You have reached your limit of 3 free stories. A story preview is shown instead.
To view more stories
(If your subscription is current,
click here to Login or Register.)
Rural Craftsman Makes Amazingly Detailed Clocks
About 50 years ago Lars Romo’s parents took him to the Bily Clock Museum in Spillville, Iowa, to view the amazingly detailed clocks made famous by the Bily brothers. “I was impressed by the intricate detail and told my parents that someday I wanted to build clocks just like those,” Romo says. A half century later, Rom
..........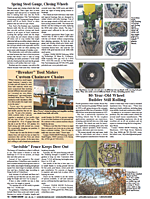
You must sign in, subscribe or renew to see the page.
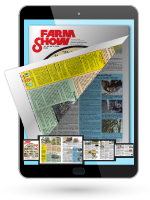
You must sign in, subscribe or renew to see the flip-book
Rural Craftsman Makes Amazingly Detailed Clocks FARM HOME Miscellaneous About 50 years ago Lars Romo’s parents took him to the Bily Clock Museum in Spillville Iowa to view the amazingly detailed clocks made famous by the Bily brothers “I was impressed by the intricate detail and told my parents that someday I wanted to build clocks just like those ” Romo says A half century later Romo has realized his wish by hand-crafting 16 intricate Bily clocks an Italian chandelier and numerous other elaborate woodworking projects Unlike most craftsmen who purchase wood for their projects Romo cuts his own lumber “I saw my own logs with a Woodmizer so I can examine the grain control the board thickness and manage the curing process ” Romo says Twenty years ago a woodworking neighbor showed him how to prevent warping and cracking by dipping boards in a mixture of anti-freeze and water before curing “I’ve never had a board crack or warp when I do that ” Romo says For his clock-making Romo uses only quarter-sawed black cherry Boards are first cut 1/2 in thick then to 3/8 in 1/4 in and even 1/8 in for the smallest pieces He traces complex scroll patterns on boards that range from just a few inches long up to about 18 in Some pieces have multiple angles that require miniature compound cuts where there’s really no room for error His replica Amiens Tower and Apostle clocks each have about 600 pieces that required several thousand cuts That time consuming task included drilling about 4 000 1/16-in holes inserting the scroll saw blade in each one then making the minute radius cuts Each clock takes about a year to complete “Sometimes I’ll drill 80 to 90 holes in a 2 by 6-in piece and more than 200 holes in a 6 by 18-in piece ” Romo says One of his favorite projects was the Apostle clock which has several 6-sided towers ranging from 1 to 4 in tall Each tower has six individual pieces that fit perfectly together in the round base and angle up to join in a pointed steeple The 3-ft tall clock is configured around a 12-in wide altar that Romo built from a sketch he made based on the altar at Urland Church near his farm Romo has built 16 complex clocks in 20 years of woodworking and worn out three different scroll saws in the process “Originally I was going to build a clock for each of my four kids and then quit ” Romo says “then I came up with an idea to reduce the amount of ‘designer firewood’ I was generating ” Romo modified his saw to accept a dremel tool that prevents the blade from chattering or deflecting to the side and ruining a complex pattern With that improvement he was able to cut more efficiently with less waste so he kept on building Romo’s clocks line the living room walls of his farmhouse and he doesn’t intend to sell them He’s happy to show them to visitors and has entered a few in woodworking contests He won $600 in a contest sponsored by Woodmizer the company that built his sawmill A few years later he entered his Normandy clock and won $1 000 A Wisconsin collector offered him $4 000 for the Normandy but Romo turned him down “That one is special and it’s going to one of my kids someday ” he says Contact: FARM SHOW Followup Lars Romo 40225 90th Ave Cannon Falls Minn 55009 ph 507 824-2297
To read the rest of this story, download this issue below or click
here to register with your account number.