You have reached your limit of 3 free stories. A story preview is shown instead.
To view more stories
(If your subscription is current,
click here to Login or Register.)
He Built His Own Heavy-Duty Bush Hog
“It’s built strong and cost less than a commercial bush hog mower,” says Phillip Morris, Enterprise, Ala., who built his own heavy-duty, 7-ft. bush hog. It rides on 12-in. caster wheels on back and has a 1-ft. deep deck with an old-style, squared-off look.
Morris operates an automotive shop and built the 3-pt. m
..........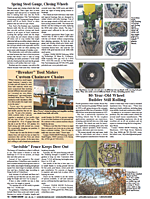
You must sign in, subscribe or renew to see the page.
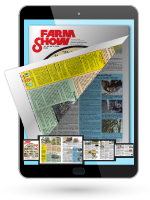
You must sign in, subscribe or renew to see the flip-book
He Built His Own Heavy-Duty Bush Hog MOWERS “It’s built strong and cost less than a commercial bush hog mower ” says Phillip Morris Enterprise Ala who built his own heavy-duty 7-ft bush hog It rides on 12-in caster wheels on back and has a 1-ft deep deck with an old-style squared-off look Morris operates an automotive shop and built the 3-pt mounted machine in his spare time and on weekends “Customers who came into the shop were shocked when they saw what I was doing They had never heard of anyone building their own bush hog ” says Morris “I looked at several different brands before I built it and decided to build something heavier I used it for the first time last spring with my Massey Ferguson 1135 2-WD tractor on about 300 brushy acres and it worked great ” He says he did a lot of mig welding and used a lot of 2-in square tubing and 3/8 and 1/2-in thick steel to build the machine “It weighs at least 2 500 lbs whereas most commercial models of comparable size weigh up to 1 800 lbs ” says Morris His cost for metal a gearbox blades and stump jumper was about $2 600 “I saved a lot of money because if you figured in the labor and cost of materials it would cost about $6 500 to build one A new bush hog of comparable size sells for about $8 100 ” says Morris Power is provided by an 85 hp gearbox welded onto a 1/2-in thick round steel plate “A lot of commercial bush hogs rust out around the gearbox and the steel plate will help keep that from happening Also the gearbox and shaft absorb most of the blade’s cutting force and the plate provides reinforcement ” A stump jumper is attached to the bottom of the gearbox and the blades are bolted to it The top of the deck was made by welding together a pair of 4 by 8 3/8-in thick steel plates and then cutting them down to 7 1/2 ft wide Each side of the deck was made from two 5-in lengths of 1/4-in thick channel iron covered by 11/32-in thick sheet metal “I spot welded the sides to make them look like they’re riveted on ” says Morris The front part of the deck is reinforced by a pair of welded-on 2-in sq tubes and also by a pair of 4-in wide 1/4-in thick flat steel bars The vertical support mounts for the 3-pt hitch are made from 2 1/2-in square tubing The arms that support the caster wheels were made by sliding lengths of 2-in square tubing inside 2 1/2-in tubing and then welding the tubes together for strength Contact: FARM SHOW Followup Phillip Morris 524 Glover Ave Enterprise Ala 36330 ph 334 347-5606; morr123isph@yahoo com
To read the rest of this story, download this issue below or click
here to register with your account number.