You have reached your limit of 3 free stories. A story preview is shown instead.
To view more stories
(If your subscription is current,
click here to Login or Register.)
She Pelletizes Chicken Feed
Karen Johnston takes her chicken feed seriously, which is why she pelletizes it. She uses an on-farm mill to turn her loose chicken feed into tight uniform pellets.
“Anyone who has ever fed a mash diet to poultry knows the birds love to pick out the largest particles and leave the all-important ‘fines’ behind,”
..........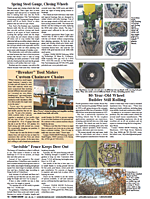
You must sign in, subscribe or renew to see the page.
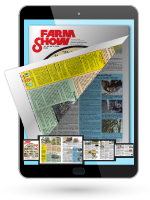
You must sign in, subscribe or renew to see the flip-book
She Pelletizes Chicken Feed GRAIN HANDLING Miscellaneous Karen Johnston takes her chicken feed seriously which is why she pelletizes it She uses an on-farm mill to turn her loose chicken feed into tight uniform pellets “Anyone who has ever fed a mash diet to poultry knows the birds love to pick out the largest particles and leave the all-important ‘fines’ behind ” says Johnston “This will change your balanced feed into a nutritionally deficient diet that can prevent your flock from reaching its full potential My solution is to pelletize the mash feed ” Johnston is the owner of Peak Poultry and raises Rhode Island Reds She is a member of the Sustainable Poultry Network dedicated to producing standard-bred heritage pastured poultry versus commercial hybrid poultry She outlined her approach with pelleted feeds in detail in Issue 120 of the American Pastured Poultry Producers Association magazine Johnston agreed to share a condensed version with FARM SHOW readers Frustrated with available commercial rations she decided to go with a custom ratio “I wanted to have as much control as I could and I wanted it adjusted seasonally ” says Johnston She realized she could use low-cost hammer mill ground feed even it if was powdery if she turned it into pellets There were low-cost pellet mills built in China available on the internet However she wanted one from a place she could call for help or parts “I bought my pellet mill from Pellet Masters ” says Johnston “They spent a lot of time talking through my options with me ” The company has a wide range of mills large and small powered by single and triple-phase electric motors gas and diesel engines or powered by belts or pto Initially Johnston considered their smallest electric pellet mill $1 385 but it would have required having her grains ground While the larger horsepower mill was almost twice as expensive as the small one the vertical design had only a 20-in sq footprint The larger mill has allowed her to avoid pre-grinding She buys cracked corn and uses full fat extruded soybean meal instead of roasted soybeans “It can pellet whole barley without any trouble ” says Johnston “The company recommended a 3-millimeter die for chickens I was pleasantly surprised that the baby chicks could eat the small pellet at 3 to 4 weeks The adults don’t mind the size either ” The pellet mill relies on compression to pelletize the feed mixture producing a hot and fragile pellet While Johnston’s pellets were not as sturdy as commercial pellets the company notes that running crumbly pellets through a second time can make them harder She found that even the second run pellets left some dust in the feed trough “To make a sturdier pellet I changed the process running the hot pellets into shallow concrete mixing tubs and setting them under a fan to cool before putting them into the feed barrels or storage bins ” says Johnston “Previously they dropped 2 1/2 ft into the feed barrels trapping heat and causing them to cool slowly Now I wait until the pellets cool to under 80 degrees before rough handling and they hold their form better ” Johnston has also begun adding Redmond Conditioner a pellet binder to help with pellet quality She estimates spending on average an additional 90 min per week pelleting her own feed Contact: FARM SHOW Followup Karen Johnston Apex N C 27523 ph 919-372-8204; peakpoultry@gmail com; www facebook com/peakpoultry or Pellet Masters 1406 Lowater Rd Chippewa Falls Wis 54729 ph 715-726-3100; info@pelletmasters com; www pelletmasters com
To read the rest of this story, download this issue below or click
here to register with your account number.