You have reached your limit of 3 free stories. A story preview is shown instead.
To view more stories
(If your subscription is current,
click here to Login or Register.)
They Make Compost All Winter And Get Heat, Too
A prototype insulated compost bin made high quality compost in the dead of an Iowa winter and produced heat for a greenhouse as a bonus. Practical Farmers of Iowa energy consultant Rich Schuler said the idea showed a lot of promise but needs more work to be economical.
“The idea was to make quality compost with
..........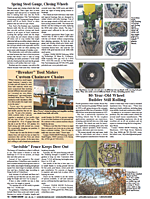
You must sign in, subscribe or renew to see the page.
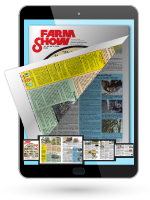
You must sign in, subscribe or renew to see the flip-book
They Make Compost All Winter And Get Heat Too ENERGY Alternative Fuels A prototype insulated compost bin made high quality compost in the dead of an Iowa winter and produced heat for a greenhouse as a bonus Practical Farmers of Iowa energy consultant Rich Schuler said the idea showed a lot of promise but needs more work to be economical “The idea was to make quality compost without turning by pushing air through the pile and pulling heat from the center of the pile to keep it under 150°F says Schuler We had to put a 100-ft coil of stainless steel in the center of the pile which required hand labor for loading and unloading The key to the system is the combination of insulation and heat storage with 2 heat exchangers moving heat from one to the other The 4 by 4 by 9-ft composting chamber is designed around 4 by 8-ft sheets of plywood with 2 by 4-in framing Insulation was placed between the 2 by 4 s and 1 1/2-in sheets of insulation were mounted to the insides of the plywood sheets Cedar fencing was used on the inside to protect the sheets of insulation during filling and removal of compost An adjacent heat storage chamber of four 275-gal commercial food totes filled with water is similarly insulated Water pumped through the stainless steel tubing harvests the 145°F heat at the center of the compost pile and carried it to the water tanks A second set of copper tubes carries tank water through an air exhaust system exchange It consists of a bank of 8 pvc pipes running the length of the pile A blower pushes air into the bottom of the chamber As it passes through the compost the air feeds the composting process It also picks up heat and moisture The warm air moves through a manifold into the pvc tubes Water pumped through 4 copper pipes in each tube harvested heat from the air and transferred it to the tanks The cooled air recirculates with retained moisture back through the compost Oxygen sensors let Schuler know if fresh air needs to be added The low volume blower that moves the air as well as the low power water pumps are powered by a 135-watt solar panel The blower barely provides positive pressure says Schuler The heat exchangers work like a trickle charger It generates the equivalent of about 1/2 gal of LP a day in BTU s and raises the temperature of the water about 10°F a week I don t think we broke 110°F due in part to the poly composition of the tanks The final step in the process was to use the heat to warm greenhouse beds Although the water tanks are heated gradually the heat can be pulled out as quickly as needed PEX tubes laid under beds in an adjacent greenhouse are designed to warm the soil in the beds and speed seedling growth The goal was to replace an expensive LP space heater mounted near the ceiling of the plastic-covered greenhouse Even though temperatures fell to 20°F below zero the system was able to keep the soil from freezing This year he plans to try a heat exchanger with a vertical tube and 2 horizontal tubes in the center Contact: FARM SHOW Followup Practical Farmers of Iowa 600 Fifth St Suite 100 Ames Iowa 50010 ph 515 232-5661; info@practicalfarmers org; www practicalfarmers org
To read the rest of this story, download this issue below or click
here to register with your account number.