You have reached your limit of 3 free stories. A story preview is shown instead.
To view more stories
(If your subscription is current,
click here to Login or Register.)
Self-Propelled "Power Plant" Runs Grain Augers
Today’s grain augers are so big – up to 16 in. in dia. and 100 ft. long – that it often requires a 150 to 170 hp tractor to operate them. Often, the tractor’s pto can’t handle the job, which can result in an expensive pto failure.
To solve the problem Don Perrion of Ipswich, S. Dak., recently finished
..........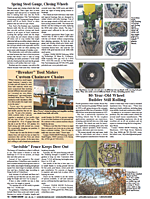
You must sign in, subscribe or renew to see the page.
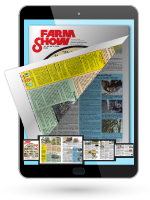
You must sign in, subscribe or renew to see the flip-book
Self-Propelled Power Plant Runs Grain Augers AUGERS Today’s grain augers are so big – up to 16 in in dia and 100 ft long – that it often requires a 150 to 170 hp tractor to operate them Often the tractor’s pto can’t handle the job which can result in an expensive pto failure
To solve the problem Don Perrion of Ipswich S Dak recently finished building a self-propelled 2-WD “pto power plant” that eliminates the need for a tractor
“It’s designed to operate big grain augers and to drive down the road to the next farm but it could also be used to operate hay grinders and other farm implements that normally require a big tractor equipped with pto ” says Perrion
The 2-WD rig is powered by a 170 hp Cat diesel engine hooked up to a large twin disc clutch that drives a 540 and 1 000 rpm gearbox There’s a pto shaft and drawbar on front allowing Perrion to push an auger up to the bin raise or lower it and operate it Hydraulic outlets located next to the pto shaft can be used to operate a belt conveyor Hydraulics are used to operate the machine’s power steering raise and lower the auger and drive the rear wheels The rig is even equipped with lights for unloading grain at night
There’s no seat The operator stands on a platform behind the steering wheel To go down the road he stands on one side of the steering wheel and turns the other way then puts the transmission in reverse The machine’s starter throttle and clutch are located next to the steering wheel while the pto and hydraulic controls mount on a panel box on one side of the machine
“I don’t have a lot of experience with it yet because I just finished building it last fall but I think it has a lot of advantages ” says Perrion “As I steer the auger I have a good view of the top of the grain bin It works better than sitting inside a tractor cab and looking back all the time I figured I don’t need a seat because I won’t spend much time there anyway It’s built with very strong components The engine steering system and hydraulics are all off a New Holland twin rotor combine while the gearbox is off a Case 4-WD tractor ”
He started with a Ford 1-ton ambulance which he bought at a salvage yard equipped with a 4-speed transmission and positraction rear end He stripped the vehicle down to the frame keeping the springs differential and rear wheels He had a machine shop make a driveshaft to connect the engine and differential The ambulance had been in an accident and didn’t have a front axle so he installed the front axle off a Dodge 1 1/2-ton pickup
He plans to build another self-propelled power plant this winter and mount a forklift on it “I’ll use the forklift to handle corn and soybean seed containers that farmers use to fill planters and drills ” says Perrion “These containers often contain 200 bu of seed corn and are too heavy to handle with some skid loaders I’m in the grain cleaning business and last spring I got several phone calls from people who wanted me to clean up spilled seed after their containers had tipped over My self-propelled rig has a much longer wheelbase than a skid loader and will be able to handle seed containers much more safely ”
Perrion says if there’s enough interest he’s willing to build similar units for others “It took me two months to make this one I spent about $20 000 ” he notes
Contact: FARM SHOW Followup Don Perrion P O Box 457 Ipswich S Dak 57451 ph 605 426-6276; cell 605 216-5763; pgisi@abe midco net
To read the rest of this story, download this issue below or click
here to register with your account number.