Combine Makes Great Portable Loading Chute
In the past few years hog producer Allan Weitekamp, Farmersville, Ill., and his brother Dale have expanded their operation to include eight different finishing buildings. They didn't want to build a loading chute for each building so they came up with an unusual solution - they mounted a portable loading chute on an old New Idea Uni-Harvester combine.
The 3-ft. wide, 25-ft. long chute, which has corrugated steel sides and a concrete floor, is welded to the right side of the combine in place of New Idea's detachable harvesting unit. It's built in three sections, with a stationary center section and hinged front and rear sections that are hydraulically raised or lowered. To load, Weitekamp backs the combine up to the building, lowers the rear section of the chute to the ground, and then backs his semi-truck up to the front ramp, raising or lowering it as necessary.
"It really works slick and has saved us a lot of money on loading chutes," says Weitekamp, who has a 750-sow farrow-tofinish operation. "It also makes it a lot easier to get around our yard because we don't have to walk around chutes all the time. We use it at least twice a week. We bought the combine for $400 and spent less than $700 to convert it. The combine's variable speed transmission makes it easy to maneuver. We can raise the front section up to 8 ft. high to load semi-trucks or lower it all the way to the ground to load gooseneck trailers.
"The chute has a rough concrete floor and a long gradual slope so hogs walk right up it. The Uni-Harvester works perfect be-cause the engine and cab both mount on one side of the combine. With the harvesting components removed, there's a wide open area to mount the chute. Also, the combine has two sets of remote hydraulic outlets so we can operate the front and rear sections independently."
Weitekamp used 2-in. angle iron to make the chute frame and a pair of steel pipes to make hinges for the chute's front and rear sections. He welded a 4-ft. length of 4 by 6-in. steel tubing across the back of the combine, then welded the rear part of the chute frame to the tubing and the front part to the combine frame near the front axle.
He laid sheet metal and reinforcing wire along the bottom of the frame and poured a 2 1/2-in. thick concrete floor over it. He welded 32-in. lengths of channel iron vertically onto both sides of the frame, spacing them 5 ft. apart, and bolted sheets of heavy duty corrugated tin to them.
Contact: FARM SHOW Followup, Allan Weitekamp, 29002 E. Frontage Rd., Farmersville, Ill. 62533 (ph 217 227-3679).
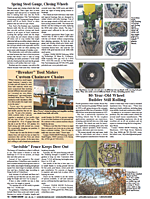
Click here to download page story appeared in.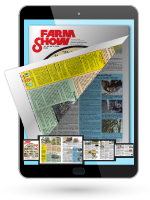
Click here to read entire issue
Combine Makes Great Portable Loading Chute COMBINES Conversions 20-5-2 In the past few years hog producer Allan Weitekamp, Farmersville, Ill., and his brother Dale have expanded their operation to include eight different finishing buildings. They didn't want to build a loading chute for each building so they came up with an unusual solution - they mounted a portable loading chute on an old New Idea Uni-Harvester combine.
The 3-ft. wide, 25-ft. long chute, which has corrugated steel sides and a concrete floor, is welded to the right side of the combine in place of New Idea's detachable harvesting unit. It's built in three sections, with a stationary center section and hinged front and rear sections that are hydraulically raised or lowered. To load, Weitekamp backs the combine up to the building, lowers the rear section of the chute to the ground, and then backs his semi-truck up to the front ramp, raising or lowering it as necessary.
"It really works slick and has saved us a lot of money on loading chutes," says Weitekamp, who has a 750-sow farrow-tofinish operation. "It also makes it a lot easier to get around our yard because we don't have to walk around chutes all the time. We use it at least twice a week. We bought the combine for $400 and spent less than $700 to convert it. The combine's variable speed transmission makes it easy to maneuver. We can raise the front section up to 8 ft. high to load semi-trucks or lower it all the way to the ground to load gooseneck trailers.
"The chute has a rough concrete floor and a long gradual slope so hogs walk right up it. The Uni-Harvester works perfect be-cause the engine and cab both mount on one side of the combine. With the harvesting components removed, there's a wide open area to mount the chute. Also, the combine has two sets of remote hydraulic outlets so we can operate the front and rear sections independently."
Weitekamp used 2-in. angle iron to make the chute frame and a pair of steel pipes to make hinges for the chute's front and rear sections. He welded a 4-ft. length of 4 by 6-in. steel tubing across the back of the combine, then welded the rear part of the chute frame to the tubing and the front part to the combine frame near the front axle.
He laid sheet metal and reinforcing wire along the bottom of the frame and poured a 2 1/2-in. thick concrete floor over it. He welded 32-in. lengths of channel iron vertically onto both sides of the frame, spacing them 5 ft. apart, and bolted sheets of heavy duty corrugated tin to them.
Contact: FARM SHOW Followup, Allan Weitekamp, 29002 E. Frontage Rd., Farmersville, Ill. 62533 (ph 217 227-3679).
To read the rest of this story, download this issue below or click
here to register with your account number.