You have reached your limit of 3 free stories. A story preview is shown instead.
To view more stories
(If your subscription is current,
click here to Login or Register.)
“Do It Yourself” Concrete Blocks
Stumbelbloc heavy-duty plastic molds make it easy to make your own concrete blocks, and the design makes stacking the blocks easy as well. Tabs on the blocks self align and lock in place with no need for mortar. A. Marcelino and Co. is distributing the block casting system, which was developed in South Africa.
..........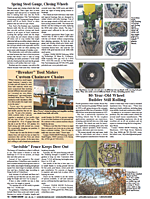
You must sign in, subscribe or renew to see the page.
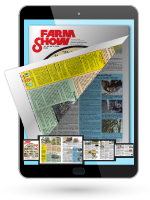
You must sign in, subscribe or renew to see the flip-book
“Do It Yourself” Concrete Blocks BUILDINGS Miscellaneous Stumbelbloc heavy-duty plastic molds make it easy to make your own concrete blocks and the design makes stacking the blocks easy as well Tabs on the blocks self align and lock in place with no need for mortar A Marcelino and Co is distributing the block casting system which was developed in South Africa “We use Block Bond designed for dry stacking cinder blocks ” says Alan Marcelino “We dip the blocks in it and it hardens on the outside like a structural skin When set up they are as solid as can be ” Marcelino a concrete and asphalt recycler crushes concrete and turns it back into redi-mix concrete used for precast concrete products Initially he began recycling styrofoam too He would break it up into BB-sized pieces and mix it with Portland cement and crushed concrete for its thermal insulation properties The Stumbelbloc casting system gave him the option of making blocks with the styrofoam mix and later filling them with the same mix While he couldn’t use them as a load-bearing wall they could add 8-in of insulation to the inside of a metal building “We live in New England and operating out of a metal prefabricated building can be a challenge ” he says “Two years ago we lined one wall of our workshop with styrofoam blocks and filled them with styrofoam concrete ” says Marcelino “That end of the building was noticeably warmer This year we are lining the rest of the shop ” Making the blocks is simple After oiling the surface the two halves of the mold lock together with wing nuts leaving one end open The concrete mix is poured in Tapping the sides with a mallet or setting the mold on a vibrating table settles the concrete into place Once the block has set for 24 to 48 hours it can be removed from the mold and set aside to cure Although the method is labor intensive Marcelino believes it has potential for use in remote locations where it is easier to bring in bags of concrete mix than pallets of blocks It also works well with customized mixes such as his styrofoam concrete Marcelino is pricing the molds at $50 each Half block molds are $25 each with price breaks for larger quantities Instructions and some plans included He says he can do about 50 blocks at a time with a 1-yard mixer “We don’t have a large inventory yet so it may take a month to fill an order ” advises Marcelino “These are not likely to be cost effective as a way to manufacture blocks but they will work great for the DIY market The molds are heavy duty and don’t wear out ” Contact: FARM SHOW Followup A Marcelino & Co 4050 Williston Rd South Burlington Vt 05403 ph 802 862-6383; starpaver1@aol com
To read the rest of this story, download this issue below or click
here to register with your account number.