2022 - Volume #46, Issue #4, Page #24
[ Sample Stories From This Issue | List of All Stories In This Issue | Print this story
| Read this issue]
Fodder Box Produces Fresh Feed Daily
![]() |
Now American Fodder Box (AFB) is bringing his expertise to the market. The company will soon be introducing three models capable of producing 150, 500, or 1,000 lbs. of fodder per day. Each layer of the Fodder Boxes is emptied, cleaned and refilled every seven days.
“We put prototypes out to livestock producers around the country to test out our design and protocols,” says Lynn Griswald, American Fodder Box. “Based on their feedback, we made changes to our design. Now we are ready to go into production. We didn’t want to get out there until we had them working right.”
One of the changes made was to eliminate computerization and go with analog controls. Griswald notes that competitive fodder-making systems tend to be complicated.
“We wanted a system that was simple to work with,” he says. “If there is a problem, a customer can call us up, and we can tell them what to do to get the system back online.”
“Just put the seed in and shut the door,” says Blake. “The light and water turn on automatically. The Dosatron built into the system automatically delivers any additives needed.”
AFB systems have no visible plumbing. Water circulation is built into the structure, with the 1-in. sq. tubing delivering water and any additives. Polycarbonate material clads the exterior.
The American Grow Cube 150 is 4 by 4 by 7 1/2 ft. The 500 is 8 by 8 by 9 1/2 ft. and the 1,000 is 8 by 16 by 9 1/2 ft.
AFB uses steel trays to make cleaning easier. A sprinkler is attached directly to the racking. It includes a leak prevention device to prevent drips after the periodic watering. No pumps are needed as the design utilizes well water pressure. UVC lighting constantly purifies the air as it passes through the system, controlling mold spores.
Options include a backup water and pump system, should well pressure fail for a length of time. A recirculation system is also available, as is a trolley and special seeding system, a pH sensor and a pH balancing system. An optional seed cleaning and filtration system cleans seed and removes mycotoxins and other impurities that can affect germinating seed.
Blake recommends two products as key to the success of the AFB systems. One is Oxy Blast from Essential Water Solutions, a hydrogen peroxide water treatment (www.essentialwater.net). Combined with the grow cube’s integrated UV light and air circulation, it helps control mold and mildew, common problems in fodder systems.
“We’ve also found the Oxy Blast chemically lacerates the seed, doubling germination rates,” says Blake.
The second product is Fodder Flora, an AFB proprietary probiotic. It can be delivered through the Dosatron to help control mold and mildew. It can also be sprayed on the fodder as it is being removed from the tray.
“Fodder Flora helps increase Brix levels and the nutrition of the fodder,” says Blake. AFB uses a local fabrication firm to build the Grow Cubes to order. Griswald advises expecting a 4-week turnaround from order to delivery. Prices going forward will depend on changing supply costs, but Griswald suggests the 150-lb. Grow Cube will be under $5,000, with the 500-lb. unit being priced below $30,000.
“Fodder converts seed into feed at a ratio of about 1:7,” says Blake. “However, it’s not just about the cost of feed. Fodder makes its vitamins and enzymes available immediately. Hog producers eliminate medications, and milk producers report better conception rates.
Contact: FARM SHOW Followup, American Fodder Box LLC, 703 S. Aurora St., Eldon, Mo. 65026 (ph 573-375-1111; info@americanfodderbox.com; www.americanfodderbox.com).
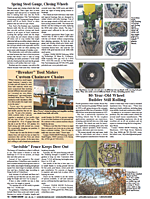
Click here to download page story appeared in.
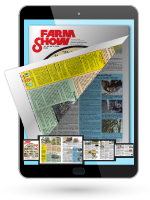
Click here to read entire issue
To read the rest of this story, download this issue below or click here to register with your account number.