2023 - Volume #47, Issue #2, Page #03
[ Sample Stories From This Issue | List of All Stories In This Issue | Print this story
| Read this issue]
Deere Gator Converted To Electric
![]() |
“A few years earlier, I bought a crate of lithium-iron-phosphate batteries at reduced cost on Craigslist from someone’s failed EV project,” says Laine.
“The old engine was 16 hp., so I figured a 10kW power plant would give me roughly equivalent horsepower (13 to 14 hp.). Given the electric motor’s flat torque curve, I expected it would match or outperform the original.”
After stripping out fire-damaged parts, Laine removed the Gator’s original drive train with forward/reverse gearbox.
“I shopped some sites and found a supplier that could sell many of the parts needed: the DC motor, controller, gearbox, pedal, and even an instrument cluster,” says Laine.
After getting the rough dimensions of the parts, he calculated room for about 22 batteries. He placed 16 behind the motor and three under each seat in place of the old fuel tank and radiator. The batteries he had purchased were 3.2 volts, producing about 72 volts in total.
Laine estimated the project would take a few weeks once the parts arrived. He ended up working on it on and off for about 6 months. There were some things he hadn’t anticipated.
“Talking to the motor manufacturer, I was told I should have a BMS or battery management system to help protect the batteries and add safety to the design,” says Laine.
The BMS connects to each cell and balances them as needed. It also monitors voltage to make sure the batteries don’t get overcharged, overdischarged, or overheated and will power down if needed.
Laine’s first challenge was how to couple the gearbox with its differential and CV-joint axles to the Gator’s splined shafts on the forward drive axle. Limited space on the driver’s side required modifications. He coupled half of the original splined adapter from the Gator to the shell of the new CV joint. However, when he spun the axle, it bound slightly. He ended up replacing it with a Lovejoy coupling to provide needed flexibility and some cushioning to the drive. This required cutting, drilling and tapping the Lovejoy shell to attach it to one side, then machining the splined Deere connector to size and cutting a keyway in it for the other half.
“On the passenger side, I had plenty of room for the axle and CV joint,” says Laine. “I cut back the provided axle and machined a spacer to adapt it to the Gator’s splined part. I turned a piece of scrap into a bushing and coupled them together with a 3/16-in. diameter roll pin holding it together.”
The original gearbox had brakes built in. With no room for brakes on the forward drive axles, Laine installed mechanical disc brakes on the rear axles, with the option of installing dual brake pedals for independent braking.
“I made the discs from scrap steel and added go-cart brake calipers,” says Laine. “I cut the Gator’s splined hub adapters in half and machined them to accommodate the discs before welding them together. If the new roller chain ever needs adjusting, I may have to shave down the spacer blocks or disks, not ideal.”
The motor controller converts battery DC power to AC needed by the motor to control speed and current. It also provides regenerative braking back to the batteries.
Laine installed an onboard charger that charges at a rate of about 12 amps, automatically stopping when fully charged.
A DC converter takes 72-volt battery power and provides 12-volt DC at 25 amps to run the bed lifting actuator, lights, and auxiliary output plug on the rear of the machine for use with a sprayer.
“I added solid-state fuses to each battery bank,” says Laine. “The fuse manufacturer wanted something like $70 each for fuse mounts, but I drew them up on CAD and 3D printed them for cheap.”
Laine also fabricated aluminum panels to hinge down with the seats to cover the batteries. He used old road signs purchased at a swap meet.
“I needed to connect all 22 cells in parallel, so I made copper busbars with a slot on one end so any bar can be used to connect batteries end-to-end or side-to-side,” says Laine.
Along with the new electric drive, Laine refurbished and repainted the machine. The new eGator hums along at 30 mph. Based on use to date, he estimates about 3 hrs. run time. Upgrading to newer batteries would likely double that or more.
When finished, the total cost for conversion parts was about $2,000, thanks to the low-cost batteries. While not cheap, Laine compares it to buying a new Gator for $20,000.
As with several other projects, Laine has detailed the entire conversion process with many pictures on his website.
Contact: FARM SHOW Followup, Brian Laine, 7921 Wade Rd., Arlington, Wash. 98223 (ph 425-879-2890; brianlaine@aol.com; www.lainefamily.com).
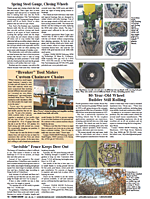
Click here to download page story appeared in.
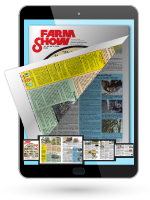
Click here to read entire issue
To read the rest of this story, download this issue below or click here to register with your account number.