Amazing Built-From-Scratch Case 150 Steam Engine
The first Case 150 steam engine built in more than a century has come to life, thanks to Kory Anderson and a team of helpers. The new “old” engine was showcased at the James Valley Threshing Show, Andover, S. Dak., last September. At 150 hp., the Case 150 has been described as the world’s largest steam engine. Only 9 were built between 1905 and 1907, and none survived.
“About 8,000 people from around the world saw it in action at the show,” says Anderson. “We hooked 12 two-bottom plows together and hooked them onto the Case 150 so people could see it work.”
Anderson is only 35, but recreating the Case 150 has been a longtime dream. He has steam in his blood, having attended his first steam engine show when he was 5 days old. Many more steam shows later, while still in high school, he restored a 65 hp. Case steam engine.
“Through the process, my dad taught me a lot about rebuilding parts and the process of putting together a sound performing engine,” says Anderson.
After studying mechanical engineering and working in welding and machining, Anderson started his own business making patterns for a local foundry. While visiting Case archives in 2006, he got copies of engineering drawings for the 150 and started working on his dream.
The first step in the process was creating CAD models from the drawing. That took 2 years of nights and weekends. In 2008 he began making wood patterns, beginning with the cylinder head. Over the next 6 years he made more patterns as he had time. His dad helped out by ordering a boiler built to Case 150 specifications. In 2014, Anderson purchased the foundry he had been making patterns for.
“It was early in 2017 when I realized that I have the rest of my life to work, but we now have the team and resources to do this project, so we need to get after it,” recalls Anderson, who by then was running 3 ag machinery related businesses.
He enlisted the help of close friend Gary Bradley of Sheridan, Wyo. The two got busy in Bradley’s shop for weeks at a time. Patterns turned into castings, and a former employer, Jim Briden, machined the flywheel on his 50-in. lathe. Other work continued into 2018, including a temporary fixture on which to assemble the engine as it would sit on the boiler. By January of 2018, the only significant parts left to build were the ring gear, intermediate gear, bull gears and front door.
“In the first 4 months of 2018 we cast the majority of parts at the foundry and finished machining the cast engine frame, which weighs nearly 1,000 lbs.,” says Anderson. “Once we had the engine frame and bearing housings machined, we installed them into the fixture built for assembly. Once the bearings had been Babbitted, we line-bored them all to size, giving them a clearance of .006 for the 4 5/8-in. crankshaft.”
With components machined and bearings prepared, the Case 150 team began assembly. One of the last projects was to build the massive, 8-ft. diameter rear wheels. The steel parts were fabricated and lugs, hubs and bull gears were machined. With the help of friends, the real work began, according to Anderson.
“We installed over 1,200 hot, 3/4-in. rivets,” he says. “Most of them we were able to squeeze with the large hydraulic squeezer I had designed. When we got to riveting in the drag links, around 80 rivets had to be put in by hand with the air hammer because we didn’t have any more room to get the squeezer in.”
Each wheel took 3 days to build. Once they were powder-coated, they joined the rest of the engine in Bradley’s shop. In early May assembly began with the engine assembly being lifted off the fixture and onto the boiler. By July a water tank had been completed by a fellow steam buff in Manitoba. Woodwork, decals and final machining and fabrications were underway with everything completed in time for the show.
“We lit the first match on 8/18/18 and fired it for 4 days running, testing and breaking in the engine and gearing,” says Anderson. “The engine ran perfectly. We didn’t have trouble with any of the bearings overheating, and the valve settings were spot on.”
Anderson estimates the total cost of the built-from-scratch steam engine at $1.5 million, including donated labor. He credits help from about 50 people doing the 4,000 hrs. of work the task took. What they accomplished was actually better than the original engine.
“The level of accuracy and tolerance that we built into this engine was not practical in the early 1900’s with the tools they had at the time,” says Anderson.
Anderson and his parents absorbed most of the cost. “I was raised with a passion for preserving history,” he says. “Operating the 150 at the show was a great opportunity to get all our steam engine friends together and celebrate bringing that piece back to life.”
For a detailed account of the entire process, including a last minute hitch, visit the Anderson Industries website listed below. Photos and stories can be found under the News heading.
Contact: FARM SHOW Followup, Kory Anderson, Anderson Industries, 200 4th Ave. S.E., Mapleton, N. Dak. 58059 (ph 833 559-3434; info@anderson-industries.com; www.anderson-industries.com).
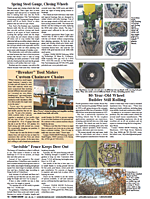
Click here to download page story appeared in.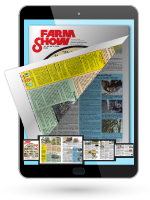
Click here to read entire issue
Amazing Built-From-Scratch Case 150 Steam Engine TRACTORS Antiques The first Case 150 steam engine built in more than a century has come to life thanks to Kory Anderson and a team of helpers The new “old” engine was showcased at the James Valley Threshing Show Andover S Dak last September At 150 hp the Case 150 has been described as the world’s largest steam engine Only 9 were built between 1905 and 1907 and none survived
“About 8 000 people from around the world saw it in action at the show ” says Anderson “We hooked 12 two-bottom plows together and hooked them onto the Case 150 so people could see it work ”
Anderson is only 35 but recreating the Case 150 has been a longtime dream He has steam in his blood having attended his first steam engine show when he was 5 days old Many more steam shows later while still in high school he restored a 65 hp Case steam engine
“Through the process my dad taught me a lot about rebuilding parts and the process of putting together a sound performing engine ” says Anderson
After studying mechanical engineering and working in welding and machining Anderson started his own business making patterns for a local foundry While visiting Case archives in 2006 he got copies of engineering drawings for the 150 and started working on his dream
The first step in the process was creating CAD models from the drawing That took 2 years of nights and weekends In 2008 he began making wood patterns beginning with the cylinder head Over the next 6 years he made more patterns as he had time His dad helped out by ordering a boiler built to Case 150 specifications In 2014 Anderson purchased the foundry he had been making patterns for
“It was early in 2017 when I realized that I have the rest of my life to work but we now have the team and resources to do this project so we need to get after it ” recalls Anderson who by then was running 3 ag machinery related businesses
He enlisted the help of close friend Gary Bradley of Sheridan Wyo The two got busy in Bradley’s shop for weeks at a time Patterns turned into castings and a former employer Jim Briden machined the flywheel on his 50-in lathe Other work continued into 2018 including a temporary fixture on which to assemble the engine as it would sit on the boiler By January of 2018 the only significant parts left to build were the ring gear intermediate gear bull gears and front door
“In the first 4 months of 2018 we cast the majority of parts at the foundry and finished machining the cast engine frame which weighs nearly 1 000 lbs ” says Anderson “Once we had the engine frame and bearing housings machined we installed them into the fixture built for assembly Once the bearings had been Babbitted we line-bored them all to size giving them a clearance of 006 for the 4 5/8-in crankshaft ”
With components machined and bearings prepared the Case 150 team began assembly One of the last projects was to build the massive 8-ft diameter rear wheels The steel parts were fabricated and lugs hubs and bull gears were machined With the help of friends the real work began according to Anderson
“We installed over 1 200 hot 3/4-in rivets ” he says “Most of them we were able to squeeze with the large hydraulic squeezer I had designed When we got to riveting in the drag links around 80 rivets had to be put in by hand with the air hammer because we didn’t have any more room to get the squeezer in ”
Each wheel took 3 days to build Once they were powder-coated they joined the rest of the engine in Bradley’s shop In early May assembly began with the engine assembly being lifted off the fixture and onto the boiler By July a water tank had been completed by a fellow steam buff in Manitoba Woodwork decals and final machining and fabrications were underway with everything completed in time for the show
“We lit the first match on 8/18/18 and fired it for 4 days running testing and breaking in the engine and gearing ” says Anderson “The engine ran perfectly We didn’t have trouble with any of the bearings overheating and the valve settings were spot on ”
Anderson estimates the total cost of the built-from-scratch steam engine at $1 5 million including donated labor He credits help from about 50 people doing the 4 000 hrs of work the task took What they accomplished was actually better than the original engine
“The level of accuracy and tolerance that we built into this engine was not practical in the early 1900’s with the tools they had at the time ” says Anderson
Anderson and his parents absorbed most of the cost “I was raised with a passion for preserving history ” he says “Operating the 150 at the show was a great opportunity to get all our steam engine friends together and celebrate bringing that piece back to life ”
For a detailed account of the entire process including a last minute hitch visit the Anderson Industries website listed below Photos and stories can be found under the News heading
Contact: FARM SHOW Followup Kory Anderson Anderson Industries 200 4th Ave S E Mapleton N Dak 58059 ph 833 559-3434; info@anderson-industries com; www anderson-industries com