You have reached your limit of 3 free stories. A story preview is shown instead.
To view more stories
(If your subscription is current,
click here to Login or Register.)
Fiber Mill Specializes In Alpaca Fiber
With the recent opening of a new fiber mill to process alpaca fleeces, alpaca producers may have a shorter wait time for roving or yarn from their animals. Plus, it’s a place to get quality advice from alpaca growers who understand fiber and color.
After waits of a year or more to get yarn from their alpaca fle
..........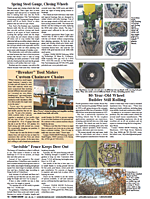
You must sign in, subscribe or renew to see the page.
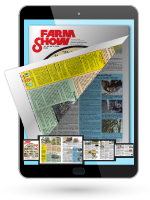
You must sign in, subscribe or renew to see the flip-book
Fiber Mill Specializes In Alpaca Fiber FARM HOME Clothes With the recent opening of a new fiber mill to process alpaca fleeces alpaca producers may have a shorter wait time for roving or yarn from their animals Plus it’s a place to get quality advice from alpaca growers who understand fiber and color After waits of a year or more to get yarn from their alpaca fleeces Mitchell and Linda Dickinson of Earleville Md decided to purchase equipment and go into business as Painted Sky Alpaca Farm & Fiber Mill It’s one of the only fiber mills anywhere that’s dedicated to processing alpaca and alpaca blends says Linda Alpaca is hypoallergenic and does not have the lanolin found in sheep fiber The need to remove oil and scrub equipment between processing sheep and alpaca is one reason why alpaca can take a long time to process at large mills At the farm’s mini-mill the Dickinsons and Linda’s sister Connie Hughes only process alpaca Plus with their understanding of fibers they offer customers advice on the best yarn types from each fleece “We are constantly learning because every fiber is different ” Dickinson says “There are certain formulas you follow but you have to adjust Some customers may want bulky yarn but the fiber doesn’t want to be bulky So we call them and make suggestions ” A key ingredient to making quality yarn is clean fiber Alpaca owners need to skirt their fleeces remove vegetation and fiber shorts prior to sending them to the mill “We look at the quality of the fiber staple length crimp structure and cleanliness to ensure the fleece will make a nice quality yarn in the desired weight ” Dickinson says Each fleece is tumbled to remove any remaining dirt vegetable matter and fiber shorts then washed in 150-degree water After drying the fleece is run through a picker “It breaks open clumps of fiber and shoots them into a closet so when you open the door it looks like a huge ‘cloud’ of fiber ” Dickinson explains “Then it goes into a fiber separator It’s important to have that with alpaca because it pulls out thicker guard hairs and only finer fibers pass through to the end ” The thicker hairs are run through one more time to salvage more of the fiber Even the coarsest fiber is saved and used to make rug yarn The good fiber goes into a carder to produce a thin strand of roving For customers who want yarn the journey continues through a draw frame then a spinner where a single strand is spun on a spindle The individual strands are then run through a plyer to create two or three ply yarn It is finished with steam to set the twist “About 75 percent of our orders are made into yarn 15 percent roving and 10 percent rug yarn ” Dickinson says As a retired graphic artist Dickinson enjoys the creative process of adding color creating natural blends or suggesting other fiber blends for her customers Some alpaca fleeces need help to become a quality yarn For instance Suri Alpacas have no crimp which gives elasticity to the yarn so it is recommended to blend it with high-grade Merino wool or a Huacaya fleece Demand is growing as people discover the mini mill Dickinson says “Our current turn around time for orders is 4 to 5 months ” Dickinson says Contact: FARM SHOW Followup Painted Sky Alpaca Farm & Fiber Mill 95 Knight House Lane Earleville Md 21919 ph 410 275-9423; www paintedskyfibermill com; paintedskfibermill@gmail com
To read the rest of this story, download this issue below or click
here to register with your account number.