You have reached your limit of 3 free stories. A story preview is shown instead.
To view more stories
(If your subscription is current,
click here to Login or Register.)
Giant Press Has Rolling Cylinders
Clair Wilson makes pressing big steel pieces look easy with his double carriage, dual cylinder with independent action, chest-high press. Overbuilt doesn’t begin to describe the “ship-channel” construction of the press at his Wilson Seedtime and Harvest shop.
“A friend of mine had a machine shipped in fro
..........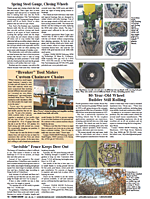
You must sign in, subscribe or renew to see the page.
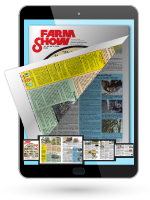
You must sign in, subscribe or renew to see the flip-book
Giant Press Has Rolling Cylinders FARM SHOP Miscellaneous Clair Wilson makes pressing big steel pieces look easy with his double carriage dual cylinder with independent action chest-high press Overbuilt doesn’t begin to describe the “ship-channel” construction of the press at his Wilson Seedtime and Harvest shop “A friend of mine had a machine shipped in from England on pieces of 15-in channel iron with a 5/8-in web called ship channel ” says Wilson “I used it for the top of the press and the table frame The web isn’t tapered like other channel iron making it ideal for mounting carriages for the cylinders ” The legs of the press are also substantial Wilson salvaged the 6-in channel iron with its 5/8-in web from rafters in a state hospital that a friend was tearing down The 40-in wide by 56-in long table was salvaged from a commercial milling machine The top level of the table is 3 in of steel with 8 slots running its length A second 3-in steel layer is bolted beneath “The slots are ideal for hold-down dogs ” says Wilson “With their bolt-on heads I can slide them into position and tighten down on the work piece ” He didn’t salvage the hydraulic cylinders Those he bought new before cutting off their brackets The base of each 4-in cylinder with its 2-in ram and 18-in reach is welded to a flat steel plate The plate sits on the bottom flanges of a carriage with wheels The wheels allow it to roll back and forth within a second larger carriage also with wheels The larger carriage rides on the lower flange of the ship channel at the top of the press “I can move a ram anywhere on the table with one carriage moving one way and the other carriage moving the other way ” says Wilson “With independent hydraulic pressure on each cylinder I can put more or less pressure on either one ” When the ram is extended the cylinder plate lifts off the bottom flange of the carriage to press against the top flange of the inner carriage It in turn pushes against the top flange of the larger carriage eventually pushing it against the top flange of the ship channel “It is great for taking bends out of a piece of steel ” says Wilson “I took a snout from an older corn picker that was all doubled over You couldn’t beat the bends out but I could push down on one corner and pry with the other cylinder and push bends out ” As heavy-duty and versatile as the press is it is also handy for Wilson to operate Rollers allow him to move it as needed and visibility is excellent “I built it chest high so I don’t have to lean in to see ” says Wilson Contact: FARM SHOW Followup Wilson Seedtime and Harvest
129 Hillview Rd
Winchester Ill 62694 ph 217 742-3918; contact@wilsonharvest com; www wilsonharvest com
To read the rest of this story, download this issue below or click
here to register with your account number.