You have reached your limit of 3 free stories. A story preview is shown instead.
To view more stories
(If your subscription is current,
click here to Login or Register.)
Indoor Farming Uses Space Tech
A combination of NASA-funded research and native creativity is making high-volume, high-quality indoor food production possible. Anu Pure Produce (APP) does it with less light, water, and labor than other indoor farms using Controlled Environment Agriculture (CEA) technologies. Seeds are planted in self-nurturing, comp
..........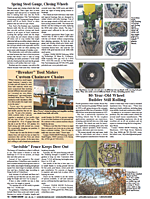
You must sign in, subscribe or renew to see the page.
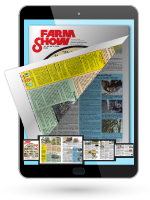
You must sign in, subscribe or renew to see the flip-book
Indoor Farming Uses Space Tech
A combination of NASA-funded research and native creativity is making high-volume, high-quality indoor food production possible. Anu Pure Produce (APP) does it with less light, water, and labor than other indoor farms using Controlled Environment Agriculture (CEA) technologies. Seeds are planted in self-nurturing, compostable seed pods placed on towers in an aerobic environment.
“The growing plants rotate under grow lights inside the growth chamber, like a chicken on a rotisserie,” says Scott Massey, Anu. “We can pack 3,920 plants in a 20-ft. shipping container. The only labor involved is planting the seed pod, harvesting the produce and cleaning the rotating tower.”
Rotating the tower so only one side is exposed to light at a time reduces the number of lights needed. This reduces fixed costs, energy costs and excess heat production.
“Plants are very light-intensive, but are able to do without the excess heat,” says Massey. “We use less energy to grow the plants than a refrigerator would to store them.”
Plant options include leafy greens, herbs, microgreens, flowers and fruiting vegetables like peppers. As a bonus, the produce is healthier too. The company claims twice the overall nutrient content on average, and 10 times the amount of certain essential nutrients, such as vitamin B.
An APP 8 by 20-ft. shipping container can hold 14 towers, each 24 in. in diameter and 80 in. tall, providing 650 sq. ft. of surface area for growing plants per tower. With its own water reservoir, pumps and nozzles for spraying plant roots, each tower can operate individually and adapt to different plant types.
Massey notes that farming is typically described in two dimensions: production per square foot or per acre.
“Our system works in three dimensions, and yields are higher per square ft.,” he says. “With aeroponics, we cut water consumption by more than 95% and eliminate pesticides and preservatives.”
A key element of the system is the integration of artificial intelligence (AI) deep learning and computer vision algorithms. The AI constantly monitors the growing plants through super-detailed images. With total control of temperature, humidity and light, it can adjust the growth factors in real time based on how the plants are doing.
Massey and co-founder Ivan Ball designed their first growth chamber for NASA while doing engineering research at Purdue University. They applied what they learned to develop APP.
First efforts focused on a prototype household appliance-type growth chamber. The idea was to produce high-quality food where it’s eaten. The home unit is now on the back burner as the company introduces the larger commercial system.
“It takes longer to bring a consumer product to market than a commercial system,” says Massey. “The University of Evansville has purchased the first of several units intended to increase the health and well-being of the community.”
Shipping container units are currently priced at $90,000, which breaks down to $150 per sq. ft. of plant canopy.
“We estimate about 60 sec. per plant to plant, to harvest and for periodic tower/reservoir cleaning,” says Massey. “Assuming $25 per hour labor, that amounts to 42˘ per plant,” says Massey.
The company has received funding from state and federal sources, including nearly a million dollars from the National Science Foundation. APP is working with ekō Solutions to produce the container systems from upcycled shipping containers.
Contact: FARM SHOW Followup, Anu, Evansville, Ind. (info@growanu.com; www.growanu.com) or ekō Solutions, 12115 Visionary Way, Fishers, Ind. 46038 (ph 317-537-0492; www.ekosolutionsllc.com).
To read the rest of this story, download this issue below or click
here to register with your account number.