You have reached your limit of 3 free stories. A story preview is shown instead.
To view more stories
(If your subscription is current,
click here to Login or Register.)
Good Press Makes Great Cider
Leonard Good’s shop-built press makes such great cider that he doesn’t even need his own apples. People give him a quarter share of their cider just for the use of his press.
“One man brought a pickup load of apples 2 days in a row, and we made 300 gal. of cider,” recalls Good. “With the help of a couple of tee
..........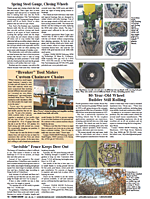
You must sign in, subscribe or renew to see the page.
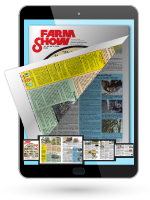
You must sign in, subscribe or renew to see the flip-book
Good Press Makes Great Cider FARM HOME Food Leonard Good’s shop-built press makes such great cider that he doesn’t even need his own apples People give him a quarter share of their cider just for the use of his press “One man brought a pickup load of apples 2 days in a row and we made 300 gal of cider ” recalls Good “With the help of a couple of teenagers we can make about 15 gal of cider an hour ” There is no telling how many gallons of cider Good has made since he first built the press in 1974 “The baskets that catch the pulp and hold it for pressing are original as is the crusher ” says Good “I did have to rebuild the press disc I started with 2 plywood layers each 1/2 in thick and it lasted a year Then I used 3 pieces and it lasted 3 years I went to 4 pieces and it has lasted ever since ” Good didn’t have any plans to work from beyond a book on crushing grapes for wine “I used all salvaged parts other than about $5 worth of screws ” says Good He designed a frame 28 by 29 in in size with a height of about 30 in It has an apple hopper to the left and a press on the right A slanted tray with 2-in rails mounted about 10 to 12 in off the ground holds the pulp baskets It has room for one being filled and a second one being pressed A pipe in the lower end drains pressed cider into containers “I have 2 sieves that fit on top of gallon milk jugs to filter out the pulp ” says Good To pulp the apples Good decided to use a wooden shaft studded with screws As the apples fall to the bottom of the hopper the screw heads tear them apart He had a motor complete with a driveshaft and sheave salvaged from an old clothes dryer for power For the press itself Good used a 1 1/2-in dia 2 1/2-ft long threaded rod with a plate at one end Good mounted it through a threaded crosspiece that seats in a recess in the underside of the upper crosspiece in the frame The 4-layer plywood press disk attaches to the bottom end To fabricate the pulp baskets Good calculated the diameter needed to match the press plate He started with steel bands for hoops and 3/4-in square mahogany and fir strips “I didn’t need bottoms as the baskets filled with pulp just slide back and forth on the shelf ” Good indicates he would be willing to draw up more detailed plans should a FARM SHOW reader want to build his own press Contact: FARM SHOW Followup Leonard Good P O Box 131 Langley Wash 98260 ph 360 221-6439
To read the rest of this story, download this issue below or click
here to register with your account number.