You have reached your limit of 3 free stories. A story preview is shown instead.
To view more stories
To view more stories
SUBSCRIBE OR RENEW NOW
(If your subscription is current, click here to Login or Register.)2014 - Volume #38, Issue #2, Page #25
[ Sample Stories From This Issue | List of All Stories In This Issue]
"Made It Myself" Sprayer Built From Cotton Picker
Peter Wilson, Chester, S.C., needed an “air boom” sprayer for his vegetable and strawberry crops, so he converted an old cotton picker. The air system that previously moved cotton lint to the basket now creates a high-pressure fog that penetrates the canopy across a 48-ft. swath.“I had looked at a couple of..........
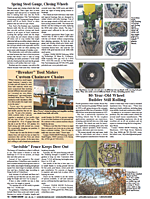
You must sign in, subscribe or renew to see the page.
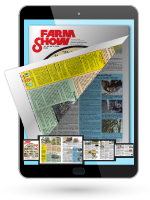
You must sign in, subscribe or renew to see the flip-book
Made It Myself Sprayer Built From Cotton Picker SPRAYING Miscellaneous Peter Wilson Chester S C needed an “air boom” sprayer for his vegetable and strawberry crops so he converted an old cotton picker The air system that previously moved cotton lint to the basket now creates a high-pressure fog that penetrates the canopy across a 48-ft swath “I had looked at a couple of air boom sprayers mounted on trailers but they were expensive would require a cab tractor to pull them and lacked some features I wanted ” says Wilson “We raise cotton so we know how powerful the fans are on pickers With the help of my dad Jeff and my wife Caroline we converted an old Case IH cotton picker to a multi-section air boom sprayer ” Wilson wanted a sprayer that could move quickly and safely from one pesticide to another That meant multiple tanks and a good clean-out system that would flush out chemicals between crops “We used an 1844 Case IH 4-row picker with worn out headers ” says Wilson “The rest of the machine was in good shape and the engine had low hours ” Removing the headers was easy To remove the big lint basket Wilson lifted it into the air Then he built a wooden frame on 8-ft posts under it “I set the basket back down on the frame disconnected it from the picker and drove out from underneath it ” says Wilson After stripping away much of the remaining body he assembled back and side booms using square tubing He purchased 35 specialty spray nozzles from a sprayer company and mounted 5 per section Each of the 2 sections per boom and the rear-mounted boom can be shut off individually “I built them on the ground and lifted them into place ” says Wilson “They can be easily removed if needed ” The side booms attach to a center frame fabricated from rectangular tubing It’s mounted to the lint basket’s front sliding track Each side boom connects to the center frame with a pair of ball and receiver hitches “They are rated for 3 000 lbs so they are plenty strong ” says Wilson “They made the booms easy to mount and easy to dismount if I need to do so ” The sliding track lets Wilson drop spray tips to as low as 18 in off the ground for strawberries or as high as 7 ft for staked tomatoes He uses the picker’s hydraulic system for boom control and more Hydraulic cylinders mounted between the booms and the frame let him fold the booms back for transport “The sliding track gives the top of the boom framework a maximum height of 13 to 14 ft ” says Wilson “I bolted the booms and frames rather than weld them If nuts and bolts come loose you can tighten them but if a weld breaks you’ve got big trouble ” He mounted a high-pressure hydraulic-powered spray pump powered by the hydraulic valve that previously supplied fluid to the cotton unloader motor It has a maximum pressure of 300 psi to the picker/sprayer However it’s the added air pressure that really delivers the fine spray “I connected the air flow from the large twin fans on the picker that moved the cotton to 5-in flexible piping which then reduces to 4-in pvc drop tubes ” says Wilson “The spray nozzles are centered in the tubes I can spray with just the conventional pump and nozzles or I can add air pressure from the fans When I turn on the fans it breaks the spray up real fine and blasts it into the foliage ” Wilson reinforced the frame so he could mount three 200-gal spray tanks where the basket had been The multiple tanks let him mix up three solutions before going to the field He retained the two 100-gal tanks used on the picker for water and spindle cleaner They now provide clean water for flushing tanks booms and nozzles “I can move clean water to empty tanks or to the booms as needed ” says Wilson “I can also switch tanks on the go ” To control the various nozzle sections tanks and returns Wilson mounted a 10-toggle control panel in the cab Pneumatic air cylinders fed by a 12-volt compressor open and close ball valves with the flip of a switch “The hydrostatic transmission on the 1844 makes it easy to find the right speed for spraying ” says Wilson “The cab is spacious and the controls are easy to reach With help from my family the entire project took about 2 months to complete Every time I got stuck my dad seemed to have an idea that got us going again ” Contact: FARM SHOW Followup Peter Wilson 3921 Armenia Rd Chester S C 29706 ph 803 385-7695; peter wilson@cottonhillsfarm com
To read the rest of this story, download this issue below or click here to register with your account number.