2014 - Volume #38, Issue #1, Page #16
[ Sample Stories From This Issue | List of All Stories In This Issue | Print this story
| Read this issue]
Plastic Liners Keep Buckets Clean
![]() |
![]() |
![]() |
“I’ve done dirt moving for 20 years and always had stuff sticking in the bucket,” says Julian. “I tried all kinds of things until I came up with a way to use UHMW poly. Nothing sticks to it. “
Some formulations of UHMW poly are 15 times more abrasion resistant than steel. It’s also highly resistant to corrosive chemicals, has low moisture absorption, and is very slippery.
Julian buys poly in sheets and cuts it to fit. The trick is how to shape it and bond it to a bucket. Rollout buckets with their many adjacent surfaces were a special challenge, but even a simple curved bucket with 2 ends has 2 seams to seal.
“You need a tight connection that seals out moisture and contaminates from getting behind the liner,” explains Julian. “Plastic welding is normally a gluey thing. If you heat the UHMW enough to melt it, it usually burns. I came up with a way to get welds that are unheard of in the industry.”
Through extensive research, as well as trial and error, he identified equipment that would let him heat the UHMW enough to shape it to fit a bucket. As it cooled, the poly fibers hardened into the new shape.
A second challenge came from creating a single solid surface where the bucket lining requires multiple pieces. Julian’s method includes using a custom-made brass tip that liquefies the edges of the UHMW liner pieces and plastic emerging from his welding gun. The 3 plastics blend in their liquid state. As they cool, they produce a hard, curved joint.
Another challenge was how to affix the UHMW to hardened steel buckets. Again research and experimentation provided an answer. Julian came up with what he views as a trade secret, a way to attach special metal fasteners through the plastic to the steel bucket.
Edges of the plastic require special treatment as well. Julian starts by dadoing the edge of the plastic, then attaching a strip of double offset steel over the edge of the plastic and spot welding it to the bucket edge.
“I use high tensile steel 7/16 in. thick and 2 1/4 in. wide, laser cut for plug welds,” explains Julian. “I can use 6 lbs. of welding wire securing the bottom edge and side edges of a liner on a big bucket. On the top edge of a liner, I may use a strip of angle iron. The majority of the time that edge doesn’t even get dirty.”
Julian prices each job individually, depending on the type of UHMW and the thickness that he uses. Labor is a big part of the cost. Large rollout buckets with many surfaces and angles can take 80 hrs. to do and cost $5,000 to $6,000. A simple payloader bucket may require 18 to 20 hrs., while a smaller skid steer bucket can take just as much time because of the difficulty of welding in the confined space.
“I don’t do many skid steer buckets because people hesitate to pay as much for a liner as they did for the bucket,” says Julian. “However, the operator is more efficient with the lined bucket, and doesn’t spend time trying to shake stuff out or banging it up and down.”
Julian points out that time savings, combined with reduced maintenance and extended bucket and hydraulic cylinder life, can more than pay for a liner.
Contact: FARM SHOW Followup, Dave Julian, PayLiner (ph 605 695-2196; www.payliner.biz).
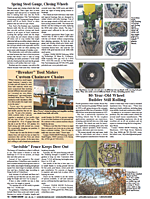
Click here to view page story appeared in
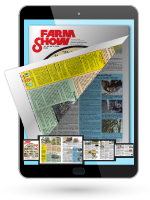
Click here to read entire issue