You have reached your limit of 3 free stories. A story preview is shown instead.
To view more stories
To view more stories
SUBSCRIBE OR RENEW NOW
(If your subscription is current, click here to Login or Register.)2022 - Volume #46, Issue #6, Page #6
[ Sample Stories From This Issue | List of All Stories In This Issue]
Teens Start Hay Business With Rebuilt Equipment
Ryan and Kellen Riedlinger are making hay with rebuilt equipment. The two teenagers have rebuilt tractors, balers, a swather, and most recently, a DARF 917 rake. They have bought, rebuilt, sold, and upgraded with bigger, better equipment. Every piece purchased gets the same treatment.“When we get anything, we g..........
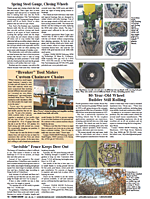
You must sign in, subscribe or renew to see the page.
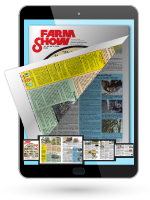
You must sign in, subscribe or renew to see the flip-book
Teens Start Hay Business With Rebuilt Equipment HAY & FORAGE HARVESTING Miscellaneous Ryan and Kellen Riedlinger are making hay with rebuilt equipment The two teenagers have rebuilt tractors balers a swather and most recently a DARF 917 rake They have bought rebuilt sold and upgraded with bigger better equipment Every piece purchased gets the same treatment “When we get anything we gut it tear it apart replace anything that needs it and paint it As a final touch we add LED lights ” says Ryan an electrical engineering student at Montana State University Bozeman “We fix everything from the transmission on a tractor to the radio air conditioning and seat ” The process has paid off repeatedly for the two hay baling entrepreneurs Ryan was 12 and Kellen 10 when they started their hay baling business using their dad’s equipment “My dad insisted we set it up as a business with a bank account and incorporating as an LLC ” recalls Ryan “We started out baling for a few neighbors and grew it from there Last year we leased or crop-shared 400 acres of hay ground which we cut baled bundled and stored We sold around 15 000 bales in 21-bale bundles We also did custom baling for around 30 customers ” They quickly outgrew their dad’s tractor and baler adding a 4630 Deere and a Massey Ferguson 1840 baler as well as two additional 30 Series Deeres which they upgraded resold and replaced with bigger more efficient tractors Other purchases have included pickups trailers a swather and more Their first baler came from Lar Voss Vol 45 No 2 via a posting on Craigslist The brothers got more than they bargained for getting a mentor in addition to the baler “Lar has been fantastic He helped us rebuild the baler ” says Ryan “He’s shown us new tools helped and advised us In return we’ve helped him on projects and I do a lot of welding for him ” The brothers found another mentor when their 4230 developed transmission problems They hired Jim Marcum an independent mechanic to do a rebuild Part of the deal was that he allowed them to help “We removed the cab ourselves and Jim split the tractor and pulled the transmission ” says Ryan “Since then he’s done several more transmissions for us and we continue to learn We’ve worked on injectors valve timing and spacing steering systems and even air conditioning He’s taught us a lot ” The repair work is done in a shop built about 4 years ago on the family farm While their dad covered the cost of the structure Ryan did all the conduit bending wire pulling and light hanging “If a breaker isn’t performing I know what’s wrong ” he says Tools for the shop have been a joint acquisition between father and sons except for major items including welders plasma cutter magnetic drill and compressor “Our business bought the heavy stuff we need to do the equipment upgrades we do ” says Ryan “Everything we buy is selected to be more efficient require less time and do a better job ” In the case of the DARF rake Ryan notes that new ones sell for $37 000 plus The brothers paid $4 250 for theirs earlier this year and the price reflects its condition There were cracks in the frame Paint was peeling and parts were rusting Rake wheel shafts and spokes were bent and bearings needed to be repacked when not replaced completely The brothers straightened wheel shafts in a hydraulic press with care to avoid damaging the machined surface Bent spokes on six of the rake wheels were sandwiched between two heavy steel plates Tightening connecting bolts between the plates brought the spokes back into line In two cases rake wheel shafts had been welded out of line with the mounting They were cut off and rewelded by Ryan Cracks were repaired and reinforced with plates welded over the repair for added strength They added hydraulic cylinders and a multifunction electric over hydraulic valve bank The latter reduced multiple sets of hydraulic hoses to the tractor with a single set This required Ryan to design and construct a control box that mounts to the tractor to control rake functions As always old paint was stripped away A coat of Corroseal was applied to neutralize rust and oxidation before parts were repainted “Our dad and Lar assisted in the restoration ” says Ryan “We spent about $7 500 on parts and upgrades like the hydraulic valve bank and control box Based on auction values for a rake in this condition we estimate it would sell for around $24 000 or $25 000 which would leave around $12 500 for our labor and profit ” However the rake is not for sale The brothers intend to keep making hay in the field and on their financial spreadsheet Upgrading and maintaining their previously owned equipment is a big part of that equation Contact: FARM SHOW Followup Ryan Riedlinger 1700 E County Rd 66 Wellington Colo 80549 ph 970-829-2988; ryan riedlinger@yahoo com
To read the rest of this story, download this issue below or click here to register with your account number.