You have reached your limit of 3 free stories. A story preview is shown instead.
To view more stories
(If your subscription is current,
click here to Login or Register.)
They Transform Wheeled Equipment To Tracked
Right Track Systems can help you turn any off-road wheeled system into a tracked one. The company offers customized tracks for wheeled equipment up to 6 ft. in width, such as duals on the largest tractors. They also offer replacement tracks for OEM tracked equipment. Applications include trucks and trailers, skid steer
..........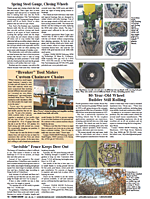
You must sign in, subscribe or renew to see the page.
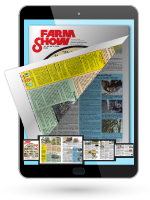
You must sign in, subscribe or renew to see the flip-book
They Transform Wheeled Equipment To Tracked TIRES/WHEELS Handling Right Track Systems can help you turn any off-road wheeled system into a tracked one The company offers customized tracks for wheeled equipment up to 6 ft in width such as duals on the largest tractors They also offer replacement tracks for OEM tracked equipment Applications include trucks and trailers skid steers Snowcats agricultural equipment and even telehandlers and aerial lifts Tracks are also available for ATV’s Argos and even custom-designed equipment “We started with track systems for skid steers and have expanded from there ” says Tom Zaleski Jr Right Track Systems Inc “Over the past decade we’ve added tracks for almost every type of off-road equipment ” The biggest question when adding tracks is clearance Is there room between the tire and the fender or wheel well? Zaleski explains that a standard track adds about 4 in to the radius of a tire and about 3 in to the width An extra inch beyond that is needed “We do offer solutions for tight spots such as recommending a smaller diameter tire or modifications to the machine ” says Zaleski “Some customers have moved fenders or even a gas tank or step A spacer can also be added between the hub and the wheel to move the hub farther from the vehicle ” One attraction of the Right Track system is customization Selecting the right track requires knowing the width of the tire tread width of the tire from sidewall to sidewall circumference of the tire and the axle spacing center to center In the case of duals the overall width of tread including space between the tires and the space between the tires is also needed Once the appropriate length and type of track is stretched out on the ground the equipment is driven on Zaleski recommends attaching a length of chain around the ends of the track and using a come-along to pull them together for linking Simply reverse the process to remove the tracks or even easier let air out of the tires and release the end links “It is a very simple process ” says Zaleski “The track ends come together like a tandem hitch Once you’ve done it a few times it takes between 30 and 40 min to mount tracks and just a few minutes to remove them ” The tracks themselves can be modified for the type of surface to be traveled Hard surfaces call for lower profile grousers treads and less gap between them Urethane grousers can be slippery on ice and snow so Zaleski recommends adding an ice cleat to the grouser for the winter and removing it for the summer Grousers are available in a variety of types patterns and depths In addition to low-impact 1-in polyurethane they are also available in aggressive 2 5-in UHMW poly grousers Grousers can be interchanged for different seasons and ground conditions or quickly replaced if damaged or worn The UHMW poly wear bars on the inside of the track add tire grip The 1-in height of the wear bars also keeps the tires away from the belting and keeps the inside free of mud Mild steel saddles guide the tracks over the wheels In the case of duals a ridge in the middle of the saddles keeps the belt centered Grousers are mounted to heavy-duty conveyor belting that has 5 times the strength of standard ag tires The 1 200-lb 4-ply belting originated in the mining industry This ensures virtually no tire damage One set of tracks can even be designed for use with a second piece of equipment with the same size tires but different axle spacing A spacer section of track is used to lengthen the track at the splice points Right Track Systems are available direct from the company as well as from several distributors such as Nesco in the utility market Prices vary by type and size Tracks for a skid steer with 10-16 5 tires run from $4 000 to $4 500 Contact: FARM SHOW Followup Right Track Systems Int 16734 – 110 Ave Edmonton Alta T5P 1G9 Canada ph 855 481-9473; info@righttracksystemsinc com; righttracksystemsinc com
To read the rest of this story, download this issue below or click
here to register with your account number.