You have reached your limit of 3 free stories. A story preview is shown instead.
To view more stories
(If your subscription is current,
click here to Login or Register.)
He Brings Wooden Water Towers Back To Life
Paul Behrends repairs old wooden water tanks and also builds new ones. Behrends is a windmill repairman, and wooden water towers were once a common way to store water.
“We’ve worked on several old water-pumping windmills with tanks built into the tower,” explains Behrends.
Putting the tanks in t
..........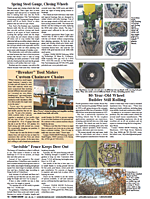
You must sign in, subscribe or renew to see the page.
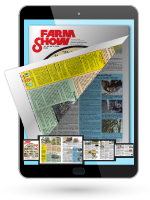
You must sign in, subscribe or renew to see the flip-book
He Brings Wooden Water Towers Back To Life FARM HOME Novelty Items Paul Behrends repairs old wooden water tanks and also builds new ones Behrends is a windmill repairman and wooden water towers were once a common way to store water “We’ve worked on several old water-pumping windmills with tanks built into the tower ” explains Behrends Putting the tanks in the tower assured water pressure for users These were often not small tanks notes Behrends “We overhauled a wooden tank in a steel tower that was built to hold 9 000 gal ” he recalls “The tower above the tank had a 14-ft diameter head on it A vertical sleeve in the tank held the pump rod as it went up and down to draw water ” The owner of that tank wanted it restored for appearance only not actual use Behrends and his employee rebuilt the catwalk and sprayed urethane on the roof to protect it from further rot Behrends was recently asked to build a new 3 000-gal wooden water tank for Ralph Gerbie on his LaPorte Ind farm The tank was built next to a 50-ft windmill with a 10-ft head over a new well Gerbie had planted a small orchard nearby “The idea was to use the well powered by the windmill to fill the tank and use the water to drip irrigate the orchard ” says Gerbie “We also wanted a design for the water tank with stairs to a platform with a railing where we could sit and watch the sunset ” Unlike others he had worked on this one would be built alongside the windmill and be supported by a wooden structure “Ralph wanted an overbuilt massive and heavy-duty look ” says Behrends Massive is what he got Behrends engineered the water tower around Gerbie’s concept It used 27 yards of concrete for a base Vertical posts were 8 by 8-in by 12-ft with 8 by 12-in primary beams some as long as 14 ft Joists were 6 by 12-in and as long as 14 ft to the tank deck “We used green white oak timbers which made working with them a challenge ” says Behrends “We cut the verticals to give them a 7 1/2-degree lean but we could only get about 3 cuts with a chainsaw before the chain got dull and started to veer off We used a lot of 40 grit sandpaper ” Behrends did all the cutting and trimming in his shop assembled 2 sides of the tower and hauled them in their vertical position to the site Once on site they were floated into position and the other sides pieced between them “They were anchored to the concrete at all 4 corners and the middle with 1-in bolts ” says Behrends “We used 3/8-in galvanized hot rolled steel plate fabricated in our shop to tie the joints together Timber tie bolts are galvanized 10-in long 1-in square head bolts Nothing is going to give ” The tank staves and bottom were made from Western red cedar Gerbie had shipped in from British Columbia It was stored in a barn on the property to acclimate to the local climate Once it was assembled Behrends also added decking and a railing around the tank “Once Paul put it all together the windmill fills the tank If we don’t shut it down overflow runs down a copper pipe and into a canal that connects several ponds on the farm ” says Gerbie “When we want to irrigate we open a valve on a second pipe ” Gerbie has since had a mural painted on the water tank It is similar to a larger mural he had painted on the end of his turn-of-the-century barn Contact: FARM SHOW Followup Paul’s Windmill & Crane Service 3413 County Road 625 E Foosland Ill 61845 ph 217 897-6699 or 217 369-4406; millfixr1@aol com; www paulswindmillservice com
To read the rest of this story, download this issue below or click
here to register with your account number.