You have reached your limit of 3 free stories. A story preview is shown instead.
To view more stories
(If your subscription is current,
click here to Login or Register.)
Loader Modified With Low-Cost Quick Attach
Robert Devine turned his conventional loader and bucket into a versatile quick attach system for less than $100. All it took was a little work with a grinder and welder.
“I looked into buying a quick-attach system, but I couldn’t justify the cost,” says Devine. “My concept required less fabrication than other p
..........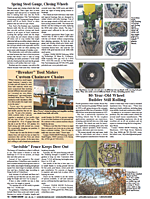
You must sign in, subscribe or renew to see the page.
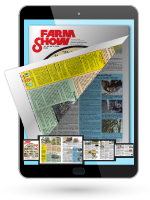
You must sign in, subscribe or renew to see the flip-book
Loader Modified With Low-Cost Quick Attach HITCHES Robert Devine turned his conventional loader and bucket into a versatile quick attach system for less than $100 All it took was a little work with a grinder and welder “I looked into buying a quick-attach system but I couldn’t justify the cost ” says Devine “My concept required less fabrication than other plans I saw ” Devine used a combination of tabs and ears to adapt equipment to his system The biggest challenge was simply separating the bucket from the loader arms “It was welded on very solid but I used a torch and a real thin grinding wheel to cut it away ” says Devine “I had to take it very slow so I could save the pivot pin brackets and their alignment brace rods that allowed the bucket to tilt ” Devine reused the brackets and rods when fabricating the pick-up portion of his quick-attach They consist of two 12-in long 1/4-in thick 4-in channel irons They are sized to match the distance between the brackets when they were on the buckets He cut out half circles from either end of the channel irons and welded the brackets and the brace rods into place The bucket side of the quick-attach consists of a 5/8-in thick tab near the top edge of the back of the bucket The female or loader arm channel irons tip under and up to hook the tab It slips 1 to 1 1/2 in into the channel iron “I didn’t want the tabs to go in too far or it would hit the upper bracket bushings ” says Devine In order to get the correct spacing he first spot-welded the tab in place on the loader arm channel iron He then positioned the bucket where he wanted it and bolted and welded the tabs in place before removing the spot weld With the tabs in place he welded ears to the bucket to either side of the lower ends of the channel iron Holes drilled through the ears and the channel iron let him pin the bucket in place “I put a bushing with a grease zerk between the holes of the channel iron just to make it easier for the pin to slip in and out ” says Devine “I have to get off the tractor to insert the pins but that only takes seconds and was more feasible than trying to make them spring-loaded ” Devine used a modified version of the male tabs and ears on a forklift attachment he fabricated It uses a 50-in wide steel plate with T-slot steel pilings at the top and bottom edge Forks are mounted to uprights with tabs that slide in and out of the T-slots The tab and ears are mounted on channel iron to the backside of the steel plate The channel iron raises them above the pilings “This design lets me carry double the amount I could with forks that attached to my bucket ” says Devine “I’ve picked up and moved trees and off-loaded logs for a neighbor’s log home ” He used the same raised concept for tabs and ears on a snow blade he fabricated for use with his loader “I used a larger piece of channel iron with it to compensate for the curvature of the blade ” says Devine “The quick attach system makes it easy to adapt any kind of loader attachment ” Contact: FARM SHOW Followup Robert Devine 4356 Boutell Ranch Rd West Branch Mich 48661 ph 307 670-0852
To read the rest of this story, download this issue below or click
here to register with your account number.