Massive Processor Handles Really Big Logs
Howard Ewen feeds his railroad tank car furnace with logs he processes with his massive, home-built firewood processor. Its 8-ft. chainsaw bar, 300-cu. in. Ford diesel engine, and log feeding system made from 3 sets of tracks all sit on a 40-ft. chassis. A hitch at the front end lets him move it as needed.
“I can cut logs and crowns up to 5 ft. in diameter and more than 35 ft. long,” says Ewen. “I’ve been using it for about 20 years, and it still works great.”
The tracks and much of the rest of the processor came from a crane built to lift modular homes. Ewen shortened a 60-ft. lowboy to make the chassis, moving part of the trimmings to the rear to mount the motor, hydraulic pump and cab, all from the crane.
Everything about the processor seems oversized, from the diesel that powers the main hydraulic pump to a set of 10 spool valves (also from the crane) housed in the operator’s cab.
Each of the 3 tracks that make up the 24-ft. long log transport is driven by its original hydraulic motor. The tracks sit inside a V-shaped cradle of I-beams and steel panels. Logs longer than the transport can be loaded with the smaller end sticking out over the gooseneck, which rides on a dolly made from an old semi tractor turntable.
Once Ewen has loaded a log in place, he climbs into the cab that overlooks the entire process and starts the log forward. As the log nears the chainsaw bar, it passes through 2 sets of grabber arms, also fashioned from I-beams.
Each arm consists of 6-ft. long twin I-beams joined by a shaft at their midpoint and to a hydraulic cylinder rod clevis at their top. The cylinder’s base is mounted to the top of one leg of a V-shaped steel framework that angles out from the chassis to either side of the log transport track.
A lift cylinder with a 30-in. reach runs from the base of the V to a rocker arm on the shaft connecting the I-beams. The other end of the rocker arm is attached to 2 steel plates that are hinged to the upper end of the V. The plates are identical except in length, as one is about a foot shorter than the other. The second grabber arm is a mirror image of the first.
Ewen can open the gap for even the largest log by extending both sets of cylinders at the same time. This lifts the verticals up while swinging their bases apart.
Once a log is in place, he can retract all 4 cylinders, which presses the lower ends of the arms against a log as small as 10 in. in diameter and also presses the fingers down on top of it.
Ewen also has a cylinder under the end of the track section. “If a log gets stuck, I can raise the track about 8 in.,” says Ewen. “If that isn’t enough, I can use the arms to lift the log up. I can even rotate a log by raising one arm and lowering the other.”
Once the log is in place, Ewen lowers the chainsaw bar. It is a Pond and Deck Saw that came with a drive sprocket in the bar and a chain.
“It was designed to be belted to a 35 hp electric motor, but I adapted it to use with a hydraulic motor,” says Ewen. “The bigger the log, the faster I run the engine and the faster the chain cuts.”
When faced with the OEM cost of an idler sprocket on the end of the blade, Ewen chose to make his own. He machined a pulley with a groove chain and mounted it in the bar with alternator bearings and 3/8-in. threaded rod on either side to stretch the chain.
A power steering pump raises and lowers the bar. Ewen uses the steering wheel for a valve. It allows him to feather the chainsaw bar into the log as gradually as he wants.
“I have a pressure gauge on it, but basically listen to the engine and watch the chips,” says Ewen. “If I feed it too hard, I blow the relief valve, and it stalls.”
When a section of log has been cut loose, it drops onto a steel table. The table is hinged at one end with a wagon hoist under the other end. As sections pile up, Ewen tips them off to be hauled away.
Other than the chainsaw and I-beams, which were salvaged from utility towers, nearly all the components came from the original crane. Ewen bought it after it sat unused for years. The engine needed considerable work, including recalibration of the fuel pumps feeding each cylinder. He also had to replace the head gasket.
“The spool valves were locked up,” recalls Ewen. “I set them up in my shop, and every morning and night I would spray them with some penetrating oil and tap them with a hammer. It took 2 weeks for the first one to loosen up, but when they were all loose, I found they didn’t even leak.”
Contact: FARM SHOW Followup, Howard Ewen, Jr., 6997 W State Rd. 8, Lacrosse, Ind. 46348 (ph 219 754-2365).
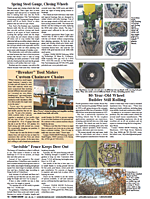
Click here to download page story appeared in.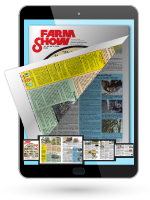
Click here to read entire issue
Massive Processor Handles Really Big Logs WOODLOT EQUIPMENT Saws Howard Ewen feeds his railroad tank car furnace with logs he processes with his massive home-built firewood processor Its 8-ft chainsaw bar 300-cu in Ford diesel engine and log feeding system made from 3 sets of tracks all sit on a 40-ft chassis A hitch at the front end lets him move it as needed “I can cut logs and crowns up to 5 ft in diameter and more than 35 ft long ” says Ewen “I’ve been using it for about 20 years and it still works great ” The tracks and much of the rest of the processor came from a crane built to lift modular homes Ewen shortened a 60-ft lowboy to make the chassis moving part of the trimmings to the rear to mount the motor hydraulic pump and cab all from the crane Everything about the processor seems oversized from the diesel that powers the main hydraulic pump to a set of 10 spool valves also from the crane housed in the operator’s cab Each of the 3 tracks that make up the 24-ft long log transport is driven by its original hydraulic motor The tracks sit inside a V-shaped cradle of I-beams and steel panels Logs longer than the transport can be loaded with the smaller end sticking out over the gooseneck which rides on a dolly made from an old semi tractor turntable Once Ewen has loaded a log in place he climbs into the cab that overlooks the entire process and starts the log forward As the log nears the chainsaw bar it passes through 2 sets of grabber arms also fashioned from I-beams Each arm consists of 6-ft long twin I-beams joined by a shaft at their midpoint and to a hydraulic cylinder rod clevis at their top The cylinder’s base is mounted to the top of one leg of a V-shaped steel framework that angles out from the chassis to either side of the log transport track A lift cylinder with a 30-in reach runs from the base of the V to a rocker arm on the shaft connecting the I-beams The other end of the rocker arm is attached to 2 steel plates that are hinged to the upper end of the V The plates are identical except in length as one is about a foot shorter than the other The second grabber arm is a mirror image of the first Ewen can open the gap for even the largest log by extending both sets of cylinders at the same time This lifts the verticals up while swinging their bases apart Once a log is in place he can retract all 4 cylinders which presses the lower ends of the arms against a log as small as 10 in in diameter and also presses the fingers down on top of it Ewen also has a cylinder under the end of the track section “If a log gets stuck I can raise the track about 8 in ” says Ewen “If that isn’t enough I can use the arms to lift the log up I can even rotate a log by raising one arm and lowering the other ” Once the log is in place Ewen lowers the chainsaw bar It is a Pond and Deck Saw that came with a drive sprocket in the bar and a chain “It was designed to be belted to a 35 hp electric motor but I adapted it to use with a hydraulic motor ” says Ewen “The bigger the log the faster I run the engine and the faster the chain cuts ” When faced with the OEM cost of an idler sprocket on the end of the blade Ewen chose to make his own He machined a pulley with a groove chain and mounted it in the bar with alternator bearings and 3/8-in threaded rod on either side to stretch the chain A power steering pump raises and lowers the bar Ewen uses the steering wheel for a valve It allows him to feather the chainsaw bar into the log as gradually as he wants “I have a pressure gauge on it but basically listen to the engine and watch the chips ” says Ewen “If I feed it too hard I blow the relief valve and it stalls ” When a section of log has been cut loose it drops onto a steel table The table is hinged at one end with a wagon hoist under the other end As sections pile up Ewen tips them off to be hauled away Other than the chainsaw and I-beams which were salvaged from utility towers nearly all the components came from the original crane Ewen bought it after it sat unused for years The engine needed considerable work including recalibration of the fuel pumps feeding each cylinder He also had to replace the head gasket “The spool valves were locked up ” recalls Ewen “I set them up in my shop and every morning and night I would spray them with some penetrating oil and tap them with a hammer It took 2 weeks for the first one to loosen up but when they were all loose I found they didn’t even leak ” Contact: FARM SHOW Followup Howard Ewen Jr 6997 W State Rd 8 Lacrosse Ind 46348 ph 219 754-2365