You have reached your limit of 3 free stories. A story preview is shown instead.
To view more stories
(If your subscription is current,
click here to Login or Register.)
“Puckey Sucker” Cleans Up Pastures And More
Sam McNair, Jr. cleans up his pasture with what he calls his Mark 2 Puckey Sucker. The homemade, tow-behind vacuum turns horse manure into a fluffy, dry material that’s ready to compost. It also works great on leaves, branches and stones.
“It costs less than $600 to put together and I haven’t found anything it
..........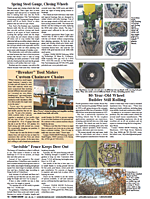
You must sign in, subscribe or renew to see the page.
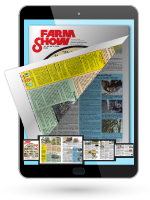
You must sign in, subscribe or renew to see the flip-book
“Puckey Sucker” Cleans Up Pastures And More MANURE HANDLING Sam McNair Jr cleans up his pasture with what he calls his Mark 2 Puckey Sucker The homemade tow-behind vacuum turns horse manure into a fluffy dry material that’s ready to compost It also works great on leaves branches and stones “It costs less than $600 to put together and I haven’t found anything it won’t pick up ” says McNair Getting a power unit was the easy part He picked up a 50 cc Husqvarna leaf blower The tougher part was deciding what to use for a vacuum vessel He decided to use heavy-duty Rubbermaid utility cart tubs The tubs had the volume and heavy-duty construction needed “You can’t use something too light or it will implode under vacuum ” explains McNair McNair mounted what would be the bottom half of his tank on an angle iron frame with its handles forward Heavy-duty wheels and axle salvaged from an old Sears riding lawn mower were mounted underneath the frame with a hitch for towing and a latch that allows the tub to tip to the rear Tube steel bolted to the tub’s rim forms the bottom mating surface The second tub with its handles pointed to the rear became the top half McNair bolted angle iron to its rim to create a flange to overlap the tube steel lip of the lower tub “The steel rims provide a mating surface but also serve to reinforce the tank when it’s under vacuum pressure ” he says At the front of the tank the top tub’s angle iron extended forward several inches to hinge with the lower tub Weatherstripping on the overlapping flange and caulk on both rims helps ensure a near airtight seal To get vacuum pressure McNair cut a hole on the top half of the tub and bolted the leaf blower’s intake to it A second and larger hole was also cut in the top tub “The opening is about 16 in by 24 in and covered with double layer nylon screen framed with 2 by 2-in wood You need enough surface area to ensure that the velocity of the air flow slows so material drops into the tank ” “Any entrained dust particles small enough to come through the screen continue through the blower fan and exhaust without a problem ” he says “The screen is loose enough that when the vacuum pressure shuts off it flexes and releases any material caught against it ” McNair cut 3 more holes in the top tub one in the wheel housing and 2 in the debris capture area of the tank one in front and one in the rear A piece of stove pipe with a cap inserted in the housing hole lets McNair clean out any debris that finds its way past the screen He inserted a piece of plastic pipe into the hole on the front of the tank The external stub serves to mount the vacuum hose Sections of pvc pipe at the end of the hose are used to suck up manure and debris McNair has fabricated a number of hose ends similar to those that come with shop vacs A piece of clear plastic mounted over the hole in the rear of the tub provides a viewing port to check the amount of material collected Gas springs attached between the two tubs hold them open when the bottom tub latch is released and they are tipped to the rear One problem McNair ran into was overheating of the blower motor To get more airflow he built a small motor shroud out of sheet metal Using a short piece of flexible hose and a right angle elbow inserted into the blower’s discharge he redirected air under the shroud Contact: FARM SHOW Followup Sam McNair 151 Croxton Road Williamston S C 29697
To read the rest of this story, download this issue below or click
here to register with your account number.