2022 - Volume #46, Issue #5, Page #34
[ Sample Stories From This Issue | List of All Stories In This Issue | Print this story
| Read this issue]
Double-Duty Fold-Out Worktable
![]() |
“I can fold it down to 3 by 6 ft. to store in my shop or haul in my cargo trailer with other tools,” says Bond. “I do a lot of kitchen cabinets and closet storage units. It’s handy to have on-site and also at home in my shop.”
Bond had seen a similar table on YouTube and patterned his after it, but with the table saw and routers added. He started with 2-in. steel tubing for the frame. The base unit is 3 by 6-ft. with a 3 by 3-ft. wing to either side and a 3 by 6-ft. wing to the rear.
Each wing locks into place as it’s lifted. Support arms to either side are two short lengths of tubing hinged by a single bolt and attached to the main frame and wing with turnbuckles. The weight of the wing locks the arms in place. To lower the wing, Bond lifts it and kicks the hinged tubing up.
The turnbuckles are welded to either end of the support arm tubing. Eyebolts on the other ends of the turnbuckles bolt to the legs of the main table and wing frames.
“The tables need to be parallel with each other,” says Bond. “I can adjust the couplers on the turnbuckles if they aren’t in alignment.”
Bond wanted caster wheels under the table for moving it onto his trailer or around his shop. However, he wanted the table to rest on rigid feet when in use or transit. His solution was to have the legs extend past the lower horizontal tubing of the frame. He then hinged a second set of tubing with castor wheels to the insides and parallel to the long sides of the frame.
Resting on its feet, the table is stable. For transit, Bond pushes down on arms welded to the castor wheel tubing and the wheels raise the table off its feet. A corner latch on a spring secures the arms to the frame ends.
With the frame in place, Bond added tops to the center table and the wings. He used a double layer of 1/2-in., pressure-treated plywood topped by a layer of countertop Formica.
After removing the table from a 10-in. table saw, he mounted it under the main table. He also mounted two routers under the right-hand wing.
“The disadvantage is that I lost about half an inch of blade diameter due to the thicker tabletop,” says Bond. “I mounted two routers so if I’m making a cabinet door, I can set up two different bits and just go from one to the other.”
“It was easy to make and saved money over buying a kit,” says Bond.
With the two routers, the table saw, steel, and other materials, Bond estimates he has about $1,000 invested in the table. He says it’s been well worth it.
“I use it every day,” he says. “It’s super portable, but with a weight of around 300 lbs., it’s also super solid.”
Contact: FARM SHOW Followup, Chadd Bond, 6602 Gaffney Dr., Jones Creek, Texas 77541 (ph 970-683-8772; bondcustomshtx@gmail.com).
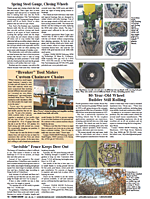
Click here to download page story appeared in.
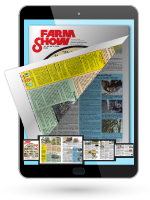
Click here to read entire issue