You have reached your limit of 3 free stories. A story preview is shown instead.
To view more stories
(If your subscription is current,
click here to Login or Register.)
Machine Uses Air Blast To Peel Garlic Fast
Gary Price blows away garlic peels with air pressure using round-bottom cups. His homemade machine helps him process 20,000 lbs. of garlic a year.
“We were growing 2 acres of garlic every year, pickling them, flavoring vinegar, and using it in a jalapeno jelly,” recalls Price. “We shipped them all over the U.S.
..........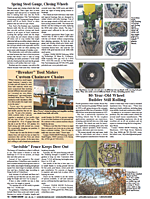
You must sign in, subscribe or renew to see the page.
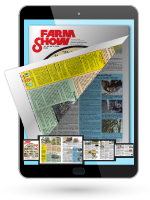
You must sign in, subscribe or renew to see the flip-book
Machine Uses Air Blast To Peel Garlic Fast CROPS New Techniques Gary Price blows away garlic peels with air pressure using round-bottom cups His homemade machine helps him process 20 000 lbs of garlic a year “We were growing 2 acres of garlic every year pickling them flavoring vinegar and using it in a jalapeno jelly ” recalls Price “We shipped them all over the U S and as far away as Europe and Australia ” Price needed a way to peel them and nobody had a commercial peeler for sale He couldn’t even find a large commercial processor who would let him see one When he finally did the machine was impressive It was a 20-row machine with air supplied by a compressor on a 454 Chevy engine However the concept was simple “You can put a few cloves in a container squirt them with 120 lbs of air pressure and the peels will blow right off ” says Price “You can even do it by putting a clove in your palm close the fingers over it and put the air nozzle tip between your thumb and forefinger ” Once he knew what worked Price went to work on a small 1-row peeler Instead of a Chevy engine he had a double lung 10 hp air compressor “My uncle in California had these plastic cups rounded on the bottom with a threaded female lead for 7/8-in bolts ” he says “I welded the bolts to a length of roller chain and ran it across and under a sheet of plywood mounted to a framework made with 1 by 3-in steel tubing ” Price mounted sprockets for the chain on either end with a crank to turn it by hand to his right He originally welded the bolts to the chain in a pattern that would have the cups side by side After some experimenting he opted for a cup on every other bolt Three cups at a time pass under a raised platform on the table with holes and air nozzles to match the three cups He ran a 1-in air hose to a foot pedal where it split 3 ways As the chain revolves 4 or 5 cloves are dropped in each cup When a group of 3 cups arrives under the air jets Price steps on the foot pedal and the peels are blown away Peels are sucked away by a dust collector type hood underneath the raised platform When Price cranks the chain around to bring three more cups into place the freshly peeled cloves drop into a bin at the end of the table “It was all the little compressor could do to handle the 3 cups of garlic ” says Price “I could have used a larger compressor but then I would have needed to add more lines of cups to justify it With this one I can do about a pound of garlic per minute and I only have about $100 to $150 in it ” Price credits his daughter’s marketing skills with driving the processed garlic business At the time he was also operating a custom cabinetmaking business and doing business nationwide “We would return through Chicago after delivering cabinets and pick up 50-gal drums of vinegar ” recalls Price “UPS would drop off a semi each week from October through November as we shipped out product ” Price shut down the business when his daughter decided to spend more time with her kids The peeler now stands largely unused as Price only raises garlic for the family and to maintain his seed stock For Price that means growing 200 lbs of garlic and planting back about half that Now he wants to share what he learned “I don’t want to sell my peeler or make them ” he says “However if anyone wants to make one they are welcome to come and take all the pictures of it they like ” Price also is willing to help should any FARM SHOW readers care to learn more about the garlic processing business Contact: FARM SHOW Followup Gary Price 3520 30th St NW Minot N Dak 58703 ph 701 839-6036 or 701 721-9560; gprice@srt com
To read the rest of this story, download this issue below or click
here to register with your account number.