You have reached your limit of 3 free stories. A story preview is shown instead.
To view more stories
To view more stories
SUBSCRIBE OR RENEW NOW
(If your subscription is current, click here to Login or Register.)2021 - Volume #45, Issue #2, Page #25
[ Sample Stories From This Issue | List of All Stories In This Issue]
Small Farm No-Till Tools
USDA researcher Ted Kornecki recently told FARM SHOW that the lack of specialized equipment for small farmers has inhibited widespread adoption of no-till and cover crops. “This is why we developed a new-style roller crimper, a powered roller crimper, a no-till drill, and a no-till transplanter for walk-behind tractors..........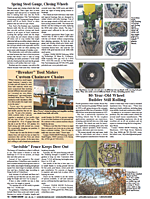
You must sign in, subscribe or renew to see the page.
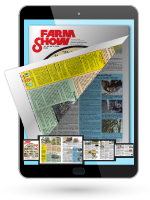
You must sign in, subscribe or renew to see the flip-book
Small Farm No-Till Tools CROPS Weed Control USDA researcher Ted Kornecki recently told FARM SHOW that the lack of specialized equipment for small farmers has inhibited widespread adoption of no-till and cover crops “This is why we developed a new-style roller crimper a powered roller crimper a no-till drill and a no-till transplanter for walk-behind tractors ” says Kornecki Roller Crimper He first came up with a 2-stage roller/crimper As a smooth roller lays down the crop a spring mechanism on the straight bar crimping roller that follows delivers stem crushing force “The crimping drum roller frame is attached to the smooth roller frame by 2 pivot points ” explains Kornecki “As it travels across the flattened crop it bounces as it jumps from one crimping bar to another ” Thanks to the smooth roller the vibration of the crimping roller is isolated from the tractor Heavy-duty springs between the 2 frames capture the potential energy as the crimping roller bounces upward This energy is released as the crimping roller bounces back down slamming the next crimping bar into the stems and restarting the cycle The more bars on the roller the more bounce The researcher has shown that enhanced crimping bars penetrate deeper into a heavy layer of cover crop than the common chevron design While the chevron design reduces bounce the straight bar design creates and takes advantage of the bounce delivering 25 percent better termination than chevron bars The 2-stage design adapts to a wide range of sizes from a 3-ft width for walk-behind tractors to a 30-ft wide roller/crimper with a 10-ft center and two 10-ft wings Pto-Driven Crimper For smaller operations using walk-behind tractors Kornecki came up with an alternative design that uses a pto-driven crimper bar Instead of a crimper roller a right angle bar stamps into the cover crop swath to crush stems A 2:1 reduction gearbox on the frame above the smooth roller reduces the pto speed of 880 rpm’s to 420 on a driveshaft that runs the full width of the crimping bar assembly Cams mounted to the shaft lift the assembly up while compressing the springs As the cams pass by the kinetic energy collected in the compressed spring is released with the crimper assembly This drives the bar down crushing stems at a rate of about 7 crimps per second delivering a 95 percent effective kill after 3 weeks Roller With Herbicide Applicator An alternative for small non-organic farmers is a roller herbicide applicator Initially the application unit was mounted to the straight bar roller/crimper implement In research trials herbicide was sprayed on continuously and intermittently and was applied to crimper bars “We discovered that herbicide application was as effective with a roller alone as with the crimping roller attached ” he says “Continuous spray behind a roller provided 98 percent termination We like the idea of farmers using equipment they already have and adapting it Our herbicide applicator can be added to any roller whether open or closed solid or basket ” The herbicide applicator uses off-the-shelf components including boom tank and control systems As designed by Kornecki it would add about $900 to a 6-ft wide roller Based on material cost of roller/crimper prototypes he estimates the 2-stage unit would run around $217 per linear foot By contrast the pto-powered roller crimper would triple the price to about $650 per linear foot “The 2-stage roller/crimper is simple enough that any farmer with a welder and a bench press should be able to fabricate it ” says Kornecki “The powered roller/crimper is more complicated ” Kornecki has rough plans available for a fabricator or farmer wishing to build a roller/crimper More exacting plans could be developed if requested he adds Walk-Behind No-Till Drill As part of the small farmer no-till emphasis Kornecki has developed other no-till tools for walk-behind tractors They include a 3-row drill and a transplanter attachment The drill frame consists of 2-in square steel tubing between steel end plates A 2:1 gearbox reduces the pto speed to 470 rpm’s This is further reduced to 360 rpm’s with a 1 3:1 chain drive mounted to a keyed driveshaft with three 18-in coulters At 360 rpm’s the coulters slice through residue and cut a notch into the soil creating a path for row openers Kornecki mounted a half bushel seed hopper to the frame He added metering units driven by a 12-volt electric motor with a built-in reduction gearbox Flexible tubes deliver the seed between double disc openers followed by closing press wheels to assure seed to soil contact Spring-loaded parallel linkage provides flotation and down force to the 3 independent row units “We used the drill with rye seed in both clay and sandy loam soils and generated an effective emergence of 83 percent ” says Kornecki No-Till Transplanter Unlike tractor-mounted transplanters requiring a driver and at least one operator the walk-behind transplanter is a one-person job Like the no-till drill attachment it has a powered no-till coulter double disc openers and closing wheels The transplant mechanism consists of 6 rectangular tubes in a rack which continuously moves from left to right across the developing row A reversing mechanism allows seedlings to be supplied from trays on both sides of the unit while walking The 880 rpm pto drive is reduced to 440 by a 2:1 belt drive and again to 110 rpm’s by 2 perpendicular bevel gears with a ratio of 4:1 A vertical shaft from the bevel gears drives a rack and pinion mechanism that moves the seedling tray in alternating directions A primary drive gear engages with a final drive gear twice its diameter to reduce the drive speed to 55 rpm’s and move the transplant rack at approximately 3 in per second The tubes mounted to the rack hold the seedlings until the bottom spring-loaded door opens over the kicker chamber The seedling drops down and is positioned in the row created by the openers The closing wheels press the furrow closed around the seedling for optimum root/soil contact “We are field-testing 2 transplanters to improve performance and to simplify their mechanisms ” says Kornecki “In our research we found less than a 10 percent variation in plan spacing uniformity ” “We have plans available for a number of the tools and can develop plans for the others upon request ” notes Kornecki Contact: FARM SHOW Followup Dr Ted S Kornecki USDA-ARS National Soil Dynamics Lab Research Unit 411 S Donahue Dr Auburn Ala 36832 ph 334 502-2745; ted kornecki@ars usda gov
To read the rest of this story, download this issue below or click here to register with your account number.