1981 - Volume #5, Issue #5, Page #23
[ Sample Stories From This Issue | List of All Stories In This Issue | Print this story
| Read this issue]
Homemade Crop Drying Furnace
![]() |
After watching a wood-fired dryer drying corn at the mill where his brother worked, he decided to build one for his own drying system. Materials included two barrels, a length of old water pipe for the smoke stack, and some concrete blocks to support the unit. For fuel, Reichley gathers up a couple pickup loads of wood scraps.
He first removed both ends from one barrel and split it down the side. To make the firebox, about two-thirds of one end of the second barrel was removed and that barrel laid on concrete blocks in front of the dryer fan. The split barrel was spread and placed around the firebox as a heat collector. Holes were cut in the tops of each barrel and the smoke stack attached to the firebox barrel.
An electric fan pulls air through the heat collector to speed the drying process. Air temperature entering the dryer is usually about 10-15? above outside air when a strong fire is maintained in the firebox, says Reichley. Ashes are permitted to build up in the firebox. This provides a good bed for the fire, and helps prevent burnout of the barrel.
During the drying season a new fire is started each morning, and fresh fuel added about once an hour. Reichley usually lets the fire burn out at night rather than trying to keep it burning around the clock. In his setup, nearby buildings help protect the burner from wind. If there's a strong wind, he lets the fire burn out, or doesn't start it at all. He cautions that wind could fan or scatter sparks from the firebox, and suggests using a wire mesh screen over the open end of the firebox to help control flying sparks.
After grain dropped to 17-18% moisture content last fall, firing the burner was stopped and only the fan was used to pull grain down to safe storage moisture. Although the dried corn had a smoky smell, there was no apparent damage and no dockage when it was sold. Reichley has several ideas in mind for improving his original burner. First, because the outer heat collector was somewhat smaller than the fan inlet diameter, a significant amount of unheated air was drawn into the fan. Consequently, Reichley suggests using a larger barrel to match the 30 in. dia. of the fan housing. Making the heat collector longer than the firebox might also help reduce the air restriction caused by the inner barrel, he points out.
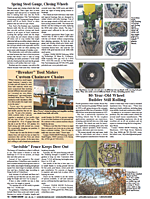
Click here to download page story appeared in.
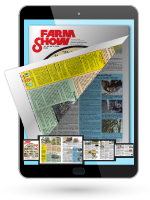
Click here to read entire issue
To read the rest of this story, download this issue below or click here to register with your account number.