You have reached your limit of 3 free stories. A story preview is shown instead.
To view more stories
(If your subscription is current,
click here to Login or Register.)
They Saved Thousands On Grain System Components
Tim Kelly says it would’ve been easy to spend more than $100,000 to equip his grain setup (see story above) with the parts and components that he and his son acquired used or built themselves for about a quarter of that cost. “There’s really no end to what a person can spend when it comes to a project like this,” Kelly
..........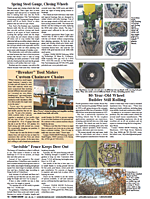
You must sign in, subscribe or renew to see the page.
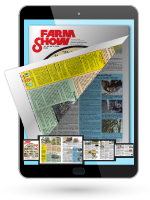
You must sign in, subscribe or renew to see the flip-book
They Saved Thousands On Grain System Components CROP STORAGE Grain Storage Tim Kelly says it would’ve been easy to spend more than $100 000 to equip his grain setup see story above with the parts and components that he and his son acquired used or built themselves for about a quarter of that cost “There’s really no end to what a person can spend when it comes to a project like this ” Kelly says “and its real easy to spend way more than what’s practical ” Fortunately Kelly and his sons Matthew and Shannon are master do-it-yourselfers who if they can’t find a good functioning used part will build it themselves
Matthew is a licensed electrician who often works on large commercial projects With that background he was able to acquire several used parts for the electrical portion of his dad’s new home-built grain setup He located good quality 2 by 4-ft electrical boxes and breaker panels that had been removed from a commercial manufacturing plant paying pennies on the dollar He found fuses the size of a stick of dynamite which cost $1 500 new for $30 apiece Two dozen capacitors were outdated for a large plant and would’ve cost several thousand dollars new Again he paid cents on the dollar When the electrical system design called for a 10-in square metal trough to run cables Tim had a local metal shop make it for a few hundred dollars rather than pay $1 500 for a new one from an electrical supply company
Tim got his biggest shock however when he asked the power company the cost for running 3-phase power to his farm “I about fell over when they told me it would be more than $200 000 ” Tim says “So the boys and I talked it over and we decided to build our own 3-phase system ”
They located a used 150 hp motor and built a converter that changes 7 500 volts of single-phase power into 1 200 amps of 3-phase power A commercially available clutch to slowly engage the motor would’ve cost a couple thousand dollars so Tim and the boys built a lever-activated version themselves that works great Their only cost was to buy a few belts and spend a few hours to fabricate the device from used steel parts
They also reduced costs by designing and building their own conveyor beneath the pit The rugged truss-type frame is mounted on wheels so it can easily swing between one grain lift and the other The sliding door that feeds grain onto the conveyor opens and closes through a clever chain gear and lever mechanism that Tim designed and built The control is mounted on a vertical pipe near the grain pit which the semi-tractor driver opens and closes with the same wrench he uses for the lift gates on his grain hopper
“We build things that make grain handling easier and more efficient ” says Tim “and we save money in the process ” Other examples of that mechanical prowess are the grain deflectors that Tim made to fit inside the distribution pipes at the top of the leg “Buying them from a supplier would’ve cost about $1 000 each ” says Tim “I made five of them myself in a week from a few hundred dollars of scrap metal and they work just fine ”
Contact: FARM SHOW Followup Tim Kelly 74861 262nd St Dassel Minn 55325 ph 320 286-2371
To read the rest of this story, download this issue below or click
here to register with your account number.