"Made It Myself" Cornhead Built To Harvest Faster
Ross Bishop hopes his home-built IH cornhead will run faster than the old head on his 2166 International combine. He also expects it to leave corn residue in better shape. The “made it myself” head contains parts of three International 38-in., 4-row cornheads.
“Prior to 1997, I ran an International 1066, 6-row cornhead on 30-in. rows, and it chopped stalks up nicely,” explains Bishop. “When I went to 20-in. rows, I built an 8-row cornhead to match out of two 30-in., 4-row Deere cornheads. It couldn’t take crop at more than 4 mph, though the combine had more capacity and it had no chopping rolls at all. No-tilling into the fields in the spring was a disaster.”
So, Bishop spent an additional $4,000 to $5,000 on Deere rolls and knives. That helped, but it wasn’t the answer. After some delay for health issues, he finally decided to start over, this time using all International parts.
“I extended the main frame on my old 1066, 30-in. 6-row from 12 ft. to 13 ft., 8 in. and extended the auger by 13 in. on either end,” recalls Bishop. “Getting the auger properly measured and welded together was one of the most difficult challenges of the process.”
Bishop bought new Calmer 20-in. header snouts and remounted his existing 30-in. row units. Here he ran into his second major challenge. The row units had 10-tooth sprockets on gathering chains. When condensed to 20-in. spacing, the neighboring chains jammed, and a shaft broke on one. Bishop called Calmer founder Marion Calmer, thinking he would need to order Calmer sprockets and shafts. Doing so would require tearing the gearboxes apart. Calmer suggested simply trying an 8-tooth sprocket.
“Deere had an 8-tooth that fit my existing smooth shafts with some modification,” says Bishop. “I had to drill holes through the sprocket to match the roll-pin hole in the International shaft.”
He also welded a notch on the round shafts so the hexagon-shaped sprockets would fit tighter. Another problem was matching the sprocket width to the shaft. He found that shaving 1/4 in. off the bottom part that protects the gearbox was sufficient.
The cost of parts for the International 20-in. 8-row cornhead came to around $10,000. Over time, however, working his way up from 6-row to 8-row he spent about $50,000. Among other things, he had to replace tires and add duals for more stability on the road.
To see how Bishop assembled his cornhead, check out the video at www.farmshow.com.
Contact: FARM SHOW Followup, Ross Bishop, 1930 Western Ave., Jackson, Wis. 53037 (ph 414 531-8531; rbishop@milwpc.com).
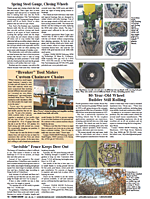
Click here to download page story appeared in.
Made It Myself Cornhead Built To Harvest Faster COMBINES Headers Ross Bishop hopes his home-built IH cornhead will run faster than the old head on his 2166 International combine He also expects it to leave corn residue in better shape The “made it myself” head contains parts of three International 38-in 4-row cornheads “Prior to 1997 I ran an International 1066 6-row cornhead on 30-in rows and it chopped stalks up nicely ” explains Bishop “When I went to 20-in rows I built an 8-row cornhead to match out of two 30-in 4-row Deere cornheads It couldn’t take crop at more than 4 mph though the combine had more capacity and it had no chopping rolls at all No-tilling into the fields in the spring was a disaster ” So Bishop spent an additional $4 000 to $5 000 on Deere rolls and knives That helped but it wasn’t the answer After some delay for health issues he finally decided to start over this time using all International parts “I extended the main frame on my old 1066 30-in 6-row from 12 ft to 13 ft 8 in and extended the auger by 13 in on either end ” recalls Bishop “Getting the auger properly measured and welded together was one of the most difficult challenges of the process ” Bishop bought new Calmer 20-in header snouts and remounted his existing 30-in row units Here he ran into his second major challenge The row units had 10-tooth sprockets on gathering chains When condensed to 20-in spacing the neighboring chains jammed and a shaft broke on one Bishop called Calmer founder Marion Calmer thinking he would need to order Calmer sprockets and shafts Doing so would require tearing the gearboxes apart Calmer suggested simply trying an 8-tooth sprocket “Deere had an 8-tooth that fit my existing smooth shafts with some modification ” says Bishop “I had to drill holes through the sprocket to match the roll-pin hole in the International shaft ” He also welded a notch on the round shafts so the hexagon-shaped sprockets would fit tighter Another problem was matching the sprocket width to the shaft He found that shaving 1/4 in off the bottom part that protects the gearbox was sufficient The cost of parts for the International 20-in 8-row cornhead came to around $10 000 Over time however working his way up from 6-row to 8-row he spent about $50 000 Among other things he had to replace tires and add duals for more stability on the road To see how Bishop assembled his cornhead check out the video at www farmshow com Contact: FARM SHOW Followup Ross Bishop 1930 Western Ave Jackson Wis 53037 ph 414 531-8531; rbishop@milwpc com
To read the rest of this story, download this issue below or click
here to register with your account number.