You have reached your limit of 3 free stories. A story preview is shown instead.
To view more stories
(If your subscription is current,
click here to Login or Register.)
How To Build A Big Wooden Ball
“I was inspired to build this big wooden ball after reading an article in FARM SHOW about ‘art’ made from pallets (Vol. 37, No. 3). The article showed a big wooden ball that I thought was interesting,” says Jody Taylor, Hammond, La.
“I had thought about constructing a big wooden ball like that for a long time,
..........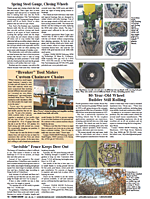
You must sign in, subscribe or renew to see the page.
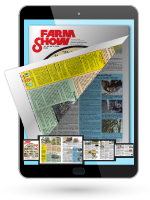
You must sign in, subscribe or renew to see the flip-book
How To Build A Big Wooden Ball FARM HOME Novelty Items “I was inspired to build this big wooden ball after reading an article in FARM SHOW about ‘art’ made from pallets Vol 37 No 3 The article showed a big wooden ball that I thought was interesting ” says Jody Taylor Hammond La “I had thought about constructing a big wooden ball like that for a long time but I could never figure out how to do it I decided to try anyway and it wasn’t until I finished the job 3 months later that I knew it could be done ” He built the ball on a metal pipe that’s mounted horizontally so he could spin the ball around as he built it To keep the ball balanced so it would spin on the shaft he would build one side and then the other side “It’s almost impossible to build a wooden ball on a shop floor or a table because you need to be able to move the ball around ” says Taylor He says he’s proud of the methods he came up with to construct the ball “I could fill all the pages of an entire FARM SHOW issue trying to explain how I did it ” The ball measures 64-in dia and weighs about 1 500 lbs It’s made entirely of treated pine and 3/4-in thick plywood “There’s an attraction to these big wooden balls that you wouldn’t believe Everyone who sees it for the first time can’t believe what they’re looking at I don’t suppose that it has any practical use other than for yard art and for the exercise I get rolling it around my 12-acre property Lucky for me my land is flat because there are no brakes installed on my big wooden ball ” The 7-ft long 2-in dia pipe is mounted on top of a big triangle-shaped metal frame that Taylor already had “I own a business making life jackets and use the frame to mount rolls of foam rubber which are then pulled through a press that stamps out various life jacket pieces The frame happened to be just the right tool to use ” says Taylor The ball is built from 8 treated pine panels shaped like a semi circle The panels radiate out from an 8-sided hollow center core that slides over the pipe Both the panels and the center core are made from 2 by 4’s A mid support structure at the center that’s made from 4 by 6’s connects all the panels together Layers of 3/4-in thick plywood are attached to the panels and support strips of curved 1 by 2’s Taylor used a 4-ft section of a 5-ft dia metal culvert to bend the 1 by 2 strips first heating the wood and then using a pair of come-alongs inside the culvert to bend the strips “I first stuck the strips in a pipe that I welded to one side of the culvert with the strips sticking straight up in the air Then I heated the strips and attached the come-alongs I also kept the strips wet as I bent them ” says Taylor “I used our well water which has rust in it that gave a brownish color to many of the boards and added to the ball’s character ” When he was done building the ball he pulled the frame with the ball still on it out through his workshop doors and it barely fit He used a forklift to lift the ball off the stand and then set it down on the ground pulled the pipe out and put caps on both ends “The hardest part was curving the 1 by 2-in wood strips I bent the strips in batches and I had to do 3 separate bendings to make enough strips to cover the ball It took about one month to do each batch The strips were under tremendous pressure pulling them around the culvert and because I was using treated pine wood a lot of the wood snapped at the knots Next time I’d do the bending work during the summer because the warmer weather might allow the wood to bend easier without snapping “My total expense was less than $2 000 That included not only the wood but also a lot of screws and a case of liquid nail glue “It was the smallest big ball that I could make because it’s very difficult to get wood to bend to a smaller circumference A bigger ball would actually be easier to build ” notes Taylor Contact: FARM SHOW Followup Jody Taylor 16150 E Club Deluxe Rd Hammond La 70403 ph 985 969-1057; sales@taylortec com
To read the rest of this story, download this issue below or click
here to register with your account number.