You have reached your limit of 3 free stories. A story preview is shown instead.
To view more stories
To view more stories
SUBSCRIBE OR RENEW NOW
(If your subscription is current, click here to Login or Register.)2021 - Volume #45, Issue #3, Page #36
[ Sample Stories From This Issue | List of All Stories In This Issue]
Compost Tools Sift And Spread
Spreading compost is easier when it’s sifted first, and Farragut Farm’s compost tools do both jobs quickly and easily. The tools were designed and built by Marja Smets and Bo Varsano to more easily apply compost to their extensive garden beds. “Because of our wet climate our compost is always wetter than is ide..........
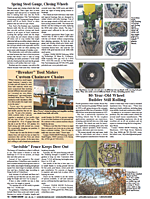
You must sign in, subscribe or renew to see the page.
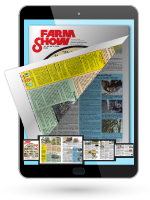
You must sign in, subscribe or renew to see the flip-book
Compost Tools Sift And Spread CROPS Miscellaneous Spreading compost is easier when it’s sifted first and Farragut Farm’s compost tools do both jobs quickly and easily The tools were designed and built by Marja Smets and Bo Varsano to more easily apply compost to their extensive garden beds “Because of our wet climate our compost is always wetter than is ideal but with our sifter we can sift a bushel in about 5 to 10 min with minimal effort ” says Varsano “Before we built our new sifter we made do with a flat screen over a wheelbarrow It was too slow and way too much effort ” The couple are market gardeners in southeast Alaska where the sifted compost plays a key role in production Farming on the edge of an inlet to Farragut Bay they average 109 in of rain a year The location which is off-grid and accessible by water only is handy for gathering seaweed to use on their garden beds “Our 30-in wide beds are often too wet for opening and closing seed furrows ” says Varsano “Instead our seeder drops seeds on the surface of the beds and we cover them with the fine sifted compost The compost is easy for the seedlings to penetrate allowing passage through it and into the light ” The sifter is a standard barrel-shaped screen that rotates in an angled framework but Varsano notes that it is the details that make it effective They include a good-sized loading chute a lip to hold the compost in at the entrance and an articulated drag bar Also important is an outflow chute that directs the larger pieces into a collection bin Grip handles front and rear make it easy to move it around They also make it easy to lift up the front end to adjust the leg height to increase or decrease the angle of the barrel The 45-in long by 26-in wide frame is a combination of scrap angle iron and rebar Varsano made the 36-in long 22 1/5-in dia barrel out of 1/4-in rock screen He wrapped it around hoops also made out of rebar Spokes made from straight lengths of rebar attached to the hoops hold the revolving barrel to a central axle The first hoop and spokes are inset a few inches to allow the loading chute to extend into the barrel The axle is a 1 1/4-in shaft salvaged from a Dodge Power Wagon winch pto shaft with its original bearings At the outflow end of the barrel a small reversible electric gear motor runs at about 20 rpm’s The chain drive to the axle reduces the speed to rotate the drum at about 7 rpm’s An articulated drag bar hangs from short lengths of pipe on the axle As the barrel rotates the drag bar gets carried a short distance sweeping compost ahead of it up the screen The constant movement keeps the screen from clogging “It’s handy to be able to reverse directions if you start to get some screen clogging or debris tangled up in the drag bar ” says Varsano Material too large to fall through the 1/4-in screen eventually reaches the overflow What doesn’t fall through is used on perennials like raspberries and rhubarb Sifted compost falls into a low cart that can be rolled under the sifter and is large enough to catch any screened material When a bed is ready for spreading the appropriate amount of compost is measured out and loaded into the spreader at the bed The spreader was designed by Varsano and Smets Drawings and plans were then provided to a local fabricator “Normally we build all our own tools but time constraints and experience welding aluminum made it a project to hire out ” says Varsano They went with all aluminum construction for weight and corrosion resistance It has 3-in wide wheels for easy rolling Push bar frame axle and wheel spokes are 1-in dia tubing The 18-in dia barrel is made with expanded aluminum mesh with 3/4-in diamond-shaped holes Thin 2-in wide aluminum strips wrap the barrel with the exception of the loading door with its 1-in border Barrel ends are solid circles of 1/4-in thick aluminum plate The 11 by 18-in hinged loading door is held in place by toggle latches If needed flow rate can be adjusted by using different sized mesh liners Smets emphasizes the importance of loading the constantly turning spreader with only enough material for the job They use about 2 cu ft of compost to spread a 1/4-in layer over their 30-in wide 30-ft long beds “We considered making the drum free-wheeling but it would have been more complex difficult to build and expensive ” says Smets “Even a free-wheeling drum will drop a not insignificant amount of compost on the ground as you wheel it around We thought it was a better alternative to figure out how full the drum needed to be to get the desired compost for a specific bed size So far it has worked out great ” For more details on Farragut Farm see a recent article by Josh Volk in Growing for Market Contact: FARM SHOW Followup Farragut Farm P O Box 1714 Petersburg Alaska 99833 ph 715 210-5383; www facebook com/FarragutFarmLLC
To read the rest of this story, download this issue below or click here to register with your account number.