Powder-Coat Extends Life Of Metal Parts
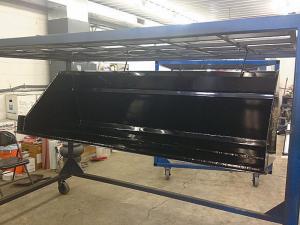 ✖  |
Chris Borning makes a good living powder-coating all kinds of metal objects big and small for farms and other industries. As a motocross racer in high school, he discovered powder-coated parts looked better and the finish lasted longer than paint. He went on to launch his business, C&L Powder Coating. He says his customers like the speed of the process and the durability of the coating.
As soon as the coated part comes out of the curing oven and cools, it is ready to go, says Borning.
Powder coating is a multi-step process. Older parts may be sandblasted, while new parts often go through an acid wash process. Then the powder is electrostatically charged to stick to the bare metal as it is applied. When the part goes into the oven, the powder liquefies and bonds to the surface.
The cure time is 10 min. at around 400°F," explains Borning. "Actual time in the oven depends on the thickness of the metal. Curing is achieved when the entire part reaches the required temperature for the full time."
The size of the oven can be the limiting factor. C&L started out in 2009 with a 6 by 6 by 10-ft. oven. This past summer they added an 8 by 8 by 22-ft. oven to handle bigger jobs, like a request to coat 6 Deere tractor wheels.
"The farmer had planned to get them painted, but decided to go with powder coating," says Borning. "We sandblasted them and applied a primer, top coat and clear coat. I put a 1-year warranty on the finish, but I expect he won't have to touch those wheels for 20 years."
Borning explains that the number of coats and the powder used can depend on how the product will be used and where. He won't do an automotive wheel if the customer doesn't agree to all the proper steps.
"Wheels take a lot of abuse and often don't get cleaned," he says. "If you don't go with the primer, color coat and top coat, you're asking for failure."
Different powders offer different features, such as UV protection with polyurethanes, and rust and acid protection with epoxies.
"We may use an epoxy primer with a poly topcoat," says Borning. "Acids won't eat through the epoxy, and you get the color you want with the poly, plus UV protection to keep it from fading."
Color choices used to be limited, but that has changed. "One powder manufacturer has more than 6,500 colors," says Borning. "You can even get special textures like wrinkles."
Special colors can also add to the cost. He notes that the yellow for the Deere tractor wheels costs around $9/lb. Each job is bid accordingly. The Deere wheels were approximately $150 each.
Limiting factors to powder coating are the thickness of the part and the ability to hold it at the right temperature.
Borning suggests that FARM SHOW readers interested in powder-coating should give him a call to discuss size, expected use and shipping. If considering other powder coaters, he recommends comparing the steps they follow and coats they recommend. He points out that not all powder-coating is the same.
"I have a regular customer from Illinois who ships parts for us to coat," says Borning. "He went through 5 different powder-coating operations before he tried us and was satisfied. It is a matter of quality and the time the operator is willing to put into the job."
Contact: FARM SHOW Followup, C&L Powder Coating, LLC; 279 4th St., P.O. Box 136, Echo, Minn. 56237 (ph 507 828-1233; c_borning@hotmail.com; www.clpowdercoating.com).
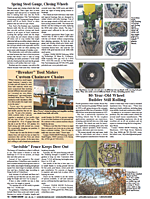
Click here to download page story appeared in.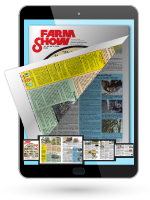
Click here to read entire issue
Powder-Coat Extends Life Of Metal Parts SPECIALTY/SERVICES Chris Borning makes a good living powder-coating all kinds of metal objects big and small for farms and other industries As a motocross racer in high school he discovered powder-coated parts looked better and the finish lasted longer than paint He went on to launch his business C&L Powder Coating He says his customers like the speed of the process and the durability of the coating As soon as the coated part comes out of the curing oven and cools it is ready to go says Borning Powder coating is a multi-step process Older parts may be sandblasted while new parts often go through an acid wash process Then the powder is electrostatically charged to stick to the bare metal as it is applied When the part goes into the oven the powder liquefies and bonds to the surface The cure time is 10 min at around 400°F explains Borning Actual time in the oven depends on the thickness of the metal Curing is achieved when the entire part reaches the required temperature for the full time The size of the oven can be the limiting factor C&L started out in 2009 with a 6 by 6 by 10-ft oven This past summer they added an 8 by 8 by 22-ft oven to handle bigger jobs like a request to coat 6 Deere tractor wheels The farmer had planned to get them painted but decided to go with powder coating says Borning We sandblasted them and applied a primer top coat and clear coat I put a 1-year warranty on the finish but I expect he won t have to touch those wheels for 20 years Borning explains that the number of coats and the powder used can depend on how the product will be used and where He won t do an automotive wheel if the customer doesn t agree to all the proper steps Wheels take a lot of abuse and often don t get cleaned he says If you don t go with the primer color coat and top coat you re asking for failure Different powders offer different features such as UV protection with polyurethanes and rust and acid protection with epoxies We may use an epoxy primer with a poly topcoat says Borning Acids won t eat through the epoxy and you get the color you want with the poly plus UV protection to keep it from fading Color choices used to be limited but that has changed One powder manufacturer has more than 6 500 colors says Borning You can even get special textures like wrinkles Special colors can also add to the cost He notes that the yellow for the Deere tractor wheels costs around $9/lb Each job is bid accordingly The Deere wheels were approximately $150 each Limiting factors to powder coating are the thickness of the part and the ability to hold it at the right temperature Borning suggests that FARM SHOW readers interested in powder-coating should give him a call to discuss size expected use and shipping If considering other powder coaters he recommends comparing the steps they follow and coats they recommend He points out that not all powder-coating is the same I have a regular customer from Illinois who ships parts for us to coat says Borning He went through 5 different powder-coating operations before he tried us and was satisfied It is a matter of quality and the time the operator is willing to put into the job Contact: FARM SHOW Followup C&L Powder Coating LLC; 279 4th St P O Box 136 Echo Minn 56237 ph 507 828-1233; c_borning@hotmail com; www clpowdercoating com
To read the rest of this story, download this issue below or click
here to register with your account number.