Farm Group Turns Big Bales Into Fuel Pellets
This past winter, six farmers in New York state didn’t have to worry about the big increases in the cost of heating fuel. They grew their own fuel, without taking any of their land out of crop production. They heated with pellet stoves and boilers, using pellets made from poor quality hay they baled on their farms. The farmers were part of a pilot project with the Hudson Valley Grass Energy (HVGE), which is developing a mobile pelleter.
It uses the same technology that’s used to make pellets at feed mills, says HVGE project coordinator Bob Thomas, a grass energy consultant. But mobilizing it offers great opportunity for farmers anywhere in the country.
The pelleter includes a hammer mill, buffer bin, steam generator, pellet mill, pellet cooling tower-shaker, and diesel-powered electricity generator. It all mounts on a trailer.
The farmers baled hay and grass at about 10 to 15 percent moisture. Each farmer provided a tractor (90 hp or more) to run a tub grinder and another tractor with an operator to load bales in the grinder and remove “supersacks” (averaging 1,500 lbs.) of finished pellets. The bales are ground in the grinder before going into the pelleter, which makes an average of about 1 ton of pellets/hour, but can make as much as 2 tons/hour. Nothing is added to bind the pellets but steam, which is used when needed. Because grass has less lignin, more die time is needed then with woody materials.
According to a Cornell University study, an average household burns 3 to 5 tons of pellets per heating season, Thomas says. Farmers can easily get that amount off 3 acres.
As part of the pilot with grant funding, farmers paid $75/ton for processing, plus $3 per bag. To be sustainable the price will go up slightly, Thomas says. But the farmers, who had to invest in multi-fuel heating systems (spending from $1,800 to $6,000), were very pleased with the project and have been spreading the word to other farmers.
Thomas notes that wood pellet stoves won’t work. The hay/grass pellets require the active burn pot used in multi-fuel stoves. One disadvantage with the hay pellets is that they leave more ash behind, 3 to 5 percent, compared to 1 percent or less with wood pellets.
But the farmers in the project aren’t complaining about having to clean out more ash. Pellet fuel saves 50 to 70 percent off the cost of using fuel oil or propane for heating. And, hay/grass pellets produce the same btu’s as wood pellets (8,000 to 8,500 btu’s/lb.). Besides growing their own heating fuel, the farmers recognize an opportunity to market the pellets, which currently sell for $225/ton.
As a grass energy consultant, Thomas says the mobile pelleter technology could be used anywhere. The unit used in New York continues to be improved, including the plan to run it off 3-phase power when available rather than Genset diesel.
He will consult and travel anywhere in the U.S. to meet with farmers or cooperatives interested in starting a similar operation in other regions of the country.
“I want to see farmers become our fuel distributors,” he says. “There are millions of potential acres that are fallow or produce poor hay that will not take land out of crop production for food.”
Contact: FARM SHOW Followup, Bob Thomas, Hudson Valley Grass Energy/Renewable Energy Center, 5 Park Lane, Highland, N.Y. 12528 (ph 845 800-0996; cell 570 470-1305; bob@renewableenergycenter.org; www.renewableenergycenter.org; www.hvgenergy.wordpress.com).
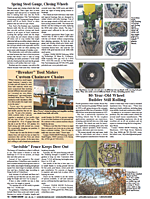
Click here to download page story appeared in.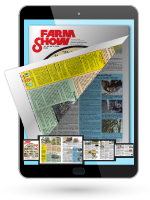
Click here to read entire issue
Farm Group Turns Big Bales Into Fuel Pellets BALE HANDLING This past winter six farmers in New York state didn’t have to worry about the big increases in the cost of heating fuel They grew their own fuel without taking any of their land out of crop production They heated with pellet stoves and boilers using pellets made from poor quality hay they baled on their farms The farmers were part of a pilot project with the Hudson Valley Grass Energy HVGE which is developing a mobile pelleter It uses the same technology that’s used to make pellets at feed mills says HVGE project coordinator Bob Thomas a grass energy consultant But mobilizing it offers great opportunity for farmers anywhere in the country The pelleter includes a hammer mill buffer bin steam generator pellet mill pellet cooling tower-shaker and diesel-powered electricity generator It all mounts on a trailer The farmers baled hay and grass at about 10 to 15 percent moisture Each farmer provided a tractor 90 hp or more to run a tub grinder and another tractor with an operator to load bales in the grinder and remove “supersacks” averaging 1 500 lbs of finished pellets The bales are ground in the grinder before going into the pelleter which makes an average of about 1 ton of pellets/hour but can make as much as 2 tons/hour Nothing is added to bind the pellets but steam which is used when needed Because grass has less lignin more die time is needed then with woody materials According to a Cornell University study an average household burns 3 to 5 tons of pellets per heating season Thomas says Farmers can easily get that amount off 3 acres As part of the pilot with grant funding farmers paid $75/ton for processing plus $3 per bag To be sustainable the price will go up slightly Thomas says But the farmers who had to invest in multi-fuel heating systems spending from $1 800 to $6 000 were very pleased with the project and have been spreading the word to other farmers Thomas notes that wood pellet stoves won’t work The hay/grass pellets require the active burn pot used in multi-fuel stoves One disadvantage with the hay pellets is that they leave more ash behind 3 to 5 percent compared to 1 percent or less with wood pellets But the farmers in the project aren’t complaining about having to clean out more ash Pellet fuel saves 50 to 70 percent off the cost of using fuel oil or propane for heating And hay/grass pellets produce the same btu’s as wood pellets 8 000 to 8 500 btu’s/lb Besides growing their own heating fuel the farmers recognize an opportunity to market the pellets which currently sell for $225/ton As a grass energy consultant Thomas says the mobile pelleter technology could be used anywhere The unit used in New York continues to be improved including the plan to run it off 3-phase power when available rather than Genset diesel He will consult and travel anywhere in the U S to meet with farmers or cooperatives interested in starting a similar operation in other regions of the country “I want to see farmers become our fuel distributors ” he says “There are millions of potential acres that are fallow or produce poor hay that will not take land out of crop production for food ” Contact: FARM SHOW Followup Bob Thomas Hudson Valley Grass Energy/Renewable Energy Center 5 Park Lane Highland N Y 12528 ph 845 800-0996; cell 570 470-1305; bob@renewableenergycenter org; www renewableenergycenter org; www hvgenergy wordpress com
To read the rest of this story, download this issue below or click
here to register with your account number.