You have reached your limit of 3 free stories. A story preview is shown instead.
To view more stories
(If your subscription is current,
click here to Login or Register.)
“Small Changes” Improve Bandsaw
Dave Sager says his bandsaw-type sawmill is pretty standard except for several small changes he made that make it easier to use.
“I built the sawmill myself and the basic design is the same as many I’ve seen in FARM SHOW, except that I decided to put an electric drive on it,” says Sager. “I have a remote con
..........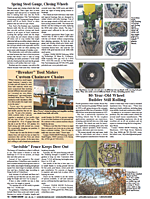
You must sign in, subscribe or renew to see the page.
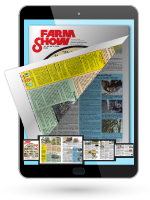
You must sign in, subscribe or renew to see the flip-book
“Small Changes” Improve Bandsaw WOODLOT EQUIPMENT Miscellaneous Dave Sager says his bandsaw-type sawmill is pretty standard except for several small changes he made that make it easier to use “I built the sawmill myself and the basic design is the same as many I’ve seen in FARM SHOW except that I decided to put an electric drive on it ” says Sager “I have a remote control with forward and reverse and speed control for the drive I can have the saw head barely moving while sawing When it gets to the end I can speed it up for return ” Sager designed the sawmill to cut 12-ft boards with a throat large enough for a 22-in log He used 2 by 6-in rectangular steel for the side rails and cross braces for the bed “I went with a $400 15-hp gas engine I had instead of the $2 200 25-hp engine people said I needed to buy ” he says “If the blade is sharp the smaller engine has no problem driving it ” The drive makes the saw run smoother and easier The saw head travels the length of the bed on spool wheels They run on an angle iron edge mounted to the top of the side rails He mounted a 1/2 hp 12-volt motor and a double sprocket drive on the saw head frame to drive a sprocket on a spool wheel The double sprocket drive with 1 large and 2 small sprockets gears down the motor speed Even greater control is provided by a circuit board wired to generate impulse current to the motor It interrupts the steady drag that would otherwise burn out the motor and gives him variable speed “I adjust the cutting speed according to the bandsaw blade ” says Sager “It can take 2 min to travel the length of the log more or less depending on how sharp the blade is ” Sager picked up half a dozen used ½-hp 12-volt motors for $100 and has put them to good use with the addition of the circuit boards A second motor raises the head to start a new log “Instead of cranking it by hand I can lift the head up 2 ft in 10 sec with the motor ” says Sager “It can be lowered with the motor or I can drop it back down by pulling a pin ” Sager’s modified log clamps alternate from either side rail and are easy to adjust Each consists of a threaded rod with a hand crank on it The rod is threaded through a nut welded to the inside lower edge of one side rail to a socket on the inside of the other side rail A threaded bracket moves on the rod as the crank turns A flat bar can slide up and down in the bracket until a set-screw type bolt with a turning knob locks it in place “The flat bar has a peg on the top that sticks out to either side ” says Sager “When a log is in position on the track to be sawn I crank the rods until the bars with the pegs are tight against the log ” The clamps hold odd-shaped logs as well as straight ones The flat bars can be set at any height on a new log and then adjusted downward as Sager removes material The clamps also work with another handy tool If a log has excessive taper Sager first raises one end with a scissors jack He then locks it into place with the clamps “Raising the smaller end lets me take off the same amount of wood with each cut ” explains Sager To make turning logs on the bed easier Sager welded a bracket to a 4-ft piece of 2 by 2-in steel tubing with a 12-volt winch mounted to the top end It can be raised about 4 ft above the bed “When I want to turn a log I raise the winch and put a half hitch on the log with a strap and roll it over ” says Sager Since building the sawmill Sager has cut up around 70 logs He has a few changes in mind Although he built the sawmill on a trailer he finds he prefers a stationary setup He also plans to add more clamps “I have 3 clamps on each side but adding more would let me hold smaller logs ” says Sager Contact: FARM SHOW Followup David Sager 15 Rosebush Rd Stirling Ont Canada K0K 3E0 ph 613 395-2173; david sager@bell net
To read the rest of this story, download this issue below or click
here to register with your account number.