2020 - Volume #44, Issue #3, Page #33
[ Sample Stories From This Issue | List of All Stories In This Issue | Print this story
| Read this issue]
Welding Table Pivots On Bowling Ball
![]() |
“Once I got the idea of an adjustable welding table, using a bowling ball for the pivot point just came to me,” says Muhs. “I just let the pressure off a little, tilt or rotate the table to suit, and then lock it down again.”
Steel for most of the table came from his scrap pile. Two old brake rotors used to sandwich the bowling ball came from a salvage yard, while the old ball was given to him by an area bowling center.
Muhs built the table from the ground up, starting with feet made from 36-in. long, 2 by 3-in., 5/16-in. steel tubing. A 26-in. long crossbeam of 4 by 4-in., 1/4-in. thick steel tubing is centered on the feet.
The crossbeam serves as the base for the jack that locks the table in position. It also is the base for the four, 27-in. long legs made from 3/16-in. thick, 1 1/2-in. square tubing.
The legs are spaced to allow the brake rotor ring that supports the bowling ball free movement. A piece of pipe welded to the bottom of the rotor, fits over the head of the hydraulic jack’s ram.
The top rotor is bolted to pieces of angle iron that are in turn welded to the tops of the 4 legs. When the jack ram is extended, the lower rotor pushes the bowling ball against the upper rotor, locking the table into place.
“Initially, I drilled a hole through the thumb hole and halfway into the bowling ball for a 3/4-in. shaft butt welded to the table,” recalls Muhs. “It didn’t work as planned. When I took pressure off the ball to turn the table, the shaft would spin in the ball.”
Muhs solved the problem by drilling a 1/4-in. hole beside the original shaft hole. He then welded a 1/4-in. rod to the shaft.
“I put J-B Weld around the shaft and put it back together with the ball,” says Muhs. “Now it works like I wanted.”
Muhs added 2 foot pedal controls to make operating the table even easier. A 3 by 4-in. pedal is welded to the end of a length of pipe that fits into the jack’s piston assembly socket. The purchased spring retains the pipe in the raised position.
He also welded 2 rectangular plates to a round steel plate. The plate is welded to the end of a 1/2-in. pipe slotted to fit over the release screw on the jack. An L-shaped steel strap supports the pipe.
“I simply step down on one of the steel plates to loosen or tighten the release screw,” says Muhs. “To tighten the table in place, I step on the spring-retained foot pedal to jack the ball up.”
Contact: FARM SHOW Followup, James Muhs, 4962 N. Oak Tree Rd., Claremont, Ill. 62421 (jmuhs11@hotmail.com).
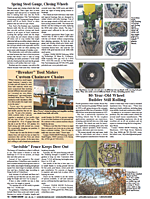
Click here to download page story appeared in.
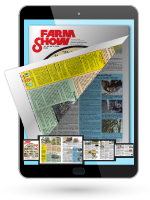
Click here to read entire issue
To read the rest of this story, download this issue below or click here to register with your account number.