You have reached your limit of 3 free stories. A story preview is shown instead.
To view more stories
To view more stories
SUBSCRIBE OR RENEW NOW
(If your subscription is current, click here to Login or Register.)2021 - Volume #45, Issue #6, Page #3
[ Sample Stories From This Issue | List of All Stories In This Issue]
Rear Decks Triple Mower Swath
Kenny Vandeventer clips a lot of lawn fast with his 11 1/2-ft. wide, triple deck mower. Two trailing 46-in. decks sandwich the 48-in. mower deck under his Cub Cadet lawn tractor. Each is positioned to overlap the center deck by 4 in. Vandeventer explains that building the mower was an act of neighborly payback...........
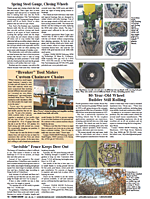
You must sign in, subscribe or renew to see the page.
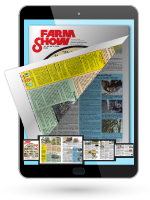
You must sign in, subscribe or renew to see the flip-book
Rear Decks Triple Mower Swath FARM HOME Lawn Mowers 31h 38 Kenny Vandeventer clips a lot of lawn fast with his 11 1/2-ft wide triple deck mower Two trailing 46-in decks sandwich the 48-in mower deck under his Cub Cadet lawn tractor Each is positioned to overlap the center deck by 4 in Vandeventer explains that building the mower was an act of neighborly payback “My neighbor used to mow my 5 acres along with his own “ says Vandeventer “When he moved out I offered to mow his lawn until his daughter and son-in-law moved in ” Vandeventer is a “garage floor” engineer To design his rear mowing system he drew a chalk line on the floor of the garage and backed the Cub with its mower deck over the line After setting the two newly purchased mower decks on either side he set a long piece of 2 by 2-in 1/8-in steel tubing on risers over them “This gave me the 9-ft length for the frame ” says Vandeventer “I could see I needed the frame 30-in front to back to support the decks ” He used the same tubing for cross members to support the 18 hp Vanguard engine he bought to power the decks The engine mounts to steel straps running between the cross-members The gas tank was framed in with 1 by 1-in steel tubing behind and to the left of the engine To bring the fuel line safely to the carburetor on the right side of the engine Vandeventer ran it through a steel tube lined with foam insulation tubing The tube was mounted to the engine support cross-members He used 1-in angle iron to make a base for the 12-volt battery to the right rear of the engine He ran the cables through a 1-in steel tube mounted to the right-hand cross-member It carries them to the front frame member where the starter switch choke cable and throttle are mounted on a flat steel plate Vandeventer gave each mower deck its own lift system He mounted a free turning 1 1/2-in pipe between the end of the frame and the engine support cross-member He did it without bearings or bushings simply nuts and bolts “I fabricated small slotted brackets from angle iron and welded them to the frame ends about 6 in from the front of the frame ” explains Vandeventer “I cut pipes to fit and inserted bolt heads into their ends with nuts outside the pipes When I had the pipes positioned where I wanted them I welded the nuts to the brackets on the frame ends and to the engine support members ” Vandeventer welded pieces of steel plate to each pipe to serve as anchors The first and the third in line are mounted at 90 degrees from the center one A chain from the center anchor connects it to the front of the deck Cables from the other two run back to pulleys on the rear frame and then down eyebolts in the rear of the deck A 1-in square tube extending back from the front frame serves as a height retention device for the lift Two short lengths of slightly larger tubing with pegs welded to their underside slide over the retainer tubing like sleeves The lead sleeve and tube rest against a bolt which can be dropped into any of a series of holes in the longer tube The second is secured in place with a set screw opposite the peg When a lever mounted to the pipe is pushed back it turns the pipe on the bolt heads lifting the deck A short steel strap pinned to the lever is notched to catch the peg on the rearmost sleeve When the lever is released from the peg and rotated forward the notched strap catches on the peg on the forward sleeve To adjust the height of the mower Vandeventer simply moves the bolt retaining that sleeve and peg The clutch lever is mounted to a similar pipe arrangement just behind the front frame Vandeventer hooked a heavy-duty spring between the lever and the mower clutch to feather the clutch on and off Rear wheels are mounted to the rear frame on 2 by 2-in tubing He welded the mounts to the rear frame at a slight rearward angle after trimming off a couple of inches of three sides of the tubing He then pinned the wheels to the fourth side While the decks can be raised and lowered mounts front and back hold the decks in place left to right On the front of each deck a 2 by 2-in tube angles down and forward from the front frame A pipe welded to the end of the tube provides a pivot point for parallel links which are pinned to a bracket extending out from the mower deck At the rear of the deck a short length of 1 by 1-in tubing welded to the wheel mount comes forward to the mower deck A short length of steel strap is attached loosely with a bolt to the tubing The other end of the strap is bolted loosely to a bracket on the mower deck As in the front the deck is restrained in side-to-side movement The mower decks were designed to receive belt drive from the front not the side Vandeventer needed to change the direction of the belt drive from the centered engine To do so he mounted double pulley drives from bearings on brackets mounted to the front side of the mower frame Belts from a double pulley on the engine driveshaft run left and right to the upper pulleys on the brackets Belts then run from the lower pulleys to the decks To make a hitch Vandeventer butt welded a 3 by 3-in piece of steel tubing to the center of the front frame It extends toward the tractor for about 10 in before dropping a few inches like a gooseneck trailer hitch to match the Cub’s hitch height A repurposed auto jack pivots on the hitch where it meets the mower frame A steel plate welded to the backside of the jack lets it pivot on the hitch and a notch on the other side of the plate locks it in place in its upright position “If I was doing it again I would overlap the mower decks by more than 4 in as when I turn sharp I sometimes leave behind strips of grass ” says Vandeventer Contact: FARM SHOW Followup Kenneth Vandeventer 3139 Indiana Rd Ottawa Kan 66067 ph 785-241-0613; kennethvandeventer@gmail com
To read the rest of this story, download this issue below or click here to register with your account number.