You have reached your limit of 3 free stories. A story preview is shown instead.
To view more stories
(If your subscription is current,
click here to Login or Register.)
He “Turns” Big Logs Into Magnificent Art"
I guess it all began when I saw the incredible log lodges in Yellowstone Park when I was 8 years old,” says Virgil Leih, a log-sculpting artist from Minnesota. “I eventually spent 10 years building my own log home near Ely, Minnesota. And then at some point, I began to have a vision of transforming giant tree trunks in
..........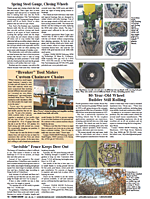
You must sign in, subscribe or renew to see the page.
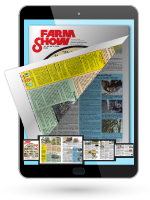
You must sign in, subscribe or renew to see the flip-book
He “Turns” Big Logs Into Magnificent Art FARM HOME Miscellaneous I guess it all began when I saw the incredible log lodges in Yellowstone Park when I was 8 years old ” says Virgil Leih a log-sculpting artist from Minnesota “I eventually spent 10 years building my own log home near Ely Minnesota And then at some point I began to have a vision of transforming giant tree trunks into large-scale sculptures ”
That’s how Leih explains his evolving wood-sculpting hobby that for the past 10 years has produced rare and unique giant urns vases and spheres that sell for $5 000 or more in galleries and on consignment
Leih’s tree art always begins with selecting a promising log from a landfill or a “tree-trunk dump” Leih may start with a 4 000-lb log and end up with an 8-ft tall urn after 95 percent of the log has been turned into wood shavings
Initially Leih guessed his biggest challenge would be finding a lathe and other equipment to work the logs He solved that problem when he bought an 8 000-lb Oliver pattern-maker’s lathe built in 1917 that could handle up to a 17- ft log
The greater challenge Leih discovered was learning to dry logs so they wouldn’t split and crack when they’re being worked on or after they’re completed “Nothing is more frustrating than creating a magnificant vessel and then having it crack because the wood wasn’t sufficiently dry ” Leih says
Leih struggled with the drying dilemma for years eventually devising a 38-in heated vacuum chamber that he fabricated using a giant sewer pipe with 2-in thick walls The heated vacuum chamber slowly extracts a log’s moisture over several weeks
Lathe woodworkers are used to working a piece of wood using a gouge as the wood turns towards them Leih reverses that procedure so he works wood as his giant lathe turns a log away from him He uses tools that he’s devised including a mounted chainsaw or a right-angle grinder to do the dangerous wood removal until he achieves a perfectly balanced round log
Leih’s fanciest urns may require 100 hrs or more to hollow and sand Then he follows with up to 10 coats of shellac interspersed with more sanding and buffing between coats “So the vessel becomes everlasting and virtually immune to discoloration”
Leih refers to himself as a “grain chaser” someone who’s constantly pursuing the often-awesome wood grain revealed in each new log He says “that’s what wood has to offer – beautiful tremendous wood grain I always feel like it’s a spiritual thing opening up a log for the first time It’s never had human eyes on it before ”
Go to www farmshow com to see a video of Leih’s process
Contact: FARM SHOW Followup Virgil Leih ph 612 308-4992; www virgiltreeart com
To read the rest of this story, download this issue below or click
here to register with your account number.