You have reached your limit of 3 free stories. A story preview is shown instead.
To view more stories
(If your subscription is current,
click here to Login or Register.)
Horse-Drawn 8N Has Plenty Of Power
Ben Burgess turned a Ford 8N without a motor into a powerful forecart. Intended for use on a hay tedder, it worked so well that Burgess hooked up a 6-ft. Bushhog.
“It did well with the transmission in third gear, easily getting to 550 rpm’s,” says Burgess. “If you drop it into first gear, it really whizzes. I th
..........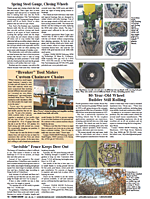
You must sign in, subscribe or renew to see the page.
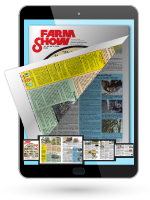
You must sign in, subscribe or renew to see the flip-book
Horse-Drawn 8N Has Plenty Of Power BALERS Ben Burgess turned a Ford 8N without a motor into a powerful forecart Intended for use on a hay tedder it worked so well that Burgess hooked up a 6-ft Bushhog “It did well with the transmission in third gear easily getting to 550 rpm’s ” says Burgess “If you drop it into first gear it really whizzes I think you could power a rotary mower in first ” He explains that running the ground speed of the wheels through the transmission produces a slower pto speed in fourth gear The pto picks up speed as you move down through the gears Burgess first saw the 8N at a friend’s house The motor had already been scrapped out He had seen mention of using old tractors for forecarts with pto on a draft animal power forum “My friend said I could have it ” says Burgess “The conversion was pretty easy as the 8N was in good shape having had minimal use ” His first step was to use another tractor to pick the 8N off the ground and spin the wheels and the pto The brakes worked and the pto had overdrive so there was no concern that a spinning pto could drive the tractor forward Burgess detached the transmission and rear end from the wide front end and narrowed it up He cut the axle down to the last two holes bringing the wheels very close together Using parts of the original axle with the spindles and bearings allowed him to maintain the correct toe-in of the wheels He made a new dolly frame for the front end as a hitch for the horse team and for connecting the dolly to the transmission housing He mounted the new axle and wheels to the frame with a salvaged wheel-bearing spindle “The spindle lets the front axle spin around when turning while bearing the weight of the tractor ” says Burgess “Without the new front end the rear would have been too heavy to pick up and attach to the pole for the horses to carry This way the horses just pull the dead weight of the tractor and implement ” Burgess also added a safety rack ahead of the operator’s platform One other change involved the brakes Since the clutch pedal was no longer needed Burgess removed it and the left brake pedal The shaft connecting the left brake pedal to the left wheel goes through the housing where the clutch was also “I changed the rotation so it’s right next to the transmission housing ” says Burgess “I welded on a piece of metal to the shaft to work as a new left brake ” This also gave him more platform space to stand on He then moved the right brake pedal forward to get more space on that side “If I have to get off in a hurry I don’t want anything in my way ” says Burgess “It works great but I’m not quite done with the conversion With its built-in hydraulics I can get lift when it’s running If I add an accumulator I’ll have lift even if it’s standing still “I also plan to add an alternator to the splined shaft where the clutch plate was and use it to charge a battery to run fans and lights ” he adds “That’s why I left a gap between the housing and the dolly wheel bracket ” Contact: FARM SHOW Followup Ben Burgess 1101 French Valley Rd Russell Springs Ky 42642 ph 270-566-1295
To read the rest of this story, download this issue below or click
here to register with your account number.