You have reached your limit of 3 free stories. A story preview is shown instead.
To view more stories
(If your subscription is current,
click here to Login or Register.)
Articulated Case Garden Tractor
Lee Matczak’s 222 Case garden tractor looks bigger than its 12 hp Kohler engine would suggest. With four big wheels, 4-WD, and full articulation and oscillation, it looks toolbar ready.
“A friend of mine bought two 222 Case garden tractors 20 years ago, intending to make an articulated one,” says Matczak. “H
..........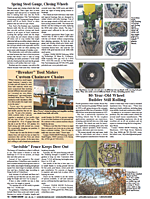
You must sign in, subscribe or renew to see the page.
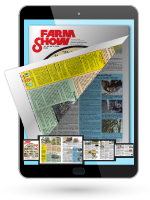
You must sign in, subscribe or renew to see the flip-book
Articulated Case Garden Tractor TRACTORS Made-It-Myself Lee Matczak’s 222 Case garden tractor looks bigger than its 12 hp Kohler engine would suggest With four big wheels 4-WD and full articulation and oscillation it looks toolbar ready “A friend of mine bought two 222 Case garden tractors 20 years ago intending to make an articulated one ” says Matczak “He never did so I bought them from him ” Matczak had been thinking about doing something similar with Cub Cadet tractors but getting the driveshaft through an articulating joint always stumped him The Case tractors had hydraulic drives which reduced the problem to hanging hoses Matczak started by removing the rear end from one and setting it under the front end of the second after removing its front axle Seeing it could work Matczak started disassembling and cutting “When I got down to the bare frame I could see where the frame channel irons were 3 1/2 in wide at the front By the time they go up and over the rear end they have narrowed to 2 1/2 in ” says Matczak “I decided to put the articulation joint at the point in the frame just before the channels begin to narrow ” Once he had cut the frame he could see the hydraulic valve body that provided power to the drive was exposed just ahead of the cut He found two 3 1/2-in channel irons and used them to extend the front end 3 in to get it past the valve body He then welded 3/8-in steel plates to the ends of the exposed frames in preparation for joining them back together “I welded two pieces of 3/8-in steel to the plate on the front end to form a clevis-type hitch and drilled holes for a pin ” explains Matczak “I made a second U-shaped clevis with 3/8-in plate to fit over the first drilled a hole and pinned the two together to get articulation I drilled holes in the back of the U-shaped clevis and in the steel plate that closed off the frame on the rear end A 7/8-in pin through those two holes provided oscillation ” Matczak knew there would be room for the second rear axle and hydraulic drive under the front end of the tractor Only slight modifications were needed He had to trim out some of the hardware including the spring plate where a belly mower would normally attach and the connectors for a snowplow Hydraulic hoses to the drive unit presented another problem Normally they exited the drive forward to the valve body Moved ahead to the front of the tractor the hoses would still exit forward Not only would this interfere with the look but would also create extra hassle in connecting them “I jacked the drive unit up and ran an rpm gauge on the rim and checked its top speed ” says Matczak “It ran 7 mph in both forward and reverse This meant I could just flip it around and run it in reverse when the rear end was running forward The hoses now exited to the rear ” “The Case 222 has a lever that sits between the operator’s legs to move the drive into high low or neutral ” says Matczak “With a second drive at the front I had to fabricate a second control ” With it in place he can shift to 2-WD by putting either front or rear in neutral when turning Matczak also modified the steering He swung the rod that formerly went to the front end to the rear Once he had cut a foot and a half off he was able to attach it to a bracket he fabricated for one end of the rear axle Contact: FARM SHOW Followup Lee Matczak P O Box 44 229 Pine St Stillman Valley Ill 61084 ph 815 645-2432
To read the rest of this story, download this issue below or click
here to register with your account number.