You have reached your limit of 3 free stories. A story preview is shown instead.
To view more stories
To view more stories
SUBSCRIBE OR RENEW NOW
(If your subscription is current, click here to Login or Register.)2017 - Volume #41, Issue #4, Page #17
[ Sample Stories From This Issue | List of All Stories In This Issue]
Built-From-Scratch Loader Tractor, Backhoe
When long-time reader Brian Laine took the time to tell us about a guy who built a tractor loader with a backhoe – all from scratch – we figured it must be good because Laine is a pretty innovative guy himself (Remote-Controlled Tractor, Vol. 40, No. 3). So we chased down the tractor builder. “I started out..........
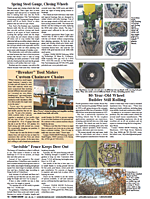
You must sign in, subscribe or renew to see the page.
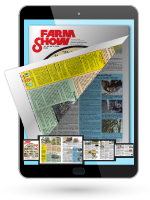
You must sign in, subscribe or renew to see the flip-book
Built-From-Scratch Loader Tractor Backhoe TRACTORS Loaders When long-time reader Brian Laine took the time to tell us about a guy who built a tractor loader with a backhoe – all from scratch – we figured it must be good because Laine is a pretty innovative guy himself Remote-Controlled Tractor Vol 40 No 3 So we chased down the tractor builder “I started out building a loader for my garden tractor only to discover the garden tractor had been misrepresented to me when I bought it It didn’t have enough power ” says Don Forgash of Tehachapi Calif Even though the garden tractor was the first tractor he’d ever owned he decided to build a bigger tractor so he could use his new loader Fortunately he had a pile of 3-in sq stainless steel tubing to get him started After about 4 mos he had a new tractor that was roughly 7 ft long and about 4 1/2 ft wide He powered it with a 13 hp Harbor Freight engine fitted with a White hydraulic pump from an old lawn tractor The drive consisted of transaxles with 1-in axles and Peerless transmissions with 4 forward gears The hydraulics powered a motor with 2 belts one to the rear axle and one to the front for 4-WD “I fabricated the front steering knuckles to work with CV driveshafts to drive the front wheels ” says Don “The biggest challenge was getting the ratios right between the variable speed White pump and the transaxles I ended up going with a high torque low rpm motor ” Don even used stainless steel for the hood and tanks Once he had the small tractor and loader built Don started thinking about adding a backhoe But he realized the size backhoe he wanted would be too heavy for the tractor “That’s when I decided to build an even heavier-duty tractor out of automotive grade parts ” explains Don Knowing he would also need a larger loader for the new tractor Don started looking around settling on the design of a Deere 300 “I liked the curves of the loader but also the hood and fenders as well as the color ” he recalls “I borrowed some features and ended up building a loader with a little bit of Deere and a little bit of Don ” A Ford Mustang 8 8 rear end was his starting point He ordered skid steer wheels and tires for it as he wanted the extra thick sidewalls Instead of stainless steel he went with 2 by 6-in 3/32-in steel tubing for the frame He used a solid 2-in bar across the frame to reinforce loader mounting points The front axle was fabricated from 3/8-in 4 by 4-in square steel tubing to carry the weight of a full loader bucket He used a 1 1/4-in pin for the center pivot He went with rack and pinion steering after chopping out a few inches and welding it back together He modified the front spindles and added disc brakes “I also shortened the rear axles and made them into full floating axles so they turn the wheels while the weight is supported by a wheel bearing hub ” Don made mounts for the hubs to hold disc brake calipers instead of a drum brake The hub also holds the axle seal Since he had the rear end torn down he changed the gear ratio and rebuilt the positraction disc “I had an old Datsun pickup truck motor that I rebuilt with new pistons bearings oil pump valves and spring ” says Don “I mounted it backward in the tractor as I intended to power the hydraulic pump off the engine’s front pulley ” To drive the rear axle Don attached a disc brake to the differential connecting it to a disc brake attached to a hydraulic wheel motor A third disc brake was run backwards toward the engine to act as a parking brake Things began to get complicated when he discovered the crankshaft pulley was cracked Unable to locate a replacement pulley he decided to fabricate a pto shaft to transfer power to the pump He opted to replace the power steering pump with electric steering reducing engine load and freeing up space in the engine compartment “I found out about Toyota’s electric steering and got hold of a used steering column ” says Don “A YouTube video gave me enough to get started ” He had to shortcut control components to bypass the need for computer inputs He also had to fabricate brackets for mounting it Don also upgraded the alternator to a chrome Delco 105 amp To get the curved fender and hood look he wanted when bending sheet metal Don made an “English wheel” with a cast iron wheel and a caster off an engine stand mounted to 2 by 2-in 1/4-in tubing When building the loader cutting out and assembling the arms was the easy part Bending a 5 by 6-ft sheet of steel for the bucket was more complicated Don started by making a frame with 2 by 2-in 1/4-in tubing and a 5-ft long 1/2 by 6-in flat bar of steel attached to an air-over-hydraulic jack Once he had the bends in place he wrapped it with 1/4 by 6-in steel straps and added 2 hooks for chains and brackets for the loader arms “I added armor to the sides and a piece of 5/8 by 6-in plow bar steel for the edge and topped it off with 7 caterpillar style teeth ” says Don “I added similar teeth to the backhoe bucket ” For complete details on Don’s projects he suggests visiting www mytractorforum com where he has posted many photos and descriptions of the work Just search for him under the user name “Donewrken ” “The encouragement was really important ” says Don “I had over half a million hits on Part One alone with people following the build from Portugal to South America as well as from North America and elsewhere ”
To read the rest of this story, download this issue below or click here to register with your account number.