You have reached your limit of 3 free stories. A story preview is shown instead.
To view more stories
(If your subscription is current,
click here to Login or Register.)
He Converts Big Bales Into 21-Bale Bundles Of Small Bales
Rodney Boll can turn big square bales into small bales at a rate of 300 to 500 an hour and just as quickly, turn them back into a 21-bale pack for shipping. He even captures chaff and returns it to the bales. The system solves a labor problem while still producing the small bales of hay that the market wants.
..........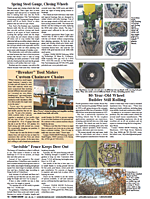
You must sign in, subscribe or renew to see the page.
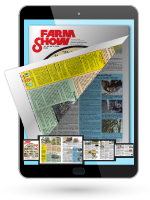
You must sign in, subscribe or renew to see the flip-book
He Converts Big Bales Into 21-Bale Bundles Of Small Bales BALE HANDLING Rodney Boll can turn big square bales into small bales at a rate of 300 to 500 an hour and just as quickly turn them back into a 21-bale pack for shipping He even captures chaff and returns it to the bales The system solves a labor problem while still producing the small bales of hay that the market wants “We sell small bales but there is a lack of labor to handle them ” explains Boll “We custom-bale for other farmers in large square bales With the rebaling system we can bale our hay in big square bales get them off the field quickly and then convert them to small bales when we have the time ” Boll has been rebaling his big squares for about 6 years ever since he first bought a Bale Destroyer Vol 37 No 3 Since then he has worked with inventor Levi Stoltsfus as it has been refined and renamed from Bale Destroyer to Bale Destructor and most recently Bale Converter The concept has worked so well for Boll that he has 2 rebaling centers in barns on the farm When one barn burned down recently he rebuilt with rebaling in mind “We built a 60 by 144-ft barn with large overhead doors to the sides of the gabled ends for a drive-through and a door to one side that leads to a loading dock for trailers ” says Boll “Most of the barn is hay and straw storage with the bale conversion system in one corner ” Building from scratch allowed Boll to design a labor-saving - and even chaff- saving system - that includes 90 ft of in-floor 11-in augers covered by steel grill The V-shaped auger channels are 42-in wide at the top and are laid out in a U-shape The Bale Converter is on the right side the Massey Ferguson 1840 baler is in the center of the U and the Bale Baron 21 Pack Vol 39 No 2 is on the left side Boll’s design allows the material to automatically feed through the system No labor is involved from the time the large square bale is set down to be shredded until the package of 21 small bales is removed at the other end All 3 in-floor augers feed a vertical auger that sends the chaff onto the baler feeder bed “Setting it up in a U-shape allows one person to control the equipment from the center of the action ” says Boll “It saves a lot of walking while you’re watching to make sure there is no problem ” While a tractor powers the baler the Bale Converter and the Bale Baron run on hydraulics provided by two 25 gpm pumps The pumps in turn are powered by two 40 hp 3-phase electric motors Boll relies on 2 variable frequency drives to modify single-phase power to drive the motors Push button switches on the control panel start and stop the motors while toggle switches to the right control 12-volt power The Bale Converter has a 12-volt delay that pauses the in-feed conveyor “When the hopper is full of crop we can push a button to start a timer that stops the conveyor for a preset amount of time usually about 40 sec ” explains Boll “There is a switch to supply the control box with power and a switch to supply power to the fans on the knotter ” Hydraulic fluid is channeled through steel tubing from the pumps to hoses that drop down to the Bale Converter and the Bale Baron Return oil goes through a cooler mounted on the wall of the building “It took 3 months to get it all set up but it works well and we have virtually zero waste ” says Boll “We can handle 15 to 20 large square bales an hour ” The speed of rebaling depends largely on the type of material in the large bale The finer the material the faster the system can run The control board offers push-button stop and start for all 3 components “The one change that we will make at some point is to increase the size of the grates ” says Boll “We sized them to ensure a foot wouldn’t get caught in them but the openings are a little too small for the chaff to flow through ” Contact: FARM SHOW Followup Rodney Boll 1802r Cloverleaf Rd Mt Joy Penn 17552 ph 717 278-6916; rodboll80@gmail com
To read the rest of this story, download this issue below or click
here to register with your account number.