2024 - Volume #48, Issue #6, Page #16
[ Sample Stories From This Issue | List of All Stories In This Issue | Print this story
| Read this issue]
Autonomous Truck Boosts Feedlot Efficiency
![]() |
“Our truck does everything a normal feed truck driver can do, including navigating around the yard and traveling from the feed mill to the loading zone to the feeding zone,” says Jacob Hansen, ALA co-founder. “Even before we reached full autonomy, our Driver Information System increased accuracy of the amount of feed fed to a pen and consistency of feed distributed along the pen by 30 to 40 percent.”
Hansen explains that a driver typically makes one light pass with the feed truck and reverses for a second pass. As a result, cattle at the front end of a bunk are underfed, while cattle at the other end are overfed.
“Our system allows a single pass with extremely consistent feeding along the bunk,” says Hansen. “Over the past year, we moved to full autonomy. We can now operate the vehicle without a driver and complete all tasks at the same or a higher level than an extremely competent driver.
“There’s not much left from the stock feed truck,” adds Hansen. “We’ve replaced every major system, from steering power delivery to braking, as well as the central computer and lighting. All have been replaced with safety-rated custom equipment to support autonomous driving.”
For safety, the truck has a multi-level perception system for 360-degree coverage. The first tier consists of radar units with low resolution but extremely high reliability.
“Radar can see from 3 ft. to three football fields away and tell us if something is there, although not what it is,” says Hansen. “LIDAR is the second tier, providing much higher resolution and data capability (recognizing what’s there). However, it’s less reliable in rough weather conditions.”
The third tier of perception sensors are cameras that register both visible light and thermal images with high resolution but poor performance in cold weather.
“All three operate in fair weather conditions, but if visibility is impaired, the truck will automatically slow down,” says Hansen. “If a human driver can operate in the weather conditions, our truck can also.”
The next step in the process for ALA is to bring the concept to market. “The truck that’ll come to market has no cab,” says Hansen. “It’ll have a shortwave-based system for walk-behind control. This is necessary for going in or out of a storage area or a mill structure where the entire sky view is blocked, and GPS and satellite RTK correction is blocked.”
“From the beginning, all the software, hardware and sensors have been developed with an ultimate goal,” says Hansen. “We want to be able to deploy them toward other sectors, whether within ag or in mining or other industries.”
Contact: FARM SHOW Followup, ALA Engineering, 2125 Transformation Dr., Suite 1000, Lincoln, Neb. 68508 (hello@ala.engineering.com; www.ala.engineering).
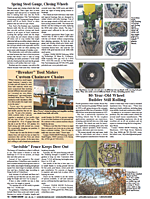
Click here to download page story appeared in.
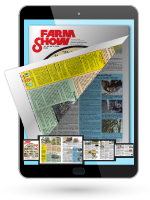
Click here to read entire issue
To read the rest of this story, download this issue below or click here to register with your account number.