You have reached your limit of 3 free stories. A story preview is shown instead.
To view more stories
To view more stories
SUBSCRIBE OR RENEW NOW
(If your subscription is current, click here to Login or Register.)2015 - Volume #BFS, Issue #15, Page #42
[ Sample Stories From This Issue | List of All Stories In This Issue]
Solar Furnace Heats Greenhouse Soil
Richard Staus has extended his growing season by 6 weeks, thanks to his solar powered furnace (SPF). Twin 4 by 10-ft. solar thermal collectors help to heat his 30 by 72-ft. FarmTek high tunnel. Hot air is piped through an insulated sand base under the greenhouse. The closed loop system keeps the soil and the greenhouse..........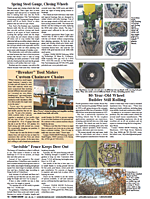
You must sign in, subscribe or renew to see the page.
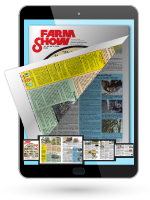
You must sign in, subscribe or renew to see the flip-book
Solar Furnace Heats Greenhouse Soil BUILDINGS New Techniques Richard Staus has extended his growing season by 6 weeks thanks to his solar powered furnace SPF Twin 4 by 10-ft solar thermal collectors help to heat his 30 by 72-ft FarmTek high tunnel Hot air is piped through an insulated sand base under the greenhouse The closed loop system keeps the soil and the greenhouse warm into the fall and warms it earlier in the spring “In 2012 we picked our last fresh strawberries November 25th ” says Staus “We had tomatoes that were 8 to 9 ft tall and grew lettuce and spinach all through the winter with the help of low tunnels at night We would take the plastic off each morning ” Staus has a supplemental furnace but rarely needs it Most of the year his SPF designed and built by Rural Renewable Energy Alliance RREAL is more than enough RREAL makes 3 SPF models – 4 by 6 1/2 ft 4 by 8 ft and 4 by 10 ft – ranging in price from $1 050 to $1 500 “We have a proprietary design that lets you set up an array of SPF units in parallel which reduces fan needs and doesn’t require an external manifold ” says Jason Edens RREAL “A lot of collectors have pre-sized fan systems but we design the air system based on 2 to 4 cu ft per min per sq ft of collector surface ” In the case of Staus that meant from 160 to 320 cfm with the 2-panel collector array An in-line fan was used to push/pull the air through the closed system of 4-in corrugated drain tiles Staus prepared the base for the greenhouse by excavating 4 ft of soil and laying down 2-in rigid Styrofoam panels The same insulation was attached to the first 2 ft of temporary 4-ft high 2 by 4-in sidewalls The remaining 2 ft of sidewall received 4 in of insulation “We laid one layer of heat tubes over the insulation with tubes on 16-in centers ” says Staus “They were covered with a foot of sand followed by a second layer of heat tubes perpendicular to the first They were covered with about 6 in of sand ” Dirt was piled against the exterior of the insulated walls and also brought in to cover the sand Staus filled the remainder of the space with about 20 yards of compost from a local provider before installing the high tunnel over the base “The compost makes great beds ” says Staus “Everything is laid out in 20-in rows with walking paths in between The plants are attached to a trellis or to strings attached to overhead frames ” Now in his third year with the heated high tunnel Staus is even more enthused about its potential In the summer even with sides open and an exhaust fan running the high tunnel can reach temperatures close to 100° While disease was a problem the first year Staus thinks he has found the answer “We prune the lower leaves away to encourage air flow and have fans to constantly circulate the air he says It was the stagnant air that caused the problem By the middle of last year we had stopped using any fungicides and this year we ve used none and also no insecticides ” Staus is confident he is getting twice the production of an open-air system Pruned to grow on strings he is able to plant tomatoes on 12-in centers Water is controlled with drip irrigation in every bed He says this also helps control disease The next step for Staus is hot water-heated beds Even with the hot air-heated ground seeds are slow to germinate Staus wants to get beds into the 70-degree range so seeds will germinate quickly “I am putting tubes under 6 in of raised beds and will use solar panels to heat the water that will be pumped through them says Staus “With the hot air I was able to plant potatoes in March after the coldest winter in Minnesota history I hope to be able to start using the water-heated beds in February ” Staus estimates the cost of the high tunnel and closed loop soil heating system at about $18 000 The two panels were about $1 500 each and the system required around 1 500 ft of tubing Staus is retired and sees the system as an on-going experiment that lets him test out ideas As a bonus it can easily feed at least two families for much of the year “Production is phenomenal ” says Staus “We feed ourselves and share with friends and family ” Contact: FARM SHOW Followup Richard Staus Hastings Minn brush e creek@gmail com or Rural Renewable
Energy Alliance 2330 Dancing Wind Rd S W Suite #2
Pine River Minn
56474 ph 218 587-4753; info@rreal org; www rreal org
To read the rest of this story, download this issue below or click here to register with your account number.