You have reached your limit of 3 free stories. A story preview is shown instead.
To view more stories
(If your subscription is current,
click here to Login or Register.)
Low-Cost High Tunnel Heat
Heating high tunnels during cold snaps can be costly when growing winter vegetables and cut flowers. Curtis Millsap and Jason Hirtz found a lower-cost way to moderate temperature swings. Starting in 2023, they used modular propane heaters and ground-level convection tubing in two high tunnels to keep crops warm.
..........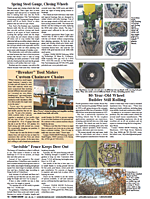
You must sign in, subscribe or renew to see the page.
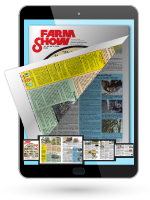
You must sign in, subscribe or renew to see the flip-book
Low-Cost High Tunnel Heat
Heating high tunnels during cold snaps can be costly when growing winter vegetables and cut flowers. Curtis Millsap and Jason Hirtz found a lower-cost way to moderate temperature swings. Starting in 2023, they used modular propane heaters and ground-level convection tubing in two high tunnels to keep crops warm.
“It’s now pretty normal every year to see a 60-degree temperature swing in a 24-hr. period,” says Hirtz.
In each case, they added frost blankets over the tubing and the crops in one of the tunnels. A grant from the USDA Sustainable Agriculture Research and Education (SARE) helped the Missouri farmers fund the project.
“We were pretty happy with the results,” says Millsap, Millsap Farms. “Using the heater without the row cover was less efficient, but it was still effective at saving the crop.”
Both farms experienced heating system failures on frigid nights but didn’t lose their crops, thanks to the added protection of row covers. The covers provided a greater margin for error and also reduced propane usage by 58%, offsetting their cost in about six weeks.
“The bottom line is, to have a predictable yield, we need to stabilize temperatures in the high tunnels when outside temperatures are unpredictable,” says Millsap. “The modular heaters on wheels gave us that. Installing a permanent heater in a greenhouse can cost several thousand dollars.”
The mobile ventless heaters allowed Millsap and Hirtz to heat only the high tunnels in production in the winter. They ran flexible ductwork across the ends of the tunnel and poly tube ducting with vent holes every 12 in. down the aisles. They also placed Inkbird thermostats at ground level throughout the tunnels as backup to the heater’s OEM thermostat.
“One thing we fine-tuned was thermostat placement,” says Millsap. “We suspended them under the row covers. The heaters didn’t kick on soon enough when on the ground or above the covers.”
Both farmers agree they would’ve lost crops without the heaters. They also saw an increased rate of growth and regrowth with the heated tunnels. In addition, they felt the decreased disease pressure recorded was due to better humidity control.
In Millsap’s case, he installed thermostats connected to Wi-Fi. This allowed him to boost the temperature in the early mornings to get condensation off the plastic.
“I was growing greens and cut flowers, and the cut flowers really benefited from the extra heat,” says Millsap.
Full details of the project can be found at https://projects.sare.org/project-reports/fnc23-1384/.
Contact: FARM SHOW Followup, Millsap Farms, 6593 Emu Ln., Springfield, Mo. 65803 (ph 417-839-0847; millsapfarms@gmail.com; https://millsapfarms.com) or Box Turtle Farm, 17679 Lawrence 2090, Mt. Vernon, Mo. 65712 (ph 314-952-5611; boxturtlefarm@live.com; www.boxturtlefarm.farm).
To read the rest of this story, download this issue below or click
here to register with your account number.