You have reached your limit of 3 free stories. A story preview is shown instead.
To view more stories
(If your subscription is current,
click here to Login or Register.)
Self-Propelled Grain Carts Built From IH Combines
"Last fall we used two of these rigs to haul approximately 1,700 bu. of corn per hour away from an International 1688 combine and the combine rarely ever got ahead of us, even though we sometimes had to travel a mile to the bin and back," says Harley Van Gieson who built the two big, self-propelled grain carts out of I
..........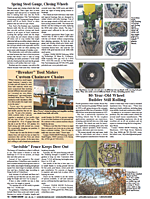
You must sign in, subscribe or renew to see the page.
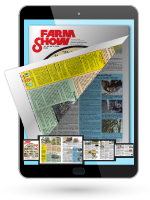
You must sign in, subscribe or renew to see the flip-book
Self-Propelled Grain Carts Built From IH Combines COMBINES Conversions 19-2-1 "Last fall we used two of these rigs to haul approximately 1,700 bu. of corn per hour away from an International 1688 combine and the combine rarely ever got ahead of us, even though we sometimes had to travel a mile to the bin and back," says Harley Van Gieson who built the two big, self-propelled grain carts out of International combines.
The Norwich, Kan., custom harvester and his son, Robert, plan to build a third cart this year. And several custom harvesters and farmers have approached the men about building carts for them.
That's because they're so maneuverable in the field and so speedy on the road.
"They steer real easy, a lot easier than any cornbine," Van Gieson says. "You can travel fully loaded in the field at 8 or 9 mph and go as fast as 16 mph unloaded."
The Van Giesons used early-1970's IH 915's that they say are available in reasonably good condition for as little as $3,000. They completely tear the machine apart from top down, saving only the lower drive train, engine, cab, hydrostatic trans-mission, and unloading system.
Next, they fabricate a new, heavier frame and subframe, using various size square and rectangular steel tubing. Everything on the combine is reversed so the grain hopper is positioned directly over the drive axle.
The men make a new heavier front steering axle for the combine out of 4-in. by 7-in. 3/8-in thick steel tubing. It's hinged in the middle to oscillate for smooth operation over rough terrain. It's also adjustable in width, up to 120-in. The steering axle is fitted with 18.4 by 26-in. rear combine tires to help give it 22-in. ground clearance.
The combine engine mounts behind and the steering axle and the radiator, which is protected by a portion of the subframe that acts as a bumper. A hood for the engine is fabricated out of sheet metal.
The grain hauler's 10-ft. by 12-ft. grain hopper box is built out of sheet steel. Mounted behind the cab, the 550-bu. hopper is angled 40 degrees on the right side so corn or wheat runs to the center for easy unloading.
"We use the top elbow and unloading tube off the combine," Van Gieson says, "but we have to fabricate the main part of the unloading auger because the original wasn't long enough to reach to the bottom of the hopper."
Rear drive tires are 24.5 by 32-in. The $3,000 pair of larger tires helps handle the weight of cart, which is 14,000 lbs unloaded.
The Van Giesons may modify engine and cab location slightly on future carts. The current design makes it difficult to replace worn out bearings in the gear box behind the engine that runs the hydrostatic pump, he says. "Time takes its toll on those bearings and some of these combines have 3,500 hours on them," Van Gieson notes.
It takes the Van Giesons two or three months to build a cart. And Van Gieson estimates he'd charge a price of about $17,000 to build one, not including the combine.
Contact: FARM SHOW Followup, Harley Van Gieson, Box 34, Norwich, Kan. 67118 (ph 316 478-2645).
To read the rest of this story, download this issue below or click
here to register with your account number.