You have reached your limit of 3 free stories. A story preview is shown instead.
To view more stories
(If your subscription is current,
click here to Login or Register.)
Made-It-Myself Can Storage Rack
Anthony Spiering of Powell, Wyo., has a clever storage solution for aerosol cans in his farm shop. He tends to buy glass cleaner, carburetor cleaner, spray lubricants, and similarly-sized products in bulk for cheaper shipping costs. Not only did this create lots of clutter within the shop, but the lack of organization
..........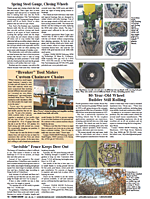
You must sign in, subscribe or renew to see the page.
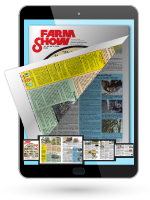
You must sign in, subscribe or renew to see the flip-book
Made-It-Myself Can Storage Rack FARM SHOP Handy Hints Anthony Spiering of Powell Wyo has a clever storage solution for aerosol cans in his farm shop He tends to buy glass cleaner carburetor cleaner spray lubricants and similarly-sized products in bulk for cheaper shipping costs Not only did this create lots of clutter within the shop but the lack of organization led him to forget what he’d already bought Spiering found inspiration for a better system from the soup can displays at grocery stores His goal was to create vertical storage where the entire stack would roll down one can after selecting the bottom one His rack organizer uses 5-ft by 10-ft 1/4-in thick steel plate to make the surface and back of the workbench He had a steel company break the sheets to make the tabletop sloping back and upper shelf Once that was done and welded solidly to the frame he began on the can racks “I took some 1/8-in by 3-in strap steel and cut pieces about 54 in long welding them in a T-shape similar to what an I-Beam looks like ” he says “After this I welded the T’s to the angled back of the workbench I spaced them about 8 1/2 in apart ” Next he attempted to design the popup ramp by first placing some flat steel to angle the cans away from the wall and then using 1-in square tubing to hold them to the tabletop Within the 13 separate slots Spiering can store and display well over a hundred cans Working with a friend the entire project took Spiering about 3 days “There was a lot of trial and error involved ” he says “While the soup rack organizers looked really simple at the store replicating the right dimensions was a struggle” The cans themselves were heavy and needed a precise amount of support to ensure they moved through the steel rack smoothly Make it too tight and the weight of the stacked cans keeps the bottom one in place so he can’t pull it out But have things too loose and cans pop out of the rack and roll on the floor He solved this problem in part with two 1-in by 2-in square “ears” on the bottom of each rack These provide enough space to work your fingers in through the bottom to pop out a can while the ears catch the next one and keep it in place Interested readers can contact Spiering directly for more details on the exact dimensions of his can rack Contact: FARM SHOW Followup Anthony Spiering 1168 Rd 19 Powell Wyo 82435 ph 307-254-2645
To read the rest of this story, download this issue below or click
here to register with your account number.