Made-It-Myself Solar Heater
Doug Taylor of Bengough, Sask., built a solar air heater for his shop that exceeded his original expectations. “I built this heater last October, hoping it would supplement my shop’s heat pump,” he says. “When sunny, this is my primary heat source, and the heat pump doesn’t even cut in.”
Taylor’s shop measures 30 ft. by 72 ft., while the solar heater is 11 1/2 ft. high by 32 ft. long. “My walls are concrete-faced foam, but I think the design could be installed over any material,” he says. “Steel siding would work great. I used 2 by 4s upright, 4 ft. apart. Then, I stapled a wire screen between them. Each screen measures 2 ft. by 4 ft.”
Taylor added three layers of screen spaced a 1/4 in. apart. “They’re fastened at an angle, out at the bottom and in at the top. The next row higher overlaps the lower row.”
He spray-painted everything flat black and attached twin wall polycarbonate sheets to the 2 by 4s. At the bottom of each 2 by 4, he installed a 4-in. dryer flap that closes when there isn’t airflow. “This keeps cold air from entering the shop at night,” he says.
At the top, he cut a 4-in. hole for the ducting that goes to the fan. “I’ve got a thermostatic switch that I put at the top of the heater. When the temperature reaches 80 F, the fan cuts in and heats the shop. Even on -20 F days, it would get to 176 F in the panel. The air from the fan is cooler, though, ranging from 104 to 140 F. It’ll heat the shop between 53 and 57 F on a freezing winter day, plenty warm enough to work in.”
On sunny days when the temperature is around freezing and above, Taylor finds the shop stays warm enough that the heat pump won’t kick in at night. “When it gets too warm, I’ll just cover the panel with a silver reflective tarp,” he says.
Taylor found the heater to be a quick and affordable project. “It cost around $1,000 CAD ($700 USD) to build, but I already had the lumber, fan and screen. If I had to buy everything, it would probably be closer to $1,600 to $1,800 CAD.” He estimates it took him a week to build, working two to four hours daily. “If I had to do it again, I’d paint the wall flat black before installing the screens,” he says. “The black wall would probably absorb more heat that way.”
For readers interested in making their own heater, Taylor highlights the importance of improvisation. “If you happen to have lots of old windows lying around, use them,” he says. “Double-pane windows would definitely be more efficient. I used a heavy 1/8-in. mesh for the screen because I had lots on hand. However, a metal window screen would probably work about the same and be easier to work with. I went with three layers of screen. Two might work, and four might be even better. Take your time to experiment, and you’ll likely come up with some creative solutions.”
Contact: FARM SHOW Followup, Doug Taylor, Bengough, Sask., Canada (ltaylorsk@gmail.com).
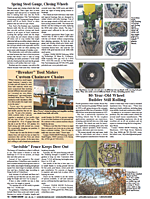
Click here to download page story appeared in.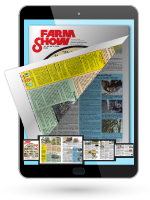
Click here to read entire issue
Made-It-Myself Solar Heater
Doug Taylor of Bengough, Sask., built a solar air heater for his shop that exceeded his original expectations. “I built this heater last October, hoping it would supplement my shop’s heat pump,” he says. “When sunny, this is my primary heat source, and the heat pump doesn’t even cut in.”
Taylor’s shop measures 30 ft. by 72 ft., while the solar heater is 11 1/2 ft. high by 32 ft. long. “My walls are concrete-faced foam, but I think the design could be installed over any material,” he says. “Steel siding would work great. I used 2 by 4s upright, 4 ft. apart. Then, I stapled a wire screen between them. Each screen measures 2 ft. by 4 ft.”
Taylor added three layers of screen spaced a 1/4 in. apart. “They’re fastened at an angle, out at the bottom and in at the top. The next row higher overlaps the lower row.”
He spray-painted everything flat black and attached twin wall polycarbonate sheets to the 2 by 4s. At the bottom of each 2 by 4, he installed a 4-in. dryer flap that closes when there isn’t airflow. “This keeps cold air from entering the shop at night,” he says.
At the top, he cut a 4-in. hole for the ducting that goes to the fan. “I’ve got a thermostatic switch that I put at the top of the heater. When the temperature reaches 80 F, the fan cuts in and heats the shop. Even on -20 F days, it would get to 176 F in the panel. The air from the fan is cooler, though, ranging from 104 to 140 F. It’ll heat the shop between 53 and 57 F on a freezing winter day, plenty warm enough to work in.”
On sunny days when the temperature is around freezing and above, Taylor finds the shop stays warm enough that the heat pump won’t kick in at night. “When it gets too warm, I’ll just cover the panel with a silver reflective tarp,” he says.
Taylor found the heater to be a quick and affordable project. “It cost around $1,000 CAD ($700 USD) to build, but I already had the lumber, fan and screen. If I had to buy everything, it would probably be closer to $1,600 to $1,800 CAD.” He estimates it took him a week to build, working two to four hours daily. “If I had to do it again, I’d paint the wall flat black before installing the screens,” he says. “The black wall would probably absorb more heat that way.”
For readers interested in making their own heater, Taylor highlights the importance of improvisation. “If you happen to have lots of old windows lying around, use them,” he says. “Double-pane windows would definitely be more efficient. I used a heavy 1/8-in. mesh for the screen because I had lots on hand. However, a metal window screen would probably work about the same and be easier to work with. I went with three layers of screen. Two might work, and four might be even better. Take your time to experiment, and you’ll likely come up with some creative solutions.”
Contact: FARM SHOW Followup, Doug Taylor, Bengough, Sask., Canada (ltaylorsk@gmail.com).
To read the rest of this story, download this issue below or click
here to register with your account number.