How They Started Their On-Farm Pelleting Business
Charlie and Christine Forman operate 2,000 acres of cropland and several service businesses that keep them and their employees hopping around the clock. In addition to growing crops, they install drain tile, dig ditches, operate a greenhouse, produce vegetables for a farmer’s market, sell bedding plants and perennials, produce custom flower containers, and deliver grain. Over the past couple years, they’ve also worked hard to develop an on-farm pelleting operation called SwitchGreen.
Charlie Forman says their initial plan was to pelletize switchgrass because the perenial crop is fairly easy to grow and is ideal for the growing conditions in eastern Ontario. They purchase harvested bales and turn the crop into biomass fuel pellets and other products. Pellets are “made to order” with recipes they’ve developed that use switchgrass, waste wood and other agricultural biomass, including crop residue. Pellets can be used for residential, commercial or industrial heating.
They’ve had some success, such as a contract to provide more than 150 tons of pellets to heat a local school, but profitability has been challenging.
To start out, Forman purchased a pelleting mill in 2011 from Torrified Wood Pellet Equipment in New Brunswick, Canada, for $350,000. Intially, they had to make a lot of modifications to the machine to get it to work the way they wanted.
“The conveyors and paddles would freeze up and the paddles were not heavy enough. The auger that supplies material to the dies had to be replaced with one of our own design so we could use steam to preheat the crop material. Sensors were installed to control the flow of material yet allow the dies and hammermill to run continuously. The two dies run against each other with 3,000th of an inch clearance and were extremely difficult to reset, so we redesigned them with a cam that can be adjusted with a large ratchet. In addition, the dies have thermal elements imbedded into the wall of the plate that the dies are fastened to. We doubled the wattage and saw a significant increase in production but, more importantly, saw fewer problems with variability in moisture content of incoming product to the dies.”
They made many other adjustments to guides and shields and even the electrical box. After modifying the machine, they’ve been able to produce about 800 lbs. of pellets per hour. They’re just now getting to a point where they’re able to get a handle on production costs, which include:
Collection of raw product.
Pre-grinding
Loading product into feed bin
Pellet production
Filling totes or bagging
Pickup or delivery of pellets
Maintenance and setup of machine
Electric costs of operation
Storage.
“The price of pellets is pretty much set by the marketplace unless you have a product with special attributes so we have to know what our costs are,” notes Froman.
In addition to all of the above, Froman notes that it takes 3 years to establish a crop of switchgrass and during that time, there’s no income. Once established, one crop can be harvested each year.
Maybe the biggest challenge to making pellets, says Froman, is getting the right recipe so the material actually pelletizes and doesn’t break down. They use vegetable oil, moisture and other ingredients that he won’t divulge because it took so much work to figure them out. He does note that switchgrass can’t be successfully pelleted by itself without added ingredients.
In addition to producing pellets for fuel, Froman makes pelletized deer feed that includes corn, roasted soybeans, alfalfa hay, and dried molasses.
Contact: FARM SHOW Followup, Forman Farms, 3936 Pine Grove Rd., Seeley’s Bay, Ontario Canada K0H 2N0 (ph 613 382-4949).
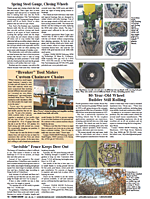
Click here to download page story appeared in.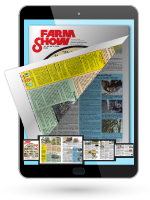
Click here to read entire issue
How They Started Their On-Farm Pelleting Business CROPS Miscellaneous Charlie and Christine Forman operate 2 000 acres of cropland and several service businesses that keep them and their employees hopping around the clock In addition to growing crops they install drain tile dig ditches operate a greenhouse produce vegetables for a farmer’s market sell bedding plants and perennials produce custom flower containers and deliver grain Over the past couple years they’ve also worked hard to develop an on-farm pelleting operation called SwitchGreen Charlie Forman says their initial plan was to pelletize switchgrass because the perenial crop is fairly easy to grow and is ideal for the growing conditions in eastern Ontario They purchase harvested bales and turn the crop into biomass fuel pellets and other products Pellets are “made to order” with recipes they’ve developed that use switchgrass waste wood and other agricultural biomass including crop residue Pellets can be used for residential commercial or industrial heating They’ve had some success such as a contract to provide more than 150 tons of pellets to heat a local school but profitability has been challenging To start out Forman purchased a pelleting mill in 2011 from Torrified Wood Pellet Equipment in New Brunswick Canada for $350 000 Intially they had to make a lot of modifications to the machine to get it to work the way they wanted “The conveyors and paddles would freeze up and the paddles were not heavy enough The auger that supplies material to the dies had to be replaced with one of our own design so we could use steam to preheat the crop material Sensors were installed to control the flow of material yet allow the dies and hammermill to run continuously The two dies run against each other with 3 000th of an inch clearance and were extremely difficult to reset so we redesigned them with a cam that can be adjusted with a large ratchet In addition the dies have thermal elements imbedded into the wall of the plate that the dies are fastened to We doubled the wattage and saw a significant increase in production but more importantly saw fewer problems with variability in moisture content of incoming product to the dies ” They made many other adjustments to guides and shields and even the electrical box After modifying the machine they’ve been able to produce about 800 lbs of pellets per hour They’re just now getting to a point where they’re able to get a handle on production costs which include: Collection of raw product Pre-grinding Loading product into feed bin Pellet production Filling totes or bagging Pickup or delivery of pellets Maintenance and setup of machine Electric costs of operation Storage “The price of pellets is pretty much set by the marketplace unless you have a product with special attributes so we have to know what our costs are ” notes Froman In addition to all of the above Froman notes that it takes 3 years to establish a crop of switchgrass and during that time there’s no income Once established one crop can be harvested each year Maybe the biggest challenge to making pellets says Froman is getting the right recipe so the material actually pelletizes and doesn’t break down They use vegetable oil moisture and other ingredients that he won’t divulge because it took so much work to figure them out He does note that switchgrass can’t be successfully pelleted by itself without added ingredients In addition to producing pellets for fuel Froman makes pelletized deer feed that includes corn roasted soybeans alfalfa hay and dried molasses Contact: FARM SHOW Followup Forman Farms 3936 Pine Grove Rd Seeley’s Bay Ontario Canada K0H 2N0 ph 613 382-4949
To read the rest of this story, download this issue below or click
here to register with your account number.