2015 - Volume #39, Issue #2, Page #10
[ Sample Stories From This Issue | List of All Stories In This Issue | Print this story
| Read this issue]
They Sell Plants Off “Living Towers”
![]() |
![]() |
![]() |
The tower’s design was part of his doctoral research 4 years ago. The past two years he began marketing it in the U.S. and internationally. Besides selling a product, Storey emphasizes educational support ‑ before the sale ‑ to ensure success. Based on more than 100 YouTube videos and a diverse range of business models created by customers, the combination seems to be working.
The Science
After extensive research, Storey decided that growing on all 4 sides of vertical units is inefficient.
“With the sun angle it wastes resources (especially in greenhouses in the northern states). So ZipGrow towers are one-sided with reflective surfaces of titanium dioxide on the other sides,” Storey explains.
The 4 by 4-in. by 5-ft. tall ZipGrow towers are also light and modular, made of extruded food-grade pvc. Plants grow in Matrix Media, made of recycled water bottles and a binder that is lightweight, durable and has a high biological surface area for microbes to live on to foster healthy plant growth. The media also has plenty of open spaces for water to move through and help maintain steady root zone temperatures.
“The towers can grow almost any crop with any spacing,” Storey says. He sells complete systems, but notes that most customers purchase the ZipGrow Tower components (starting at $50/each) and tie them into their own systems.
From the U.S. to Africa to the Middle East, he is amazed at the diversity of systems customers have come up with.
“Our product is like the Lego blocks of hydroponic growing,” Storey says.
Shipping Container Gardening
ZipGrow towers are integral to Freight Farms’ turnkey hydroponic “Leafy Green Machine” (LGM) set up in shipping containers, says Caroline Katsiroubas, marketing manager for the Boston, Mass., company (www.freightfarms.com).
“There are 256 towers in each container. They are easy to move, transplant and grow and are more efficient in terms of labor and space,” she says. The company researched vertical systems and chose Storey’s towers based on his extensive research and the trust he earned in the hydroponic industry for developing a proven product.
Besides the towers, Freight Farms sets up the 8 by 40-ft. containers with lights and climate controls to provide the perfect environment to grow lettuces, brassicas and herbs. For example, one Leafy Green Machine can produce 500 heads of lettuce a week.
“We are targeting institution food service groups,” Katsiroubas says. Customers include hotels, schools and wholesale produce distribution companies.
Farmers Market
In Rochester, Minn., Chris Lukenbill (www.freshwithedge.com) transports ZipGrow Towers filled with leafy greens and herbs to farmers markets, restaurants and food cooperatives, where customers and chefs can harvest whatever they need.
“That differentiates our product and is the most ideal for longevity,” he says. “It’s interactive. It intrigues people, and they can also see that it’s fresh.”
He starts the towers in his greenhouse with up to six varieties in each tower. He uses an enclosed trailer to deliver the towers, pump, battery and water needed to run the system.
At farmers markets or co-ops, customers can cut their own greens, which are weighed and charged by the ounce. At a restaurant, the system is located where diners can see it and watch as the chef cuts fresh herbs for their meals. With an LED light system, the produce continues to grow until it’s harvested, and Lukenbill services his customers by switching out the harvested towers with new filled towers.
“The beauty of the ZipGrow Tower is its simplicity. I build displays around them. They are very encompassing and flexible,” Lukenbill says. “In comparison to other systems, the cost per plant is much lower.”
Haydn Christensen, one of ZipGrow’s first customers, offers a similar service in Ft. Collins, Colo., growing a variety of herbs and greens for his CSA, restaurants, stores and farmers markets.
“I take a tower to the store, and customers do all the harvesting labor,” he says. His company, BayBerry Fresh (www.babyberryfresh) was the first to sell live plants at Whole Foods. By adding LED and T5 lighting to a heated space in his greenhouse, he’s developed a system with the towers to grow basil in winter.
Living Walls
The living walls that Teryl Chapel creates provide architectural variety yet also produce edible plants.
The founder of City Planet Farms (www.cityplanetfarms.com) incorporates ZipGrow Towers into an aquaponic system. A wall he designed for a high-end restaurant in Sag Harbor, Maine, with water re-circulating through the plants and three fish tanks, is a good example of taking the towers to a new level.
“The white towers fit in and are easy to hang and move,” Chapel says.
Because of the distance from his home in Manhattan to the restaurant, he set up the system and trained an employee to do the maintenance ‑ cleaning, feeding the koi and tilapia, keeping the pump and tanks maintained, etc. To change out harvested ZipGrow towers, Chapel set up an 80-sq. ft. aquaponic system in the restaurant’s basement with more fish and towers.
“They grow greens, herbs, cherry tomatoes, cucumbers and celery for Bloody Marys,” Chapel says.
He also sets up seasonal living walls on rooftops and small displays in Harlem schools and for a non-profit sustainable group as part of his interest in educating others about aquaponics for sustainable and natural systems.
“I’ve been focusing on urban applications for access to fresh produce,” Chapel says, including figuring out how to get in unlikely places such as airport food courts.
The simplicity and portability of ZipGrow Towers makes that possible.
Contact: FARM SHOW Followup, Nate Storey, Bright AgroTech LLC, 1938 Harney St., Laramie, Wyo. 82072 (ph 307 766-6538; info@brightagrotech.com; www.brightagrotech.com).
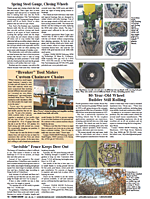
Click here to download page story appeared in.
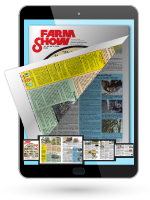
Click here to read entire issue
To read the rest of this story, download this issue below or click here to register with your account number.