You have reached your limit of 3 free stories. A story preview is shown instead.
To view more stories
(If your subscription is current,
click here to Login or Register.)
They Restore Windmill Gear Cases To Better Than New
Paul Petrocchi at American Windmill restores gear cases to better than new with a special oil seal and roller bearings.
“One of the reasons we started installing roller bearings and oil seals was having to throw away the clothes I wore when working on windmills as oil from gear cases went everywhere,” says Pet
..........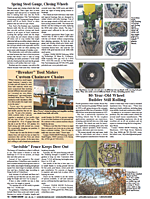
You must sign in, subscribe or renew to see the page.
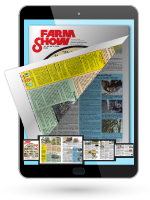
You must sign in, subscribe or renew to see the flip-book
They Restore Windmill Gear Cases To Better Than New ENERGY Wind Power Paul Petrocchi at American Windmill restores gear cases to better than new with a special oil seal and roller bearings “One of the reasons we started installing roller bearings and oil seals was having to throw away the clothes I wore when working on windmills as oil from gear cases went everywhere ” says Petrocchi “I wanted to be able to go up the tower and have it be a clean and safe place to work ” Petrocchi and his wife Ellen Sattler do complete restorations of old windmills as well as install new ones mostly in western and southern states They have worked on windmills for more than 35 years Petrocchi began as a college intern in a windmill factory carving blades While he works up on the towers Sattler handles the business end as well as building towers and operating cranes and trucks She is also his main consultant “She can’t use a tool but she can see how it should be used to resolve a problem and explain it to me ” says Petrocchi Although their specialty is Aermotor they work on all brands and models of windmills “We’ve worked on more than 100 different models from different manufacturers ” says Petrocchi “Most of the work I do is on the platform We also do some in the shop We’ll restore a gear case like it was just factory made ” Upgrading gear cases to prevent leaks is a unique specialty and spans all makes and models He explains that with the exception of one made by Duplex most machines were not sealed off or not sealed off well “Companies did all kinds of things to seal off the nose while some just dumped in oil ” says Petrocchi “If you can seal it off the oil stays in the tank and stays cleaner ” To seal off a gear case Petrocchi often has to modify the nose of the main casting to accept the roller bearings and oil seal “We end up cutting off from 2 to 5 in of the nose of the main gearbox We then make a bell shape flange to fit inside the nose ” says Petrocchi “It expands when heated to seal tightly to the old case ” He explains that the flange has to be fabricated carefully If it expands too much it can shatter the old cast iron gearbox Some rebuilders will put a needle roller bearing in but not the hardened shaft and needle housing The shaft is key and has to match the housing in hardness “We are fortunate to have an older machinist who is really into metallurgy ” says Petrocchi “You need to know what the metal will do If you build it like the hub of a car wheel with a hardened shaft a great set of bearings and an oil seal you have it ” If a FARM SHOW reader has a windmill or gear case to be restored or upgraded Petrocchi suggests sending him pictures the make and model as well as the diameter of the fan “We need pictures of the gearbox any ID marks the tail and the tower as well as dimensions of cross members and the ladder ” Petrocchi recommends anyone interested in windmills and windmill restoration should subscribe to the Windmill Gazette He also recommends attending the Windmill Technology Certification Workshop Vol 38 No 6 at New Mexico State University Sattler recommends readers contact them by phone or email as she and Petrocchi are often traveling for business Contact: FARM SHOW Followup American Windmill 5981 Silver Ridge Lane Placerville Calif 95667 ph 530 644-3008; ellen@windmills net
To read the rest of this story, download this issue below or click
here to register with your account number.