You have reached your limit of 3 free stories. A story preview is shown instead.
To view more stories
(If your subscription is current,
click here to Login or Register.)
Fuel-Saving Conversion For Trucks, Tractor Engines
"We alter expansion factors in tractor and truck engines by installing turbochargers and reworking the cam-shaft, compression ratios, and governor ratios," says Stoney Pipes, Rocheport, Mo., who runs "The Power Squeeze Company" ù a custom engine rebuilding outfit that reworks conventional engines into "high thermal exp
..........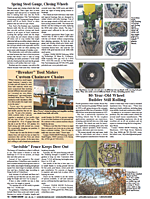
You must sign in, subscribe or renew to see the page.
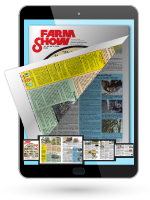
You must sign in, subscribe or renew to see the flip-book
Fuel-Saving Conversion for Trucks, Tractor Engines ENGINES Engines 10-3-35 "We alter expansion factors in tractor and truck engines by installing turbochargers and reworking the cam-shaft, compression ratios, and governor ratios," says Stoney Pipes, Rocheport, Mo., who runs "The Power Squeeze Company" ù a custom engine rebuilding outfit that reworks conventional engines into "high thermal expansion engines," boosting gas mileage "up to 50% or more."
Pipes contacted FARM SHOW after reading about Utah inventor Mike Brown who rebuilds engines by installing remanufactured camshafts and 16:1 compression pistons to boost gas mileage by up to 50% on many vehicles (Vol. 10, No. 1). Brown has worked primarily on cars and pickups. Pipes, a former Allis-Chalmers Co. mechanic, says he has successfully converted tractors and semi-truck engines for years.
"Several years ago a farmer brought me a 7000 series Allis Chalmers tractor that had problems with overheating, cracked heads and short-lived injectors. I decided to experiment by regrinding the camshaft. That eliminated all problems related to excessive heat and the farmer said it burned less fuel. I later obtained different pistons, sleeves and rings and converted a 7060 Allis-Chalmers. We installed a reworked camshaft, along with the new pistons, and horsepower was boosted and fuel consumption was cut by more than 60%. Since then, I've changed over 14 more engines of different brands and all have produced similar results, including an 855 cu. in. Cummins semi engine which doubled mileage on an18-wheeler from 3¢ mpg to, 7¢ mpg," says Pipes.
The cam is reground so that it leaves the intake valve open halfway through the compression stroke and begins opening the exhaust valve before bottom dead center on the power stroke. This lets the fuel mixture expand twice as much and de-creases the amount of compression at low rpm's and increases it at high speeds.
Because of the increased expansion, Pipes rebuilds the turbo charger with a large housing and wheel to boost air flow and changes the governor ratios to adapt to the other changes.
"The changes decrease exhaust temperatures and increase engine efficiency by 40 to 50%. Engine wear is greatly reduced and we've been ableto lower fuel consumption on Allis Chalmers 301 engines from 8 gal. per hour to 4 gal. per hr. doing fieldwork," says Pipes.
The biggest problem with converting gas engines, according to Pipes, is that the no-lead gas currently on the market doesn't work as well as leaded gas in high-compression engines. Conversion of gas engines costs about the same as a normal overhaul. Cost to completely modify an AC 301 diesel tractor engine is about $4,000, or the cost of an engine rebuild.
"Every manufacturer in the country should be building engines this way right from the factory," says Pipes.
For more information, contact: FARM SHOW Followup, Stoney D. Pipes, Rt. 1, Box 49A, Rocheport, Mo. 65201 (ph 314 698-3995).
To read the rest of this story, download this issue below or click
here to register with your account number.